Precision Label Rewinders & Slitting Machines
Featured Label Slitter Rewinder Machines
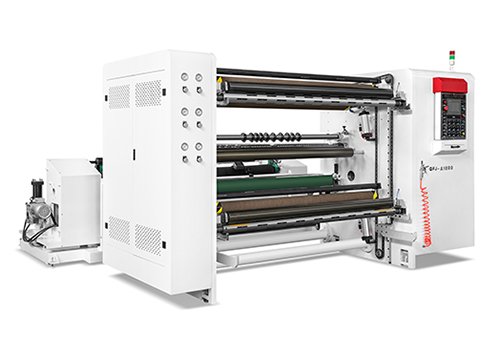
QFJ-A400 Horizontal High Speed Slitting Machine
- Key Specifications:
- Max Speed: 400m/min
- Min. Slitting Width: 30mm
- Unwinding Diameter 1200mm(Customizable)
- Rewinding Diameter 1000mm(Customizable)
- Key Specifications:
- Automatic unloading by chain
- Independent shaft free feeding
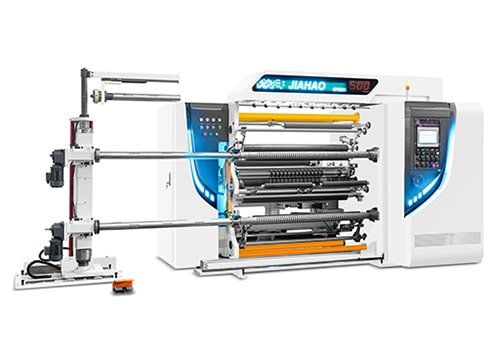
QFJ-A500 Horizontal High Speed Slitting Machine
- Key Specifications:
- Max Speed: 500m/min
- Min. Slitting Width: 20mm
- Unwinding Diameter 800mm(Customizable)
- Rewinding Diameter 600mm(Customizable)
- Key Specifications:
- Small Footprint of connected structures
- 4 Sets Servo Motor Controll
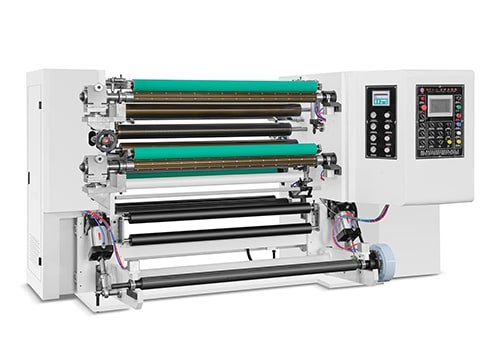
QFJ-B200 Vertical Slitting Machine
- Key Specifications:
- Max Speed: 200m/min
- Min. Slitting Width: 20mm
- Unwinding Diameter 700mm(Customizable)
- Rewinding Diameter 400mm(Customizable)
- Key Specifications:
- Small Footprint of connected structures
- 4 Sets Servo Motor Controll
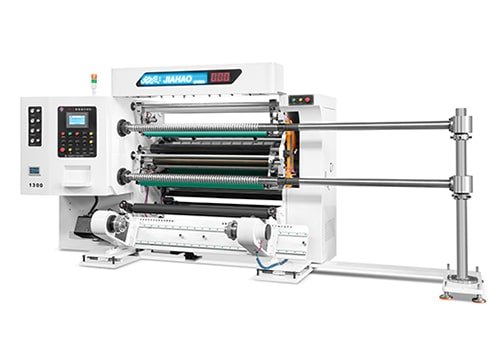
QFJ-B500 Vertical High Speed Slitting Machine
- Key Specifications:
- Max Speed: 500m/min
- Min. Slitting Width: 30mm
- Unwinding Diameter 750mm(Customizable)
- Rewinding Diameter 450mm(Customizable)
- Key Specifications:
- Automatic unloading by chain
- Independent shaft free feeding
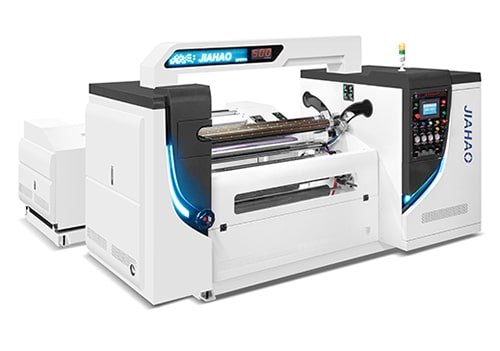
QFJ-C500 Surface Winding High Speed Slitting Machine
- Key Specifications:
- Max Speed: 500m/min
- Min. Slitting Width: 20mm
- Unwinding Diameter 1000mm(Customizable)
- Rewinding Diameter 600mm(Customizable)
- Key Specifications:
- Small Footprint of connected structures
