High-Efficiency Expander Rollers for Web Spreading
Featured Expander Rollers
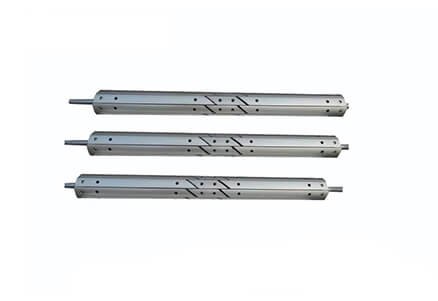
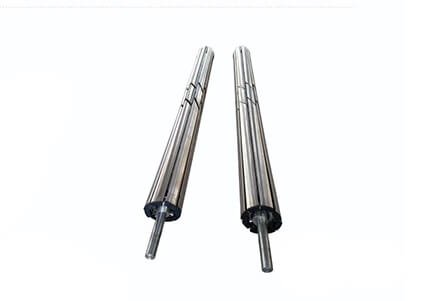
Expander Roller Size Specifications | |||
---|---|---|---|
Roller Surface Diameter (mm) | 130 | 150 | 180 |
Max Shaft End Diameter/Length L1 (mm) | 30 / 2000 | 35 / 3500 | 50 / 5000 |
Wrinkle-Free Web Processing with High-Performance Expander Rollers
Comprehensive Wrinkle Removal
Eliminates center, edge, and V-shaped wrinkles from various substrates before printing, coating, or lamination. Result: Delivers a smooth, uniform web for flawless downstream processing.
Web Width Control & Stabilization
Maintains consistent web width by evenly spreading material and preventing neck-in or shrinkage. Result: Minimizes variation and waste, ensuring dimensional accuracy.
Slack Edge & Baggy Center Correction
Resolves slack edges and loose center areas that disrupt tracking and processing consistency. Result: Improves web stability and machine runnability.
Separation of Slit Webs
Keeps slit lanes apart post-slitting to avoid re-adhesion or tangling before rewind. Result: Enables clean, independent rewinding and roll management.
Engineered for Precision: Inside Expander Roller Technology
1. Optimized Core Structure
2. Wrinkle-Resistant Surface Design
3. CNC-Finished for Smooth Web Contact
4. Material Synergy for Performance
5. Versatile Across Industries
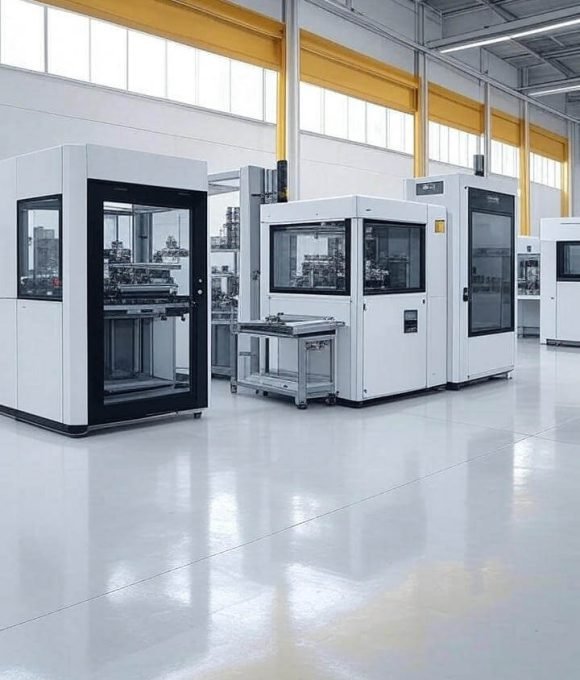
Get Our Free Samples
What Are Expander Rollers?
Expander rollers are specialized cylindrical components designed to eliminate wrinkles, control web tension, and improve material flatness in continuous web processing operations. Unlike conventional rollers that simply guide material, expander rollers actively work to spread and smooth the web through controlled mechanical action, ensuring optimal material presentation for downstream processes.
