Premium Industrial Rubber Rollers - Engineered for Excellence
- Nitrile Rubber Rollers - Superior chemical resistance and durability for demanding industrial environments
- EPDM Rubber Rollers - Outstanding weather resistance and thermal stability for outdoor and high-temperature applications
- Silicone Rollers - Exceptional release properties and temperature tolerance for specialized coating processes
Featured Rubber Rollers
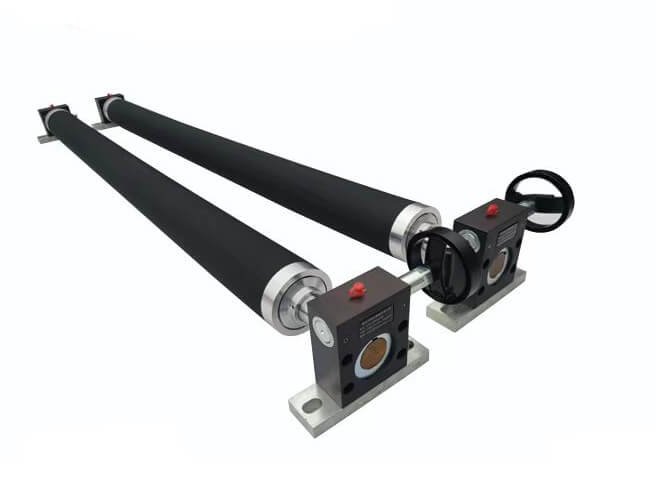
Product Specifications – Rubber Rollers | |||||||||
---|---|---|---|---|---|---|---|---|---|
Model | R80 | R100 | R125 | R150 | R180 | R200 | R240 | R280 | R330 |
Roller Surface Diameter (mm) | 80 | 100 | 125 | 150 | 180 | 200 | 240 | 280 | 330 |
Maximum Total Length (mm) | 1000 | 2000 | 3000 | 4000 | 4500 | 5500 | 6000 | 7500 | 9500–12000 |
High-Performance Rubber Rollers for Industrial Web Processing
Nip & Pulling Applications
Used in tandem to create controlled pressure zones, these rollers grip and pull materials through converting lines. Nitrile rubber rollers are commonly chosen for their oil resistance and general-purpose reliability.
Coating & Printing Support
Rubber rollers used to evenly transfer inks, adhesives, or coatings onto films, foils, or paper webs. Designed for excellent surface uniformity and chemical compatibility.
Laminating Pressure Rollers
Employed to bond multilayer webs in lamination systems. Silicone or EPDM rollers offer excellent heat resistance and compressibility for void-free adhesion. Benefit: Strong, uniform lamination across paper, film, or foil substrates.
Drive & Idler Roller Functions
Drive rollers apply power to web systems, while idlers guide and support the web through the line. Rubber coatings provide extra grip or protect sensitive materials.
Engineered for Performance: Inside Industrial Rubber Roller Technology
1. Custom Core Construction
2. Precision Rubber Compounding & Bonding
3. Optimized Surface Finishing
4. Application-Tailored Material Pairing
5. Built for Versatile Web Processing
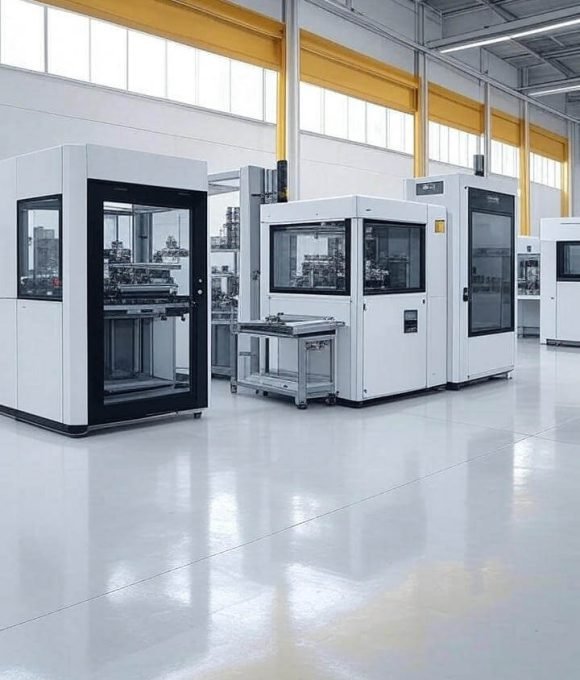
Get Our Free Samples
What Are Rubber Rollers?
