High-Performance Tape Slitting Machines
Featured Adhesive Tape Slitter Rewinder Machines
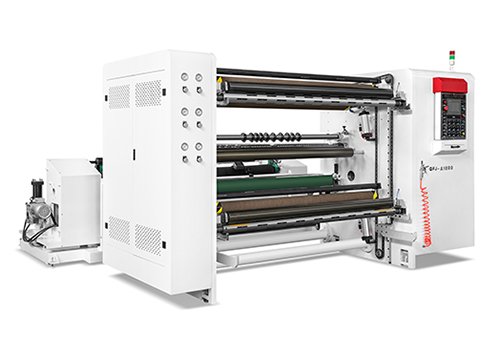
QFJ-A400 Horizontal High Speed Slitting Machine
- Key Specifications:
- Max Speed: 400m/min
- Min. Slitting Width: 30mm
- Unwinding Diameter 1200mm(Customizable)
- Rewinding Diameter 1000mm(Customizable)
- Key Specifications:
- Automatic unloading by chain
- Independent shaft free feeding
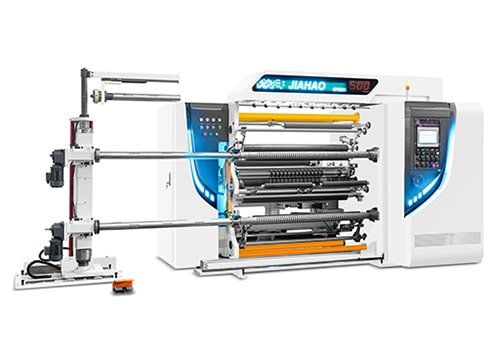
QFJ-A500 Horizontal High Speed Slitting Machine
- Key Specifications:
- Max Speed: 500m/min
- Min. Slitting Width: 20mm
- Unwinding Diameter 800mm(Customizable)
- Rewinding Diameter 600mm(Customizable)
- Key Specifications:
- Small Footprint of connected structures
- 4 Sets Servo Motor Controll
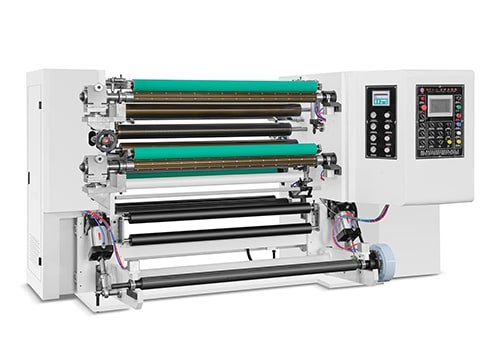
QFJ-B200 Vertical Slitting Machine
- Key Specifications:
- Max Speed: 200m/min
- Min. Slitting Width: 20mm
- Unwinding Diameter 700mm(Customizable)
- Rewinding Diameter 400mm(Customizable)
- Key Specifications:
- Small Footprint of connected structures
- 4 Sets Servo Motor Controll
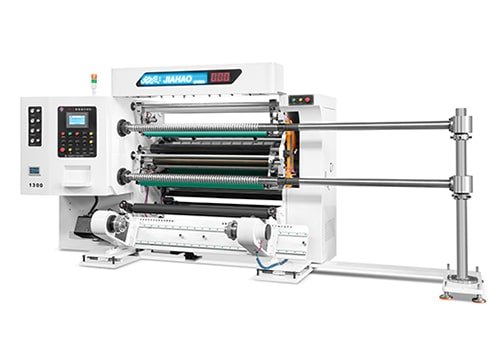
QFJ-B500 Vertical High Speed Slitting Machine
- Key Specifications:
- Max Speed: 500m/min
- Min. Slitting Width: 30mm
- Unwinding Diameter 750mm(Customizable)
- Rewinding Diameter 450mm(Customizable)
- Key Specifications:
- Automatic unloading by chain
- Independent shaft free feeding
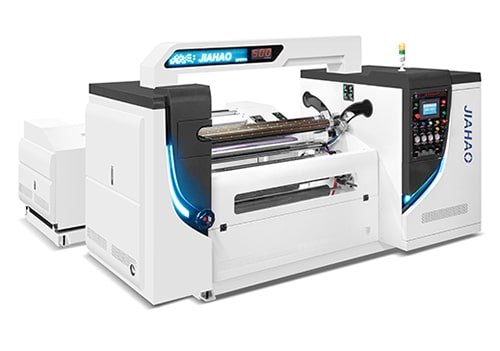
QFJ-C500 Surface Winding High Speed Slitting Machine
- Key Specifications:
- Max Speed: 500m/min
- Min. Slitting Width: 20mm
- Unwinding Diameter 1000mm(Customizable)
- Rewinding Diameter 600mm(Customizable)
- Key Specifications:
- Small Footprint of connected structures
- 4 Sets Servo Motor Controll
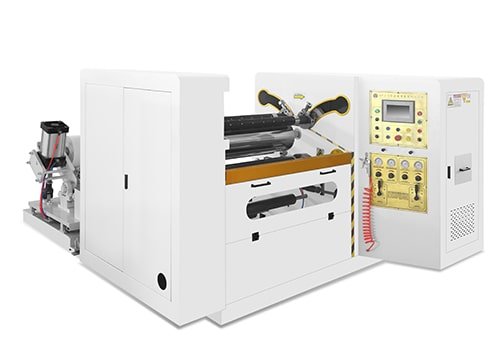
QFJ-C200 Series Surface Winding Slitting Machine