- 4 Sets Servo Motor Controll
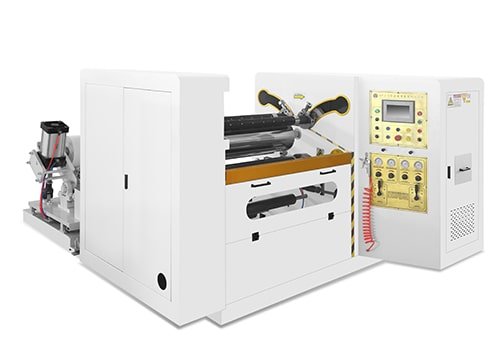
QFJ-C200 Series Surface Winding Slitting Machine
- Key Specifications:
- Max Speed: 200m/min
- Min. Slitting Width: 10mm
- Unwinding Diameter 1000mm(Customizable)
- Rewinding Diameter 600mm(Customizable)
- Key Specifications:
- Small Footprint of connected structures
- 4 Sets Servo Motor Controll
Specialized Label Slitting Applications
Finished Label Roll Rewinding
High-efficiency rewinders for converting large master rolls into smaller, application-ready label rolls. Options include fully automatic models with precise tension control and smooth roll formation.
Label Stock Slitting
Precision slitting systems designed to convert wide label stock into multiple narrow rolls. Delivers accurate width control and maximized material usage for diverse label formats.Ideal for: Flexible label production from a single master roll.
Slitting & Rewinding with Inspection
Inspection-integrated machines with vision systems for defect detection, label counting, and quality control. Ensures flawless rolls before final dispatch.Ideal for: Zero-defect applications requiring strict quality assurance.
Narrow Web Converting
Advanced equipment for processing ultra-narrow web materials used in electronics, pharma, and specialty packaging. Offers high-precision slitting and gentle web handling. Ideal for: Delicate and miniature labels needing accurate conversion.
Label Unwinding & Dispensing
Reliable unwinders and feeders for consistent label delivery to printers, applicators, and downstream systems. Available in manual, semi-auto, and fully automatic setups. Ideal for: Seamless integration into printing, labeling, or packaging lines.