The fundamental principle behind expander rollers lies in their ability to apply controlled lateral forces to moving webs, effectively removing wrinkles, creases, and other surface irregularities. This is achieved through various mechanical designs including banana rollers, bow rollers, and pneumatic spreading systems that create precise curvature and tension distribution across the web width.
Expander rollers function by creating a controlled crown or bow that causes the web material to experience differential tension across its width. This differential tension naturally draws the material outward, eliminating wrinkles and creating a smooth, flat surface. The effectiveness of this process depends on proper roller design, material properties, and operating parameters.
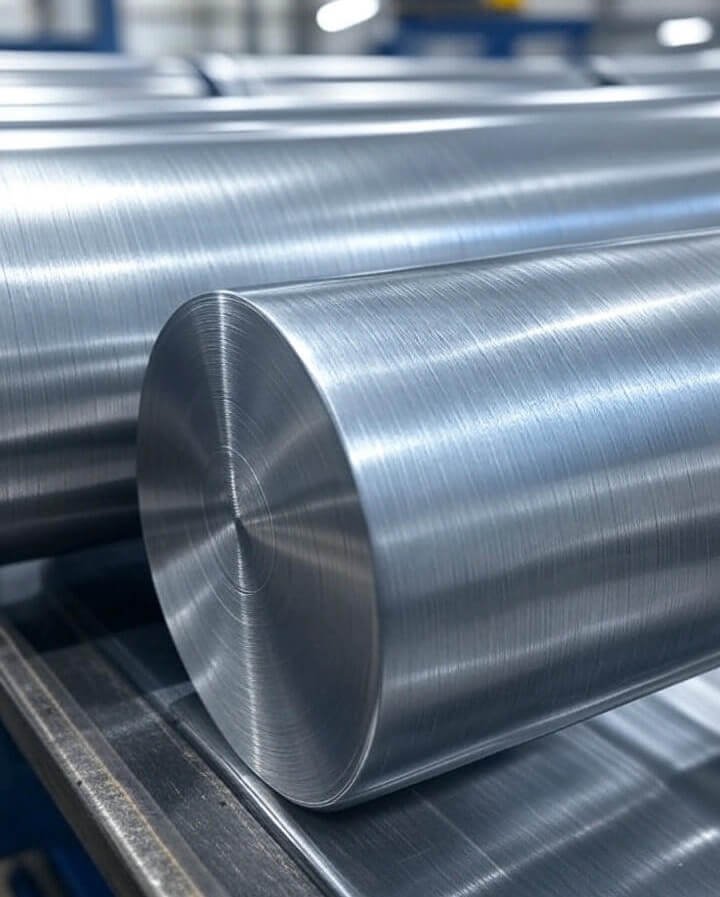
Industrial Applications Across Various Sectors
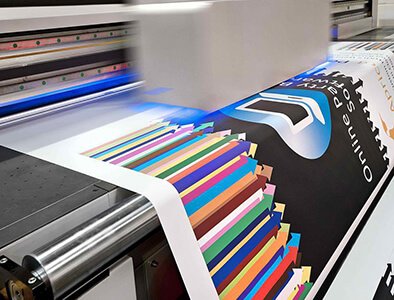
Printing Industry
Printing Industry extensively uses expander rollers to eliminate web wrinkles and ensure proper registration in multi-color printing processes. Web wrinkles can cause registration errors, ink smearing, and quality defects. Expander rollers positioned at strategic locations in the web path help maintain proper web flatness and tension distribution, resulting in higher print quality and reduced waste.
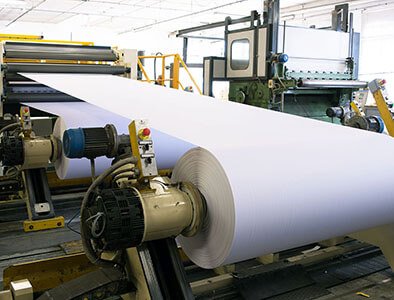
Paper and Converting Industry
Paper and Converting Industry employs expander rollers in coating, laminating, and slitting operations. These applications require precise web flatness to ensure uniform coating thickness, proper lamination bonding, and accurate slitting operations. Expander rollers help eliminate wrinkles that could cause coating defects or lamination voids.