Rubber rollers are cylindrical components consisting of a core material (typically steel, aluminum, or composite) covered with a specially formulated rubber compound. The rubber covering provides specific surface properties including grip, flexibility, chemical resistance, and wear characteristics that are essential for effective material handling and processing.
The fundamental advantage of rubber rollers lies in their ability to conform to irregular surfaces while maintaining consistent contact pressure. This conformability, combined with controlled hardness and surface texture, enables rubber rollers to perform functions that rigid metal rollers simply cannot accomplish effectively.
Rubber rollers operate on principles of friction control, pressure distribution, and material deformation. The rubber compound can be engineered to provide specific coefficients of friction, ranging from high-grip applications requiring maximum traction to low-friction applications where material slippage must be minimized. The viscoelastic properties of rubber allow these rollers to absorb vibrations, distribute loads evenly, and adapt to varying operating conditions.
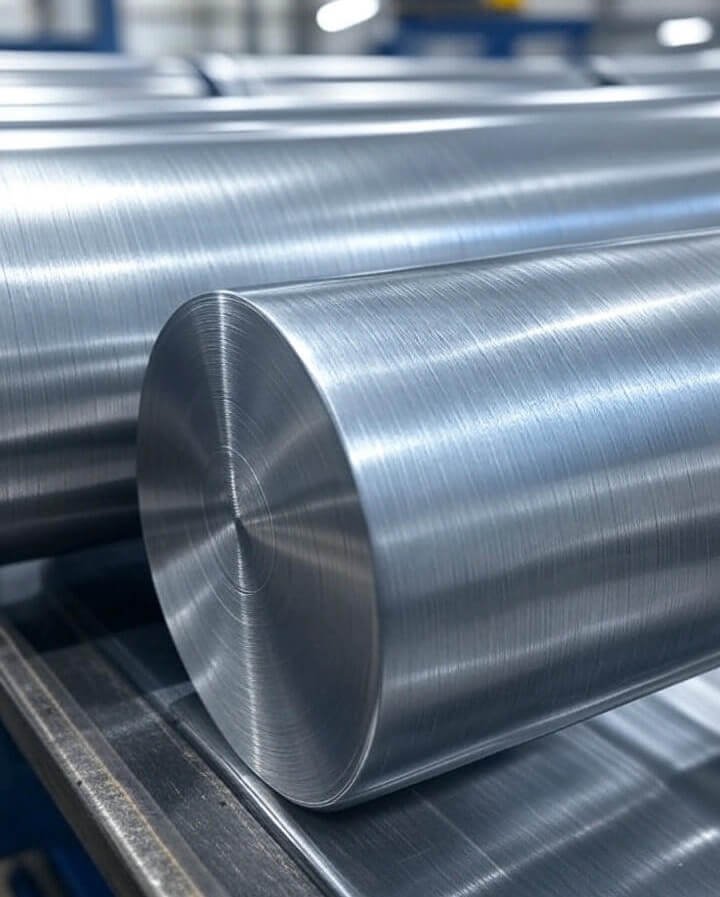
Industrial Applications Across Various Sectors
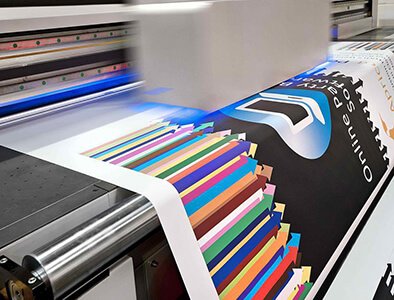
Printing and Graphics Industry
Printing and Graphics Industry extensively utilizes rubber rollers in offset printing, flexographic printing, and digital printing applications. The rubber surface provides controlled ink transfer, consistent pressure distribution, and excellent print quality. Form rollers, ink rollers, and impression rollers are essential components that directly impact print quality and production efficiency.