Advanced Slitting Technology for Labels
End-to-End Label Slitting & Rewinding Workflow
1. Tension-Controlled Unwinding
2. Precision Web Guiding
3. Optional Inline Inspection
4. Versatile Slitting Mechanisms
5. Automated Trim Waste Removal
6. High-Accuracy Rewinding
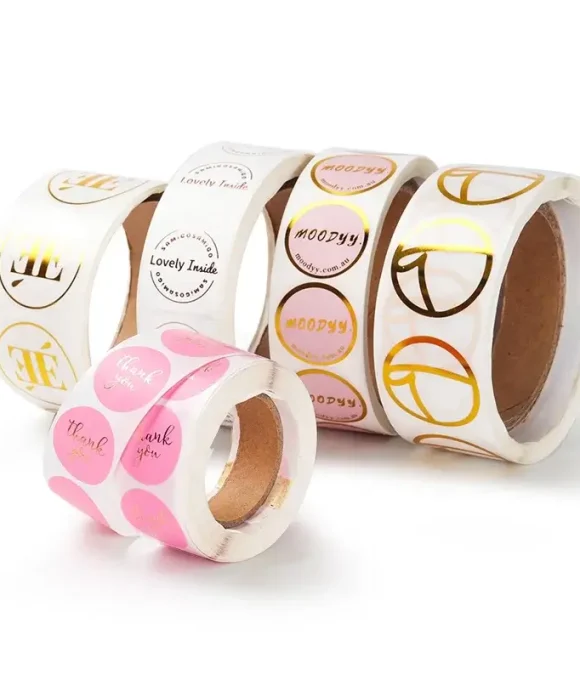
Turning Your Label Slitting Challenges into Smart Solutions
Achieve Perfect Roll Quality for Automatic Labeling
Inconsistent winding—like telescoping or loose rolls—can disrupt automated lines. Our label rewinders feature precise tension control and CNC-machined cores to deliver tightly wound, uniform rolls ready for high-speed label applicators.
Produce Ultra-Narrow Label Slits with Precision
Standard slitting setups often struggle with tight tolerances. DJH label slitters utilize shear or razor blades, low-runout shafts, and precision guiding systems to deliver accurate, narrow slits—even for micro-label formats.
Ensure 100% Quality with Automated Defect Detection
Manual inspection is slow and unreliable. Our inspection slitter rewinders integrate high-speed vision systems to detect defects in real time, isolate faulty segments, and guarantee consistent roll quality.
Minimize Label Waste During Trim Removal
Uncontrolled edge trimming can waste material and damage good labels. Our machines feature dedicated trim removal systems that cleanly extract matrix waste without affecting usable labels—boosting yield and process cleanliness.
Handle Delicate Materials Without Damage
Thin films and fragile label stocks demand gentle handling. DJH systems use dancer rollers, non-slip web paths, and adaptive tension control to prevent tearing, curling, or material stress during slitting and rewinding.
Customized Label Slitting & Rewinding Solutions
What We Customize:
Machine Configuration
Custom frame sizes, unwind/rewind directions, and web routing adapted to label stock properties and factory layout. Ensures smooth feeding and eliminates issues like telescoping or misalignment.
Slitting System
Choose from razor, shear, or crush cut blades—each selected based on label thickness, liner material (paper/film), and required slit accuracy. Designed for clean edges with minimal dust or fray.
Rewinding Technology
Turret rewinders, differential shafts, or tension-sensitive winding systems. Engineered for tight, uniform rolls that are compatible with downstream applicators and printers—without core slippage or wrinkling.
Web Width & Roll Size
Supports label webs from 20mm to 1600mm wide, with jumbo roll handling up to Ø1000mm. Ideal for anything from tiny RFID or vial labels to large-format product labels.
Tension & Control Accessories
Integrated tension sensors, dancer rollers, static elimination units, and adhesive-friendly coatings—ensuring smooth, contamination-free operation even with sensitive or high-tack label materials.
