Curved (Bow) Rollers for Effective Wrinkle Removal
Featured Curved (Bow) Rollers
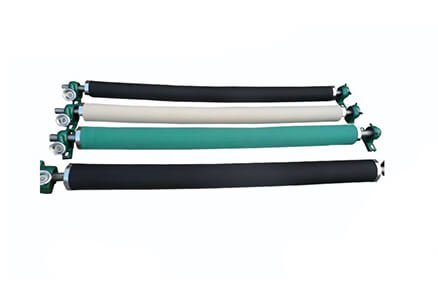
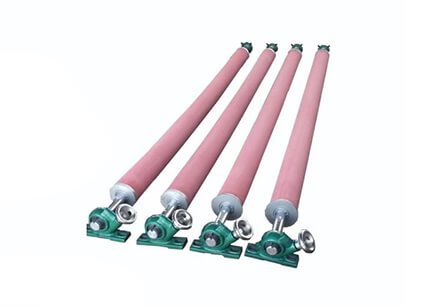
Product Specifications – Curved (Bow) Rollers | ||
---|---|---|
Model | Roller Face Diameter (mm) | Maximum Overall Length (mm) |
R80 | 80 | 1000 |
R100 | 100 | 2000 |
R125 | 125 | 3000 |
R150 | 150 | 4000 |
R180 | 180 | 5000 |
R200 | 200 | 6000 |
Efficient Web Handling with Precision Curved (Bow) Rollers
Universal Web Spreading
Expands the web evenly to eliminate slack edges and stabilize tension—critical before coating, printing, or slitting. Benefit: Delivers a flat, stable web and reduces process defects.
Wrinkle Removal for Various Materials
Effectively removes wrinkles, folds, and creases from paper, plastic films, textiles, foil, and nonwoven substrates. Benefit: Enhances product quality and reduces material waste.
Separation After Slitting
Curved rollers guide and separate slit webs to avoid interleaving and tangling during rewinding. Benefit: Ensures clean, independent roll formation and higher productivity.
Correcting Web Camber or Distortion
Adjustable crown designs gently realign distorted or cambered webs by applying differential tension. Benefit: Improves web alignment and supports consistent downstream processing.
Precision Engineered for Web Control: Inside Curved (Bow) Roller Design
1. Precision-Curved Core Geometry
2. Stress-Free Rubber or Metal Covering
3. Smooth, Calibrated Finishing
4. Function-Oriented Material Pairing
5. Versatile Performance in Web Processing
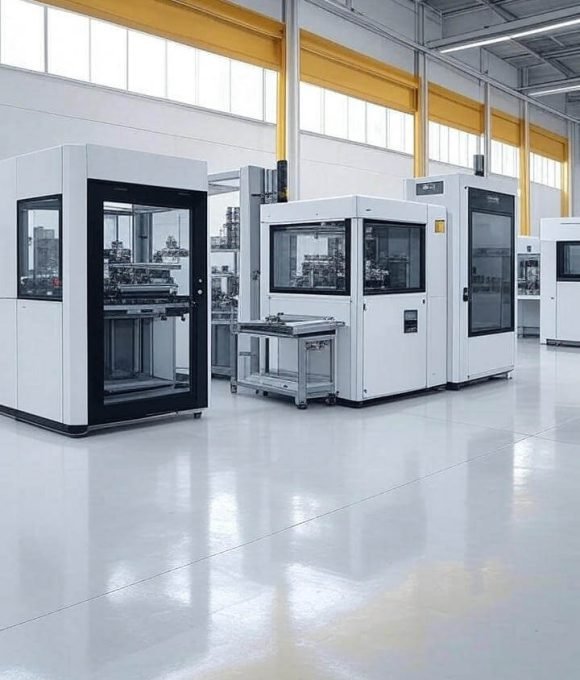
Get Your Free Sample Today
What Are Curved (Bow) Rollers?
Curved rollers are specialized cylindrical components with a subtle, intentional curvature along their length. This bow-shaped design enables them to spread web materials—such as paper, fabric, or plastic films—laterally as they pass over the roller, effectively smoothing out wrinkles and maintaining consistent tension.