- Key Specifications:
- Max Speed: 200m/min
- Min. Slitting Width: 10mm
- Unwinding Diameter 1000mm(Customizable)
- Rewinding Diameter 600mm(Customizable)
- Key Specifications:
- Small Footprint of connected structures
- 4 Sets Servo Motor Controll
Specialized Tape Slitting Applications
BOPP Tape Slitting
High-efficiency machines designed for BOPP packaging tapes, featuring accurate width control, stable roll length, and turret rewind for nonstop production.
Industrial Adhesive Tapes
Durable slitting systems built for double-sided, foam, foil, and duct tapes, capable of handling thick materials and higher web tension with precision.
Masking & Painter’s Tapes
Precision slitting solutions for masking and painter’s tapes, ensuring clean edges and no adhesive bleed—ideal for professional paint and finish work.
Medical & Specialty Tapes
Cleanroom-compatible equipment designed for medical, surgical, and specialty tapes, with hygienic material handling and strict process control.
Custom Tape Converting
Flexible machines for custom sizes, short runs, and diverse core requirements—plus contract slitting and technical services for niche markets.
Advanced Slitting Technology for Adhesive Tapes
From Jumbo Roll to Finished Tape: A Complete Slitting Workflow
1. Precision Unwinding Control
2. Accurate Web Guiding & Tension Management
3. Flexible Slitting Options
4. Adaptive Rewinding Technology
5. Continuous Production with Auto Roll Change
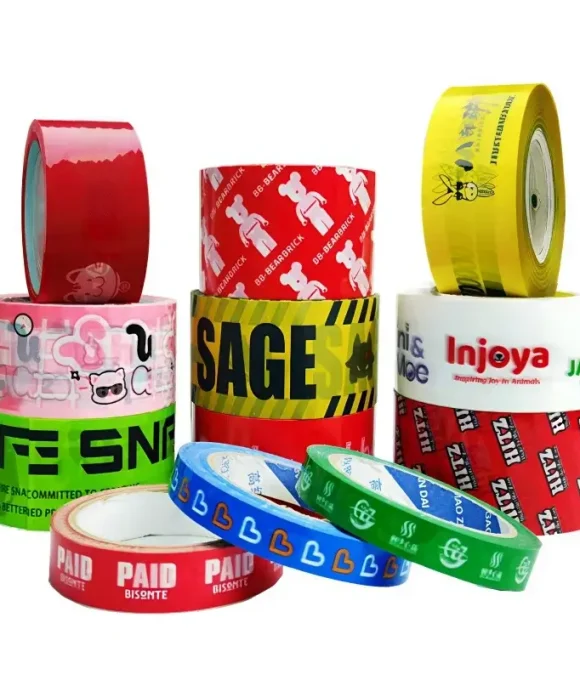
Turning Tape Slitting Challenges into Precision Performance
Eliminate Telescoping & Edge Damage
Our tape slitter rewinders feature closed-loop tension control and laser-guided web alignment, ensuring clean, tight rolls free of adhesive bleed or irregularities. Achieve uniform rolls essential for reliable application performance.