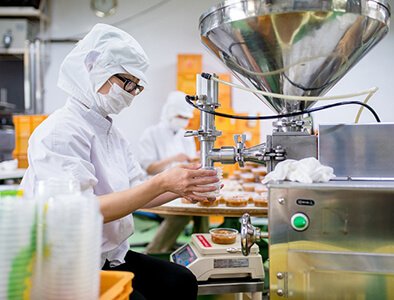
Packaging Industry
Packaging Industry utilizes expander rollers in flexible packaging production, particularly for films and foils. Wrinkles in packaging materials can affect barrier properties, appearance, and functionality. Expander rollers ensure smooth, flat materials that meet strict quality requirements for food packaging and other critical applications.
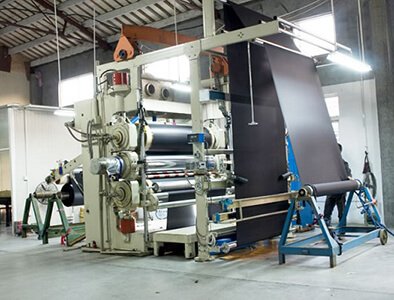
Textile Industry
Textile Industry uses expander rollers in fabric processing, dyeing, and finishing operations. Wrinkled fabrics can result in uneven dyeing, printing defects, and quality issues. Expander rollers help maintain proper fabric tension and flatness throughout the processing chain.
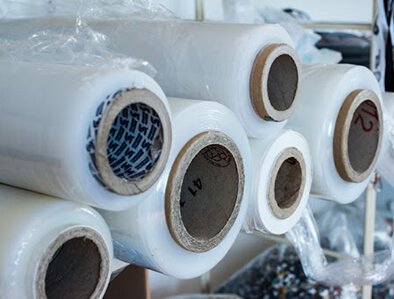
Film Manufacturing
Film Manufacturing relies on expander rollers to eliminate wrinkles and gauge variations in plastic film production. These applications require precise control over film flatness and thickness uniformity to meet demanding performance specifications.
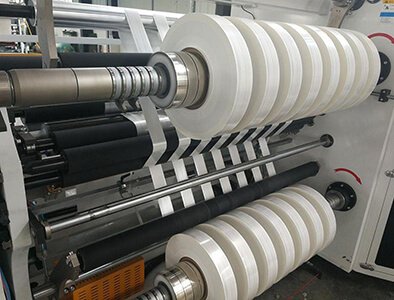
Metal Processing
Metal Processing industry employs expander rollers in coil processing, coating, and converting operations. Metal coils can develop wrinkles during unwinding and processing, affecting surface quality and coating uniformity. Expander rollers help maintain flat, smooth metal surfaces for subsequent processing steps.
Custom Expander Roller Parameters and Specifications
Dimensional Specifications
Dimensional Specifications must include roller diameter, face width, shaft dimensions, and mounting requirements. These dimensions must be coordinated with existing equipment and space constraints while optimizing performance for the specific application.
Performance Specifications
Performance Specifications should clearly define the required crown adjustment range, response time, operating speed range, and load capacity. These specifications help manufacturers select appropriate designs and components.
Material Requirements
Material Requirements may include specific coating materials, core materials, or component specifications based on the operating environment and web material characteristics. Chemical compatibility, temperature resistance, and wear characteristics must be considered.
Control System Requirements
Control System Requirements specify the level of automation, feedback systems, and integration requirements with existing production control systems. This may include analog or digital control interfaces, remote monitoring capabilities, and safety interlocks.
Quality Standards
Quality Standards may require compliance with specific industry standards, certifications, or testing requirements. This is particularly important for applications in regulated industries such as food packaging or pharmaceuticals.
Environmental Considerations
Environmental Considerations include operating temperature range, humidity tolerance, chemical exposure, and cleanability requirements. These factors influence material selection and system design.