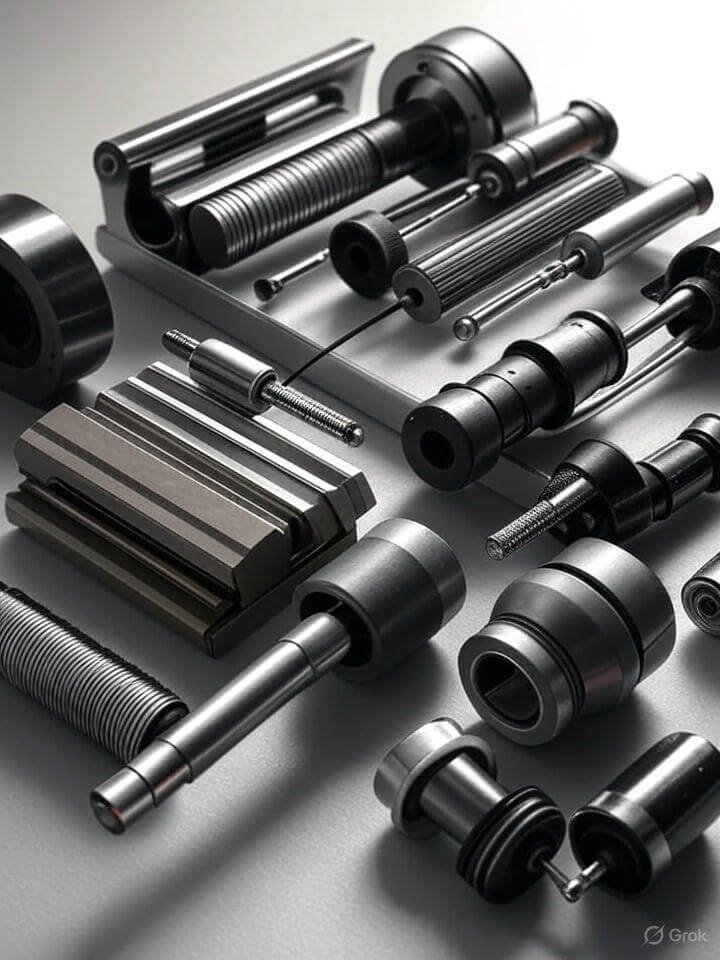
Our Manufacturing Prowess & R&D Capabilities
Production Scale & Qualifications
- Factory Area: Over 10,000 square meters dedicated to manufacturing high-precision slitters.
- Annual Capacity: 200+ high-quality slitting machines for various materials.
- Certifications: ISO 9001, CE, Multiple Patents for advanced slitting technology.
R&D and Innovation
- Dedicated R&D Team: 12+ experienced engineers focused on slitter machine innovation.
- Technical Collaborations: Partnering with leading universities and research institutes for cutting-edge slitting solutions.
- Innovation Focus: Continuous development of intelligent and automated slitting and rewinding machines for paper, film, and foil.
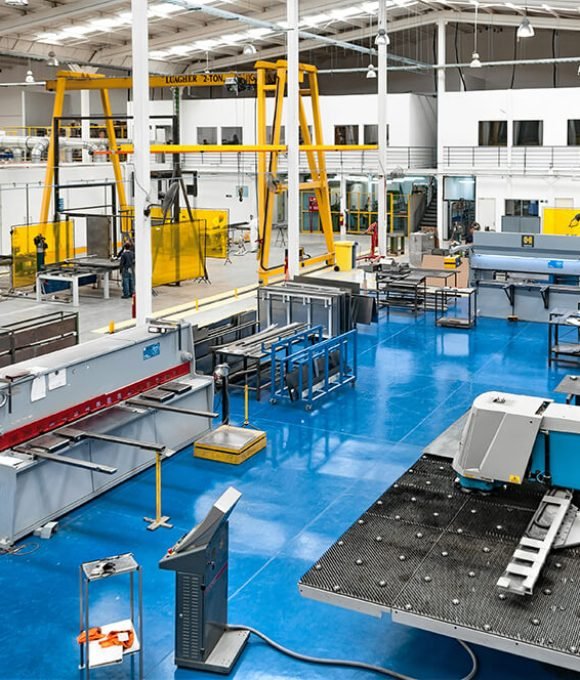
Quality Certifications
- ISO 9001:2015 Quality Management System
- CE Certification for European Market Compliance
- SGS Audited Supplier Status for all our slitting and rewinding machines.