Maximize BOPP Slitting Efficiency
Fully automatic systems with PLC control, recipe memory, and turret rewinders (4-shaft) slash labor costs by 30%+ while enabling continuous high-volume output—ideal for packaging tape operations.
Slit Specialty Tapes Without Custom Costs
From double-sided adhesives to thick industrial tapes, our modular blade systems (razor/shear/score) adapt to any backing or adhesive. Get tailored solutions without custom engineering costs.
Reduce Core Handling Downtime
Automatic core loading/unloading and precision shaftless unwind systems minimize manual intervention, accelerating roll changes and reducing operator fatigue.
Optimize Blade Life for Aggressive Adhesives
Hardened blade cartridges and adhesive-resistant coatings extend service intervals by 2–3× when slitting silicone-based or heavy-tack tapes, lowering consumable costs.
Customized Tape Slitting Solutions
What We Customize:
Machine Configuration
Custom-built frames, unwind/rewind positions, and web paths optimized for adhesive behavior and factory space. Prevents telescoping and roll deformation.
Slitting System
Precision razor, shear, or score blades selected for backing thickness (film/paper/foam), adhesive tack, and edge-cleanliness requirements.
Rewinding Technology
Turret rewinders (4-shaft), contact/non-contact winding, or coreless systems—engineered to prevent adhesive transfer and ensure roll tightness.
Web Width & Roll Size
Handles tape widths from 50mm to 1800mm and jumbo rolls up to Ø1200mm. Supports narrow medical tapes to wide industrial rolls.
Tension & Control Accessories
Closed-loop tension sensors, low-friction rollers, anti-static systems, and adhesive-resistant coatings for dust-free, jam-proof operation.
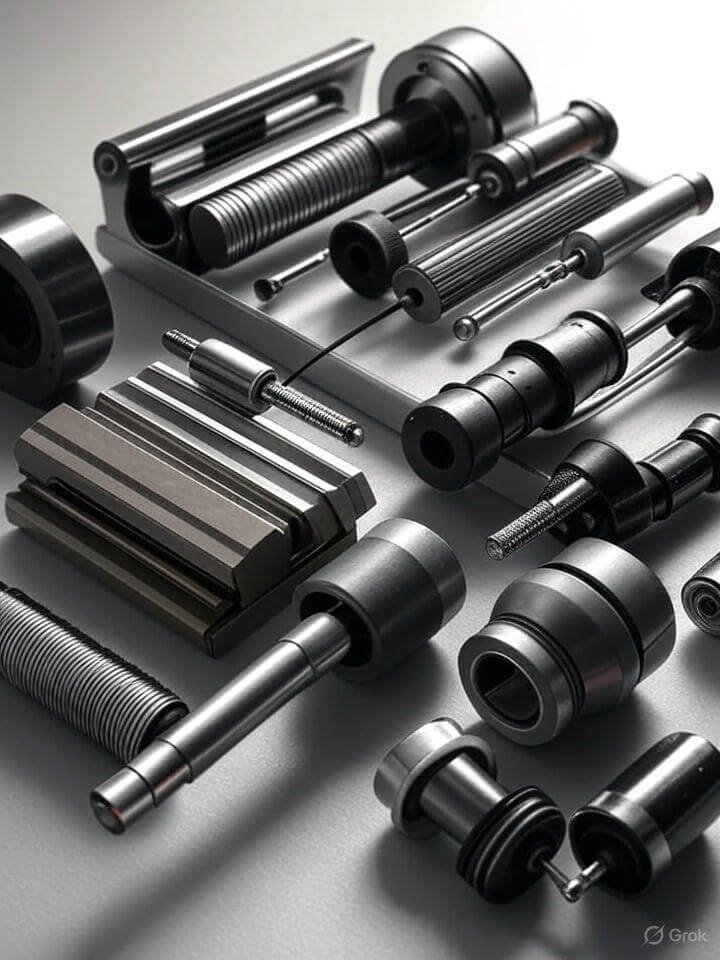
Our Manufacturing Prowess & R&D Capabilities
Production Scale & Qualifications
- Factory Area: Over 10,000 square meters dedicated to manufacturing high-precision slitters.