Our Manufacturing Prowess & R&D Capabilities
Production Scale & Qualifications
- Factory Area: Over 10,000 square meters dedicated to manufacturing high-precision slitters and Accessories
- Annual Capacity: 200+ high-quality slitting machines for various materials.
- Certifications: ISO 9001, CE, Multiple Patents for advanced slitting technology.
R&D and Innovation
- Dedicated R&D Team: 12+ experienced engineers focused on slitter machine innovation.
- Technical Collaborations: Partnering with leading universities and research institutes for cutting-edge slitting solutions.
- Innovation Focus: Continuous development of intelligent and automated slitting and rewinding machines for paper, film, and foil.
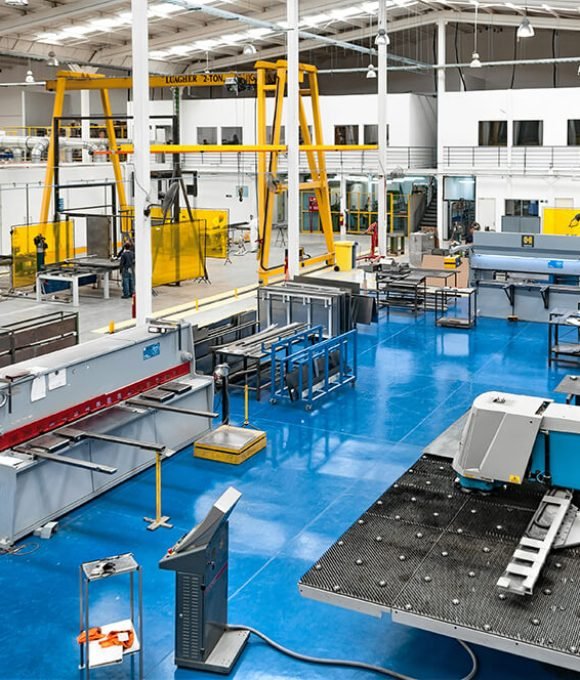
Quality Certifications
- ISO 9001:2015 Quality Management System
- CE Certification for European Market Compliance
- SGS Audited Supplier Status for all our slitting and rewinding machines.
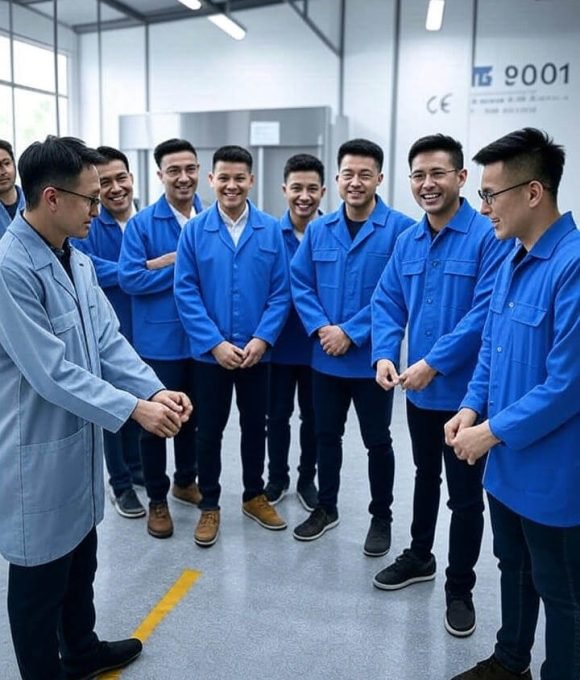
Unmatched After-Sales Service & Support
We have a growing network of overseas service points and authorized agents in Southeast Asia, Europe, and the Americas to ensure prompt local support for your slitting and rewinding machine.
Our Service Commitments
- 24/7 remote technical support and troubleshooting for your slitter.
- Scheduled preventive maintenance programs and on-site servicing for all slitting machines.
- Comprehensive operator training and detailed maintenance guides (e.g., slitter slider lubrication, film slitter knife care).