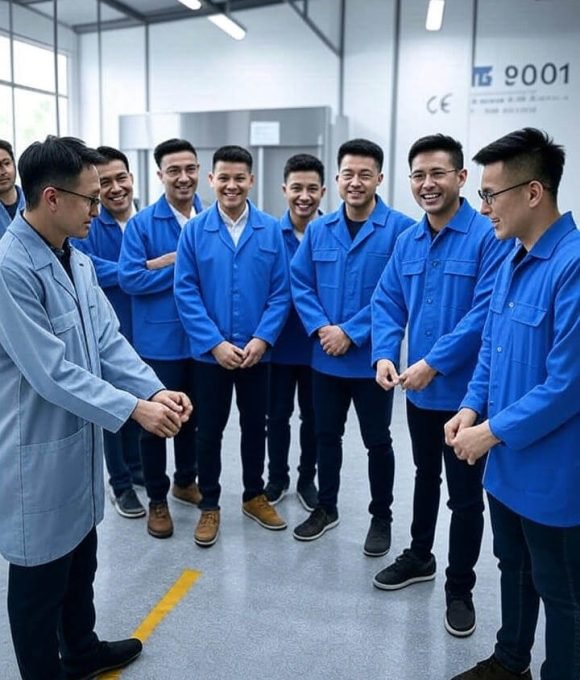
Unmatched After-Sales Service & Support
We have a growing network of overseas service points and authorized agents in Southeast Asia, Europe, and the Americas to ensure prompt local support for your slitting and rewinding machine.
Our Service Commitments
- 24/7 remote technical support and troubleshooting for your slitter.
- Scheduled preventive maintenance programs and on-site servicing for all slitting machines.
- Comprehensive operator training and detailed maintenance guides (e.g., slitter slider lubrication, film slitter knife care).
12+
Years of Experience
500+
Customer Cases
20+
Patented Technologies
98%
Customer Satisfaction
Case Study: Customized Label Slitting & Rewinding Solution for a Turkish Converter
Client Overview
Location: Istanbul, Turkey
Industry: Pressure-Sensitive Label Converting & Packaging
Application: Barcode Labels, Clear-on-Clear Labels, Variable Data Printing
Project Background
A fast-growing label converter in Istanbul needed to upgrade its slitting and rewinding capabilities. Their increasing production volume, combined with diverse label types, demanded higher accuracy, better automation, and tighter roll quality.
Challenges
- Roll inconsistency (telescoping, loose winding) disrupted automated label application.
- Difficulty slitting narrow labels (<15mm) with precision on standard machines.
- Manual tension adjustment and lengthy setup time reduced efficiency.
- Quality defects were only detected after rewinding, leading to high waste.
- Production bottlenecks due to slow changeovers and limited automation.
Our Solution
DJH Machinery engineered a fully customized slitting & rewinding system tailored to the client’s workflow, material types, and space limitations.
Key Features
- Modular Machine Frame: Space-saving layout with optimized web path for film and paper labels.
- Dual Slitting Options: Razor and shear blade setup with ±0.1mm width tolerance.
- Closed-Loop Tension Control: Servo-driven system with automatic calibration per material type.
- Inline Vision Inspection: Real-time defect detection and automatic flagging of faulty labels.
- Turret Rewinder (4-Shaft): Seamless roll changeovers with adjustable torque settings.
- Multi-Language Interface: User-friendly HMI with Turkish language support and job memory.
Results
- 40% increase in production capacity
- 98% reduction in roll rejections
- 60% faster changeover times
- No more telescoping or winding issues
- Fully integrated with downstream applicator systems
Client Testimonial
“Before DJH, we were constantly fixing winding issues and dealing with waste. Now we run long jobs with fewer stoppages and better quality control. Their team understood our exact materials and delivered a system that fits our growth.”
— Production Director, Istanbul Facility
What is a label rewinder and what does it do?
What is the difference between a rewinder and a slitter?
Can I use a label rewinder with any label printer?
What core sizes do label rewinders support?
What are the typical speed and roll capacity of a label rewinder?
Can a slitter handle different label sizes and materials?
Complete Guide to Choosing a Label Slitter Rewinder Machine
Label slitter rewinder machines are critical in converting printed or blank label rolls into precise, usable sizes for further processing or application. Whether you’re producing barcode labels, film-based labels, or variable data printing applications, choosing the right machine helps ensure efficiency, accuracy, and quality. This guide outlines the major factors you need to consider before purchasing a label slitter rewinder machine.