- Annual Capacity: 200+ high-quality slitting machines for various materials.
- Certifications: ISO 9001, CE, Multiple Patents for advanced slitting technology.
R&D and Innovation
- Dedicated R&D Team: 12+ experienced engineers focused on slitter machine innovation.
- Technical Collaborations: Partnering with leading universities and research institutes for cutting-edge slitting solutions.
- Innovation Focus: Continuous development of intelligent and automated slitting and rewinding machines for paper, film, and foil.
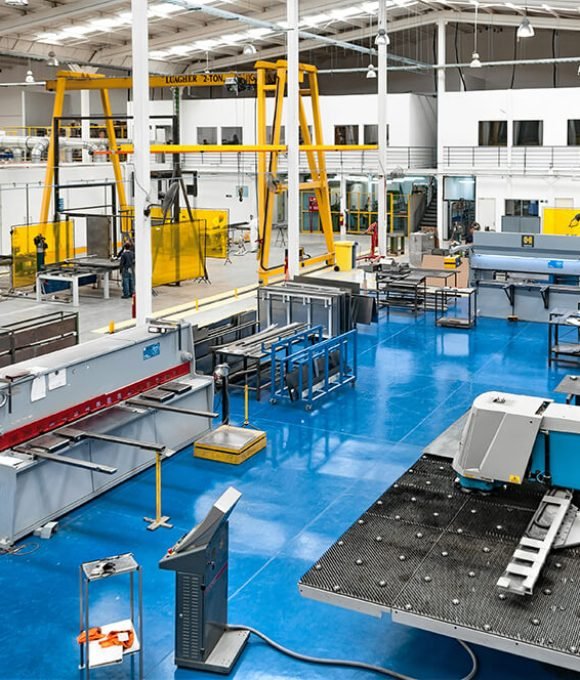
Quality Certifications
- ISO 9001:2015 Quality Management System
- CE Certification for European Market Compliance
- SGS Audited Supplier Status for all our slitting and rewinding machines.
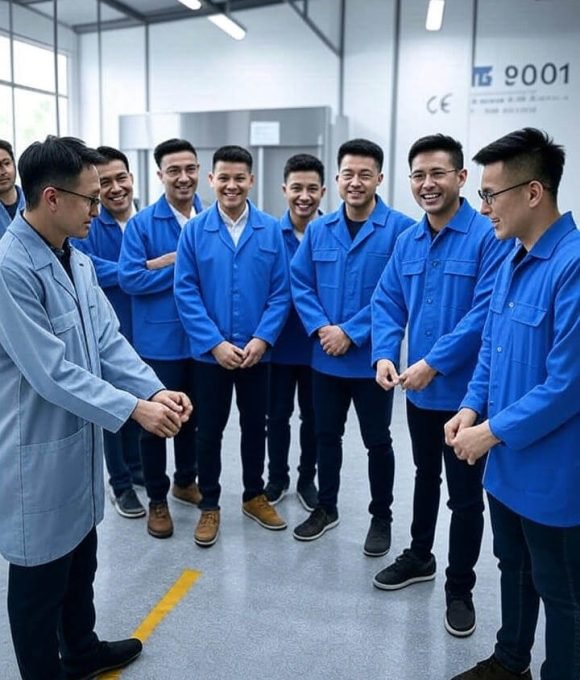
Unmatched After-Sales Service & Support
We have a growing network of overseas service points and authorized agents in Southeast Asia, Europe, and the Americas to ensure prompt local support for your slitting and rewinding machine.