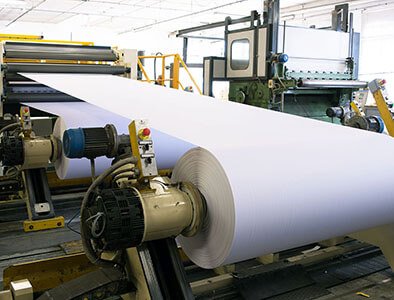
Paper and Pulp Industry
Paper and Pulp Industry employs rubber rollers throughout the papermaking process, from pulp preparation to final product finishing. Calender rollers provide surface smoothness and thickness control. Coating rollers apply precise amounts of coating materials. Transport rollers move paper through various processing stages while maintaining proper tension and alignment.
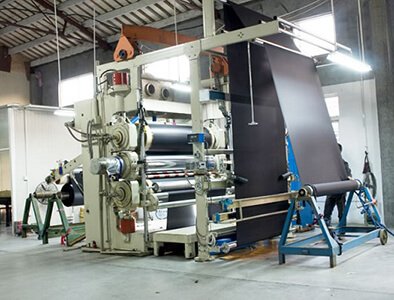
Textile Industry
Textile Industry relies on rubber rollers for fabric processing, dyeing, and finishing operations. The rubber surface provides gentle material handling while maintaining proper tension and alignment. Squeeze rollers remove excess water or chemicals, while guide rollers direct fabric through complex processing paths.
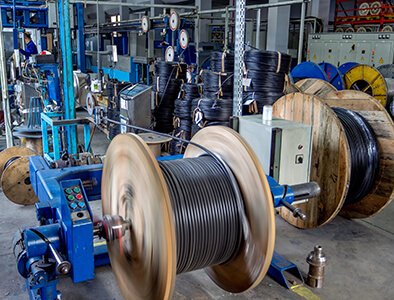
Steel and Metal Processing
Steel and Metal Processing uses rubber rollers for material handling, surface treatment, and finishing operations. The rubber surface prevents scratching and marring of finished metal surfaces while providing controlled pressure for various processing operations.
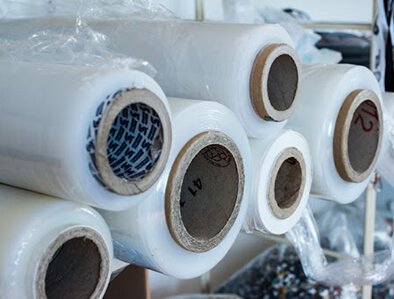
Plastic Film Industry
Plastic Film Industry depends on rubber rollers for film production, laminating, and converting processes. The rubber surface provides controlled friction and pressure distribution essential for producing high-quality plastic films with consistent thickness and surface properties.
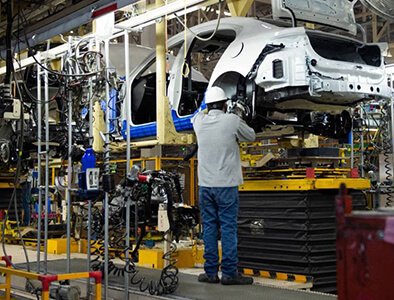
Agricultural Equipment
Agricultural Equipment incorporates rubber rollers in various applications including grain processing, crop handling, and soil preparation. The rubber surface provides gentle material handling while maintaining durability in harsh outdoor environments.
Custom Rubber Roller Parameters and Specifications
Core Material Selection
Core Material Selection depends on application requirements including strength, weight, thermal characteristics, and cost considerations. Steel cores provide maximum strength and durability. Aluminum cores offer lighter weight and better heat dissipation. Composite cores may provide specific characteristics for specialized applications.
Rubber Compound Formulation
Rubber Compound Formulation must be tailored to specific performance requirements. This includes selecting base polymers, fillers, curing systems, and additives to achieve desired properties such as hardness, chemical resistance, temperature stability, and wear characteristics.
Geometric Specifications
Geometric Specifications include roller diameter, length, core configuration, and any special features such as grooves, patterns, or mounting provisions. These specifications must consider manufacturing capabilities and application requirements.
Surface Finish Requirements
Surface Finish Requirements may include specific textures, patterns, or smoothness levels depending on the application. Custom surface treatments can be applied to achieve specific functional characteristics.