1. Understanding Your Label Production Requirements
Begin with a detailed analysis of your production workflow:
- Label Type: Paper, PET, PE, PP, clear-on-clear, or multi-layer laminates—each requires specific blade types and tension control settings.
- Jumbo Roll Dimensions: Standard label slitters support up to 1600 mm web width and diameters of 1000–1200 mm.
- Finished Roll Size: Define slit widths (as narrow as 10 mm for barcode or micro-labels) and core sizes (1″ to 3″).
- Output Speed: Speeds of 150–300 m/min are typical depending on print type, substrate, and label complexity.
2. Key Machine Features to Evaluate
Your machine’s features directly affect your throughput and label quality. Important features include:
- Slitting System: Razor blades are ideal for film labels, shear knives suit thick or laminated structures.
- Rewinding Options: Contact or non-contact winding methods prevent adhesive transfer or distortion.
- Tension Management: Servo-controlled tension ensures tight, even rolls without telescoping.
- Edge Guiding: Sensors and tracking systems improve accuracy and minimize waste.
- Automation: Automatic tension setting, job memory, turret rewinding, and defect flagging speed up production and reduce operator errors.
3. Selecting the Right Machine Manufacturer
Choose a supplier who understands label-specific requirements and offers full support:
- Label Industry Experience: Not all slitter manufacturers specialize in self-adhesive label processing.
- Customization: Look for vendors who can adapt blade positioning, unwind configurations, and inspection systems to your needs.
- Service Network: Ensure spare parts and technical service are available in your region (e.g., Turkey, Southeast Asia).
- After-Sales Support: Commissioning, staff training, and manuals should be included in the package.
4. Cost Considerations and ROI
A reliable label slitter rewinder can deliver returns beyond initial pricing. Evaluate:
- Machine Cost: Entry-level options suit simpler labels, but high-speed, automated models may offer better value over time.
- Operating Costs: Blade wear, static eliminators, vacuum systems, and maintenance time add to long-term investment.
- Downtime & Waste: Machines with defect inspection and precise tension control lower scrap rates.
- Labor Efficiency: Automated systems reduce operator workload and training time.
5. Other Important Factors
- Label Inspection: Integrate with vision systems for quality assurance and defect detection.
- Anti-Static Features: Particularly important for film-based labels or high-speed runs.
- Roll Change Efficiency: Turret rewinders or automatic core loaders improve productivity.
- Dust Collection: Keeps sensors and blades clean, improving long-term reliability.
6. Market Trends and Future Opportunities
- Smart Labels: RFID or QR labels require high-accuracy slitting and defect tracking.
- Sustainable Labels: Paper-based and recyclable substrates call for updated cutting systems.
- Short Run Jobs: Label converters increasingly require quick setup machines for variable data printing.
- Growing Markets: Countries like Turkey and Vietnam are expanding label exports, demanding higher slitting capacity and quality.
Label Slitter Machine Comparison Table
Evaluation Factor | Details | Why It Matters |
---|---|---|
Material Compatibility | Paper, PET, PE, clear-on-clear, multilayer | Ensures clean slitting for all label types |
Rewinding Method | Contact, non-contact, turret | Prevents adhesive transfer and maintains roll shape |
Tension Control | Closed-loop, servo-driven | Maintains roll quality and avoids stretching |
Automation | Blade positioning, inspection, job memory | Improves throughput and reduces manual errors |
Customization | Roll size, web width, vision systems | Adapts machine to your label product range |
Choosing the right label slitter rewinder machine involves understanding both your product requirements and the latest industry technologies. From tension control and slitting accuracy to automation and inspection features, every element impacts your production efficiency. With growing global demand for high-quality label rolls, investing in a versatile and well-supported slitter is key to staying competitive in fast-moving markets like Turkey, Southeast Asia, and beyond.