Silicone Spreader Rollers for Enhanced Web Handling
Featured Silicone Spreader Rollers
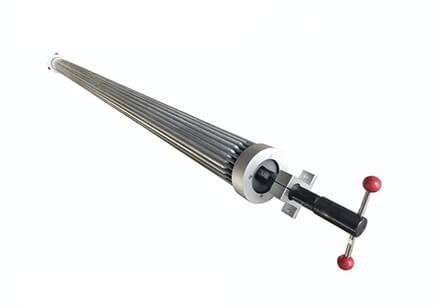
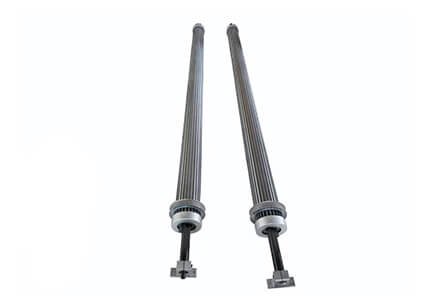
Product Specifications – Silicone Spreader Rollers | |
---|---|
Shaft Surface Diameter | 130 mm |
Core Shaft Diameter | 40 mm |
Effective Roller Length | 600–4000 mm |
Line Speed | <300 m/min |
Substrate Wrap Angle | 90°–180° |
Spreading Width | 0–30 mm |
Core Shaft Condition | Fixed, Non-Rotating |
Versatile Solutions for Web Control and Wrinkle Elimination
Wrinkle Elimination for Converting Lines
Effectively removes wrinkles and creases from films, papers, foils, and nonwovens ahead of slitting, coating, or laminating. Ensures smooth web flow and reduces downstream defects.
Web Guiding and Alignment Support
Provides additional web guidance by gently correcting minor alignment deviations. Ideal for maintaining edge stability without damaging the substrate.
Tension Leveling Across the Web
Distributes tension uniformly across the web width—especially helpful for materials with edge slack or center tightness—to improve roll quality and process stability.
Delicate Substrate Handling
Silicone’s soft, non-marking surface makes it the perfect choice for fragile materials. Offers excellent performance in narrow web unwinding or applications requiring reduced surface pressure.
Engineered for Web Perfection: Inside Silicone Spreader Roller Design
1. Precision Roller Core Construction
2. High-Performance Silicone Coating
3. Fine Surface Finishing for Smooth Web Contact
4. Balanced Material Integration
5. Optimized for Wrinkle-Free Converting
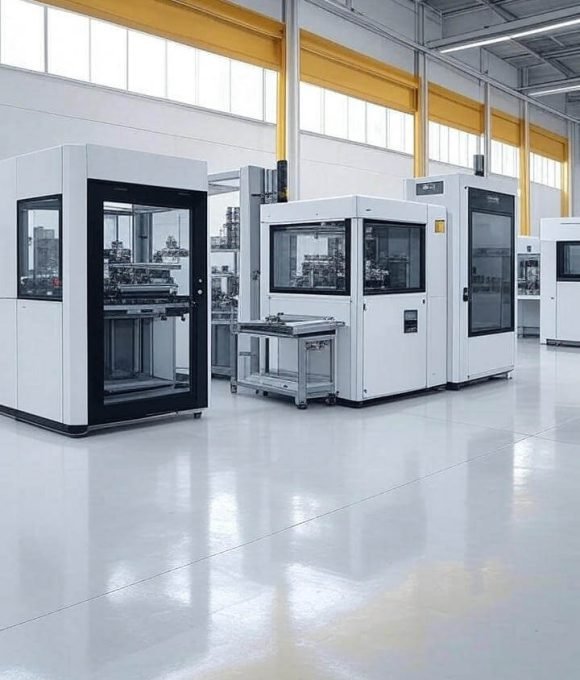
Get Free Samples of Our Silicone Spreader Rollers
What Are Silicone Spreader Rollers?
Silicone spreader rollers play a pivotal role in modern manufacturing processes, delivering uniform material distribution, precise coating control, and exceptional release properties. As production demands evolve—whether in printing, laminating, or adhesive applications—engineers and procurement teams must understand how silicone spreader rollers differ from traditional rollers and how to choose the right roller for maximum performance and economy.
Silicone spreader rollers consist of a metal or polymer core uniformly coated with a silicone elastomer. This combination leverages the structural strength of the core and the unique elasticity, chemical resistance, and non-stick surface of silicone. When material passes beneath or across the roller, the silicone layer ensures even spreading, prevents buildup, and maintains consistent thickness across sheets, films, or webs.