Our Service Commitments
- 24/7 remote technical support and troubleshooting for your slitter.
- Scheduled preventive maintenance programs and on-site servicing for all slitting machines.
- Comprehensive operator training and detailed maintenance guides (e.g., slitter slider lubrication, film slitter knife care).
12+
Years of Experience
500+
Customer Cases
20+
Patented Technologies
98%
Customer Satisfaction
Transforming Tape Production in the Gulf: Al-Najjar Industries' Journey
Revolutionizing Adhesive Manufacturing in Dubai's Harsh Climate
When Khalid Al-Najjar took leadership of his family’s 25-year-old adhesive tape business in 2021, he faced mounting pressure from international competitors. Dubai’s extreme temperatures caused adhesive bleeding in their BOPP packaging tapes, while their aging European slitting equipment couldn’t handle the region’s growing demand for specialty masking tapes needed by the booming construction industry. Production waste had reached 18%, threatening their position as a leading UAE tape supplier.
The Desert Challenge: Climate-Sensitive Tape Solutions
Traditional slitting machines faltered in Dubai’s 45°C summers where:
- Adhesive viscosity became unpredictable during high-speed rewinding
- Dust storms contaminated precision slit edges
- Humidity shifts caused core slippage in jumbo rolls
Custom Engineering for Gulf Conditions
Our engineers conducted onsite assessments at Al-Najjar’s Jebel Ali facility, resulting in these customizations:
- Thermo-Regulated Rewinding – Chilled contact rollers maintaining 22°C adhesive temperature
- Sand-Proof Enclosure – IP65 sealed slitting cabin with positive air pressure
- Desert-Grade Blades – Diamond-coated shear knives resisting abrasive particle wear
- Quranic Verse Integration – Arabic interface with production tracking aligned with prayer times
Operational Breakthroughs in Record Time
Within three months of installation:
Metric | Before | After |
---|---|---|
Masking Tape Output | 12 tons/day | 28 tons/day |
Edge Defects | 23% rejection | 1.2% rejection |
Energy Consumption | 18 kW/hr | 9 kW/hr |
Specialty Tape Range | 3 types | 11 types |
Regional Market Dominance Achieved
By 2023, Al-Najjar Industries had:
- Secured exclusive contracts with Dubai Expo City construction projects
- Become the primary supplier for Saudi NEOM infrastructure development
- Launched Halal-certified medical tapes for GCC hospitals
A Partnership Driving Regional Industrialization
Today, our collaboration continues with:
- On-site technician academy training Emirati engineers
- Co-development of solar-reflective adhesive tapes for Middle East rooftops
- Plans for the region’s first fully automated tape slitting facility in Abu Dhabi
What types of adhesive tapes can be slit using your tape slitting machines?
What slitting methods are available for different tape types?
How do you ensure clean and straight edges when slitting adhesive tape?
Can your machines handle jumbo rolls and automatic roll changes?
What is the typical width range and cutting tolerance?
Do you offer fully automatic BOPP tape slitting machines?
Complete Guide to Choosing an Adhesive Tape Slitter Rewinder Machine
Adhesive tape slitter rewinder machines are essential for converting jumbo rolls of tape into smaller, market-ready sizes. Whether you manufacture BOPP packaging tape, masking tape, double-sided tape, or specialty adhesive products, choosing the right slitter rewinder can improve your production efficiency, reduce waste, and ensure high-quality rolls. This guide will help you evaluate critical technical and business factors before investing in a tape slitting machine.
1. Understanding Your Tape Production Requirements
Start by clarifying your product specifications and operational needs:
- Type of Tape: Identify the adhesive tape material—BOPP, PVC, kraft paper, double-sided, foam, etc.—since each may need different blade types and tension settings.
- Jumbo Roll Size: Most tape slitters handle rolls with widths up to 1600 mm and diameters of 1000–1200 mm.
- Finished Roll Dimensions: Define your slitting widths (often 12 mm and above) and core sizes (1″, 1.5″, or 3″).