Quality Standards
Quality Standards should specify testing requirements, certification needs, and performance criteria. This may include durometer testing, tensile strength verification, chemical resistance validation, or other application-specific tests.
Performance Validation
Performance Validation requirements should define acceptance criteria, testing methods, and documentation needs to ensure the custom roller meets all specified requirements.
Our Manufacturing Prowess & R&D Capabilities
Production Scale & Qualifications
- Factory Area: Over 10,000 square meters dedicated to manufacturing high-precision slitters and Accessories
- Annual Capacity: 200+ high-quality slitting machines for various materials.
- Certifications: ISO 9001, CE, Multiple Patents for advanced slitting technology.
R&D and Innovation
- Dedicated R&D Team: 12+ experienced engineers focused on slitter machine innovation.
- Technical Collaborations: Partnering with leading universities and research institutes for cutting-edge slitting solutions.
- Innovation Focus: Continuous development of intelligent and automated slitting and rewinding machines for paper, film, and foil.
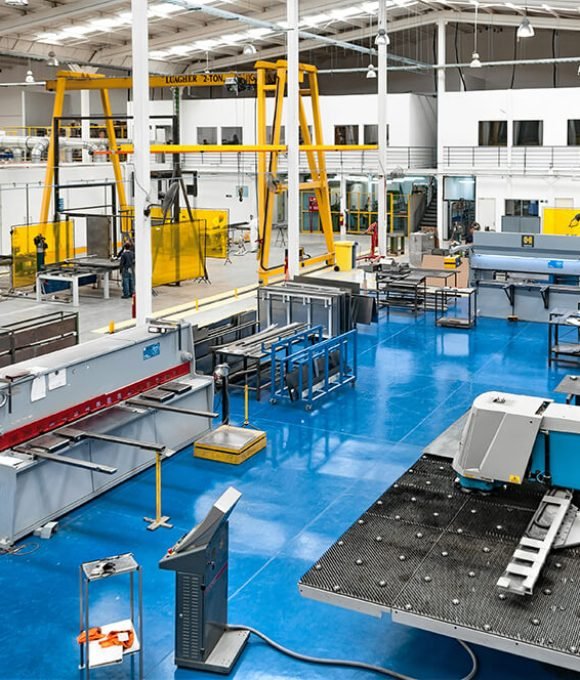
Quality Certifications
- ISO 9001:2015 Quality Management System
- CE Certification for European Market Compliance
- SGS Audited Supplier Status for all our slitting and rewinding machines.
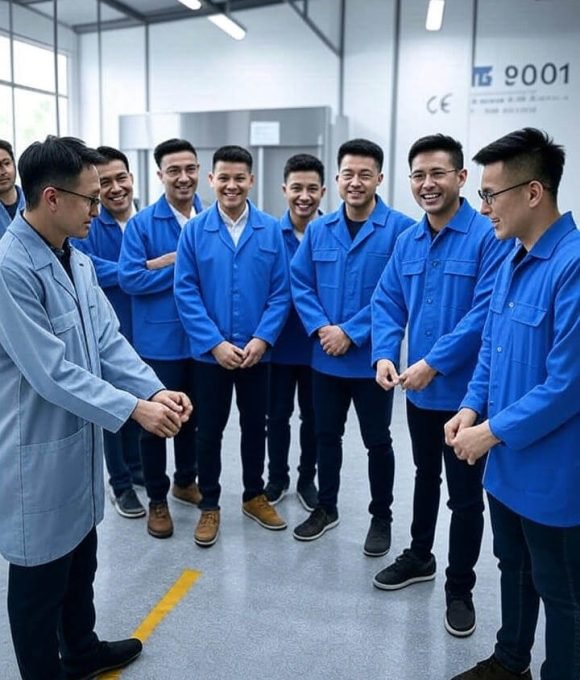
Unmatched After-Sales Service & Support
We have a growing network of overseas service points and authorized agents in Southeast Asia, Europe, and the Americas to ensure prompt local support for your slitting and rewinding machine.
Our Service Commitments
- 24/7 remote technical support and troubleshooting for your slitter.
- Scheduled preventive maintenance programs and on-site servicing for all slitting machines.
- Comprehensive operator training and detailed maintenance guides (e.g., slitter slider lubrication, film slitter knife care).