The operational principle of curved rollers relies on their geometry: the bowed profile creates varying path lengths across the roller’s surface, with the center path being longer than the edges. This differential stretches the material outward, correcting distortions and ensuring uniform processing.
Different Types and Specifications of Curved Rollers
Fixed Bow Rollers
These have a permanent curvature, ideal for consistent, predictable web handling tasks. Bow heights typically range from 0.5% to 2% of the roller’s width.
Variable Bow Rollers
Featuring adjustable curvature, these rollers adapt to changing material properties or process conditions, offering versatility.
Sectional Bow Rollers
Composed of multiple segments, these allow for differential rotation, suited for wide or uneven webs.
Coated Bow Rollers
With surfaces like rubber or silicone, these enhance traction for slippery materials.
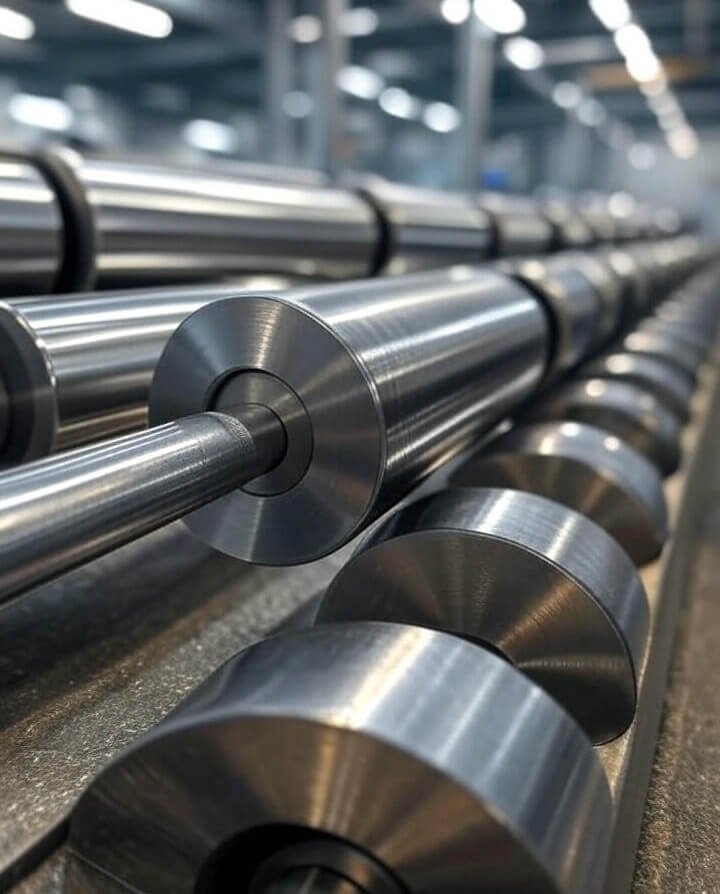
Industrial Applications Across Various Sectors
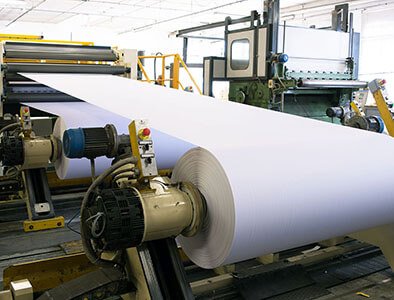
Paper Manufacturing
In the paper industry, curved rollers play a pivotal role throughout the entire production process. During pulp processing, these specialized rollers prevent the formation of wrinkles and creases that could compromise paper quality and cause costly production interruptions. In printing operations, curved rollers ensure consistent ink distribution and prevent web buckling, which is crucial for maintaining print registration and avoiding costly reprints. The rollers' ability to maintain uniform pressure distribution across the web width is particularly valuable in high-speed paper mills where even minor irregularities can cascade into significant quality issues.