- Required Output Speed: Speed demands vary based on whether you are serving large-volume retail orders or industrial specialty markets.
2. Key Machine Features to Evaluate
The performance of a tape slitter rewinder directly impacts productivity, safety, and finished roll quality. Key features to consider include:
- Slitting Method: Razor blade slitting is common for BOPP and PET tapes; rotary blades or shear knives are better for thicker or reinforced materials.
- Rewinding Options: Options include surface rewinding, center rewinding, and duplex rewinding, depending on tape type and roll stability.
- Tension Control: Consistent and adjustable tension is critical for avoiding wrinkles, bubbles, or telescoping in adhesive materials.
- Edge Alignment & Tracking: Accurate edge guiding ensures smooth rolls and reduces waste, especially for printed or branded tapes.
- Automation: Features like auto blade positioning, meter counters, turret rewinders, and touch-screen control systems improve efficiency and reduce operator fatigue.
3. Selecting the Right Machine Manufacturer
A reliable tape slitting machine supplier can ensure stable production and long-term service. Look for:
- Industry Expertise: Choose suppliers with proven success in adhesive tape manufacturing, not just general-purpose slitting.
- Customization Ability: Whether you need multi-lane slitting, jumbo roll loaders, or non-stop turret systems, customization should be available.
- Local Support & Spare Parts: For markets like Vietnam or Southeast Asia, check if local agents or service centers are available.
- Training & Commissioning: Ensure the supplier offers installation guidance, operator training, and clear manuals.
4. Cost Considerations and ROI
Evaluating price alone may be misleading. Factor in these elements for a full ROI picture:
- Machine Price: Entry-level tape slitters may cost less, but lack automation, while high-end models offer better long-term returns.
- Consumables & Maintenance: Blades, core loaders, pneumatic shafts, and bearings all contribute to running costs.
- Downtime & Scrap: High-precision machines reduce tape waste and downtime due to roll defects.
- Labor Requirements: Automation can reduce the number of operators needed, particularly for 24/7 operations.
5. Other Important Factors
When planning your tape slitting operations, don’t overlook these critical points:
- Safety Features: Ensure the machine includes guards, emergency stops, and interlock systems.
- Core & Shaft Compatibility: Make sure the machine supports all your required core diameters and shaft types.
- Adhesive Control: Consider anti-adhesive rollers or tension zones that prevent sticky buildup on blades and rollers.
- Dust Collection: Particularly useful for paper masking tapes or foam tapes that generate slitting dust.
6. Market Trends and Future Opportunities
The adhesive tape industry is expanding across various sectors. Stay ahead by considering these trends:
- E-commerce Boom: Growing demand for printed and branded BOPP packaging tape requires efficient, high-output slitters.
- Eco-Friendly Tapes: Paper-based and biodegradable adhesive tapes are growing—machines must adapt to new materials.
- Industrial Tape Growth: Double-sided foam, copper, and protective tapes are in demand, requiring robust, high-precision machines.
- Vietnam as a Production Hub: With rising tape exports and investments, localizing production in Vietnam offers strong growth potential.
Tape Slitter Machine Comparison Table
Evaluation Factor | Details | Why It Matters |
---|---|---|
Material Compatibility | BOPP, PVC, foam, kraft, PET | Ensures clean slitting without adhesive issues |
Rewinding Method | Surface, center, or turret rewind | Impacts roll tightness and speed |
Tension & Blade Control | Precision adjustment & tracking | Affects finished roll quality and yield |
Automation Level | Manual, semi-auto, or fully automatic | Improves efficiency and reduces labor cost |
Customization Options | Core sizes, slit widths, loader systems | Adapts to your specific product line |
Investing in the right adhesive tape slitter rewinder machine is essential for maximizing production output and maintaining consistent product quality. From understanding material compatibility to evaluating supplier reliability and automation features, each factor plays a role in your overall success. With growing global demand for adhesive tapes and increasing automation trends, now is the perfect time to upgrade or expand your slitting capabilities—especially if you’re targeting competitive markets like Vietnam or Southeast Asia.