Different Types and Specifications of Silicone Spreader Rollers
Standard Silicone Rollers
A basic silicone elastomer coating (thickness 0.5–2.0 mm) on a steel or aluminum core. Ideal for general-purpose coating and spreading applications.
High-Durometer Silicone Rollers
Featuring shore hardness up to Shore A 90 for high-pressure or high-speed operations where minimal deformation is essential.
Low-Durometer Silicone Rollers
Shore A 20–50 for delicate film spreading or applications requiring conformable, soft contact surfaces.
Antimicrobial Silicone Rollers
Infused with silver or other biocidal agents, these rollers prevent microbial growth and are suited for medical, pharmaceutical, or food-contact lines.
FDA- and USDA-Compliant Rollers
Made from virgin, platinum-cured silicone compounds free of plasticizers and fillers, meeting food- and drug-contact regulations.
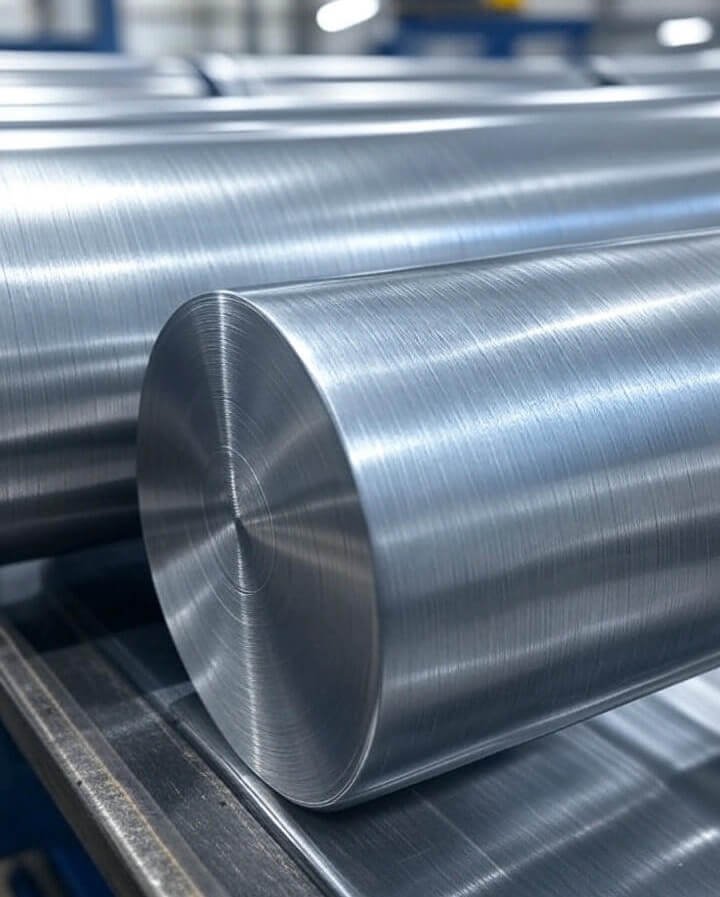
Industrial Applications Across Various Sectors
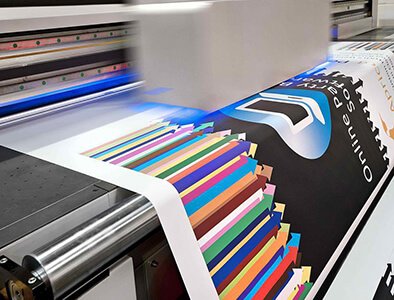
Printing & Coating
Ensure uniform ink, varnish, or specialty coatings in offset, flexo, and digital presses. The compliant silicone surface maintains constant nip pressure for consistent dot gain and film weight, reducing print defects and waste.
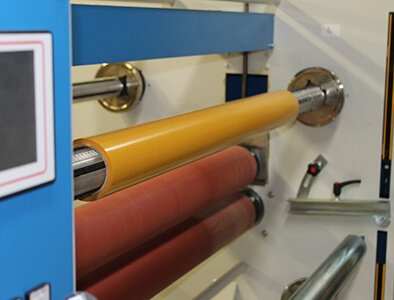
Adhesive Lamination
Spread hot-melt, pressure-sensitive, or UV-curable adhesives evenly across substrates. Silicone rollers prevent stringing and buildup, improving bond quality in packaging, label, and graphic lamination lines.
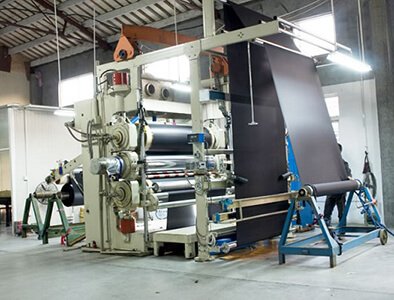
Textile Finishing
Apply softeners, flame retardants, and other functional finishes to fabrics without marking or snagging. Silicone’s smooth yet slightly conformable surface handles delicate weaves and nonwoven webs with minimal tension variations.
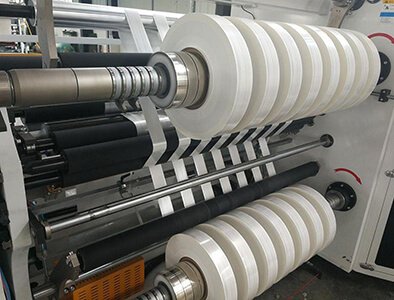
Foil & Film Processing
Control coating thickness and ensure clean release in metallization, barrier coatings, and extrusion lamination. Silicone spreader rollers resist sticking to tacky polymers and maintain precise gauge control in high-speed lines.
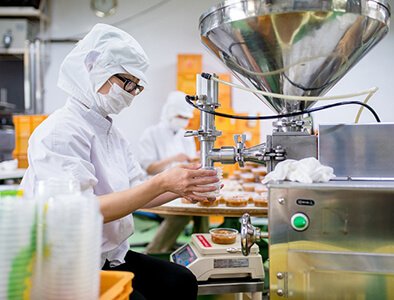
Pharmaceutical & Food Packaging
Deliver hygienic, non-contaminating spread of sealants, lubricants, or barrier coatings on blister packs, sachets, and wrapping films. FDA- and USDA-compliant silicone formulations meet stringent purity and clean-in-place requirements.
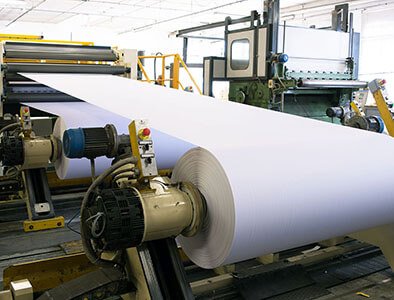
Composite & Advanced Materials
Distribute resin systems, adhesives, or release agents in composite lay-up, panel lamination, and specialty film manufacturing. The chemical resistance and temperature stability of silicone ensure reliable performance under demanding processing conditions.
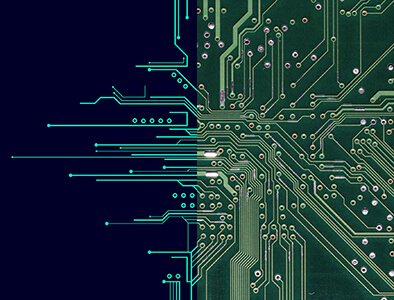
Automotive & Electronics
Spread conformal coatings, adhesives, and thermal interface materials for circuit boards, displays, and component assembly. Silicone rollers provide uniform film thickness and clean release, critical for high-precision applications.
Custom Silicone Spreader Roller Specifications
Dimensional Specifications
– Include all critical dimensions: roller diameter, overall length, bore and shaft diameters, keyways or flats, and any special grooves or shoulders. – Specify tolerances and concentricity/straightness requirements to guarantee proper nip alignment and smooth web tracking. – Account for end-cap or bearing housing interfaces and any clearance needed for mounting brackets or sealing.
Core Material Selection
– Steel Cores (carbon or alloy): Ideal for high-load, high-speed lines; offer maximum rigidity and fatigue resistance. – Stainless Steel Cores: Provide superior corrosion resistance in hygienic or chemical‑exposed environments. – Aluminum Cores: Lightweight option for reduced inertia, beneficial in rapid‑start/stop systems or low‑tension webs. – Engineered Polymer Cores: Available for ultra‑lightweight or electrically insulating rollers; suitable for niche applications.
Silicone Coating Compound Specification
– Base Elastomer: Platinum‑cured silicone for highest purity and tear resistance; peroxide‑cured for cost‑sensitive uses. – Durometer: Specify Shore A hardness (20–90) to balance compliance and load‑bearing capacity. – Fillers/Additives: Include silica for enhanced wear resistance, ceramic for thermal stability, or antimicrobial agents for sanitary lines. – Regulatory Compliance: Indicate any FDA, USDA, USP Class VI, or ISO 10993 certifications required for food, pharmaceutical, or medical applications.
Surface Texture & Finish Requirements
– Surface Roughness (Ra): Define target Ra (e.g., 0.4–0.8 µm for release-critical coatings; 1.0–2.0 µm for grip-enhancing textures). – Finish Methods: Electropolishing or