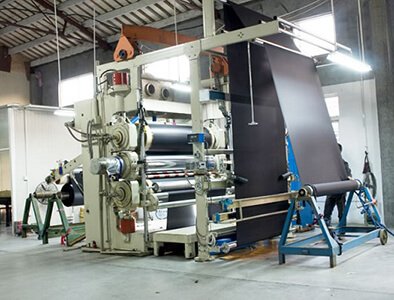
Textiles Industry
The textile sector relies heavily on curved rollers to maintain fabric integrity and appearance throughout various manufacturing stages. In weaving operations, these rollers ensure proper warp tension distribution, preventing uneven fabric construction that could lead to defects in the finished product. During dyeing processes, curved rollers facilitate uniform chemical penetration by maintaining consistent fabric tension and preventing the formation of dye streaks or color variations.
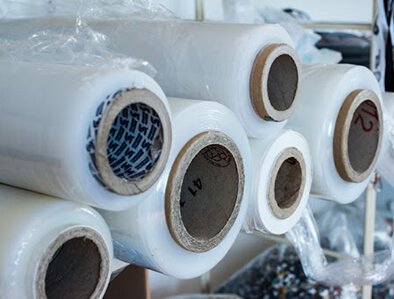
Film Production
In plastic and metal film extrusion processes, curved rollers are essential for maintaining consistent film thickness and surface quality. These rollers eliminate wrinkles and air entrapment that could create weak points or optical defects in the finished film. For thin-gauge applications, such as food packaging films or electronic component substrates, the precision offered by curved rollers is critical for meeting stringent thickness tolerances and surface smoothness requirements.
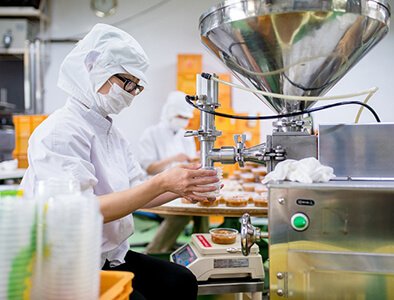
Packaging Industry
The packaging sector benefits significantly from curved roller technology in handling flexible packaging materials. These rollers support smooth processing of complex multi-substrate laminates, preventing delamination and ensuring strong bond formation between layers. In printing and coating operations for packaging materials, curved rollers maintain consistent substrate tension, enabling high-quality graphics reproduction and uniform coating application.
Supplier Selection and Investment Considerations
Manufacturing Excellence Assessment
Evaluate potential suppliers based on their precision manufacturing capabilities, particularly their expertise in crown profiling and surface finishing technologies. Suppliers equipped with advanced grinding and polishing equipment, along with comprehensive metrology systems, consistently deliver curved rollers with superior dimensional accuracy and surface quality. Production capacity analysis should encompass their ability to handle varying order volumes while maintaining consistent quality standards. Facilities with dedicated curved roller manufacturing lines and specialized tooling demonstrate commitment to this product category.
Technical Competency Evaluation
Assess suppliers' engineering depth in curved roller design principles, including crown calculation methodologies, deflection compensation techniques, and thermal expansion considerations. Suppliers with experienced application engineers who understand web handling dynamics can provide invaluable guidance in roller selection and system optimization. Their problem-solving capabilities should include finite element analysis tools and practical troubleshooting experience across diverse industrial applications.
Quality Assurance Standards
Priority should be given to suppliers maintaining relevant quality certifications such as ISO 9001 for general manufacturing excellence, with additional industry-specific certifications for specialized applications. For food packaging applications, BRC or SQF certifications may be essential. Aerospace applications might require AS9100 compliance. The supplier's quality control procedures should include crown profile verification, surface roughness measurement, and dynamic balancing protocols.
Design Flexibility and Innovation
Modern curved roller applications often demand specialized solutions beyond standard offerings. Evaluate suppliers' capabilities in computational modeling for crown optimization, including their ability to account for specific web materials, line speeds, and environmental conditions. Advanced suppliers utilize sophisticated simulation software to predict roller performance under various operating scenarios, enabling optimized designs before manufacturing.
Rapid Prototyping and Testing
Suppliers with in-house prototyping capabilities can accelerate product development cycles and reduce time-to-market for critical applications. Look for facilities equipped with additive manufacturing for concept validation and pilot-scale testing capabilities. The ability to perform web handling trials with prototype rollers provides valuable validation before full-scale production.
Material Science Expertise
Curved roller performance heavily depends on material selection and surface treatments. Suppliers with metallurgical expertise and coating capabilities can optimize roller compositions for specific applications. This includes knowledge of thermal treatments, chrome plating processes, ceramic coatings, and specialized surface textures that enhance web handling performance.
Our Manufacturing Prowess & R&D Capabilities
Production Scale & Qualifications
- Factory Area: Over 10,000 square meters dedicated to manufacturing high-precision slitters and Accessories
- Annual Capacity: 200+ high-quality slitting machines for various materials.
- Certifications: ISO 9001, CE, Multiple Patents for advanced slitting technology.
R&D and Innovation
- Dedicated R&D Team: 12+ experienced engineers focused on slitter machine innovation.
- Technical Collaborations: Partnering with leading universities and research institutes for cutting-edge slitting solutions.
- Innovation Focus: Continuous development of intelligent and automated slitting and rewinding machines for paper, film, and foil.
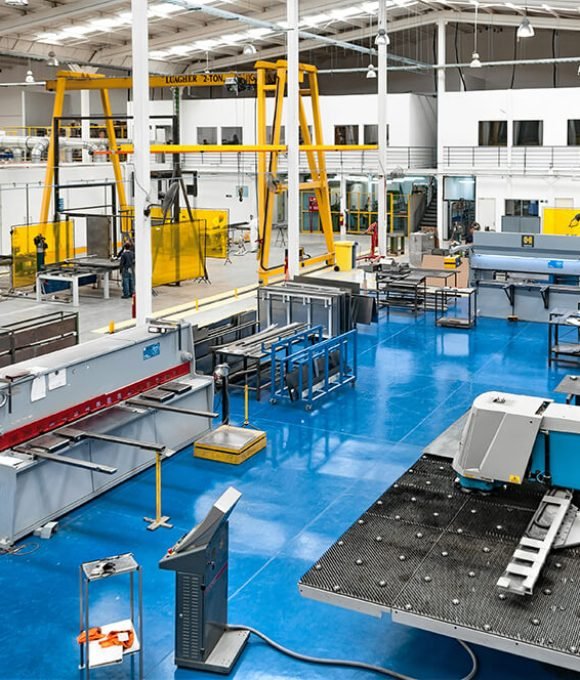
Quality Certifications
- ISO 9001:2015 Quality Management System
- CE Certification for European Market Compliance
- SGS Audited Supplier Status for all our slitting and rewinding machines.
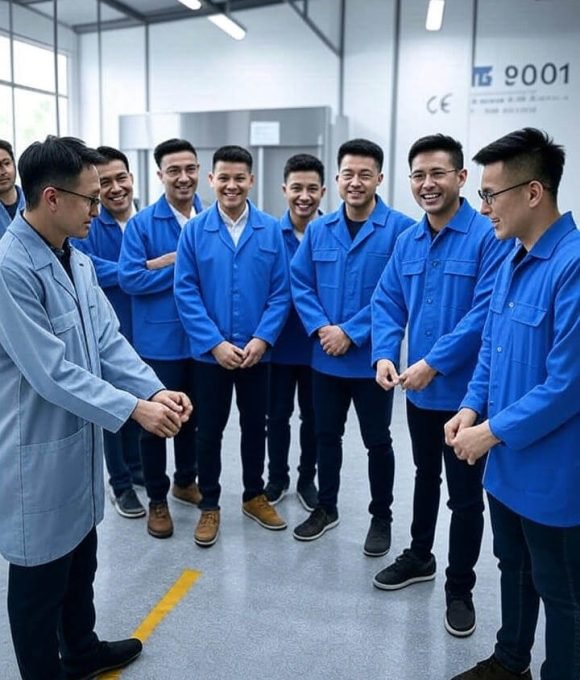
Unmatched After-Sales Service & Support
We have a growing network of overseas service points and authorized agents in Southeast Asia, Europe, and the Americas to ensure prompt local support for your slitting and rewinding machine.
Our Service Commitments
- 24/7 remote technical support and troubleshooting for your slitter.
- Scheduled preventive maintenance programs and on-site servicing for all slitting machines.
- Comprehensive operator training and detailed maintenance guides (e.g., slitter slider lubrication, film slitter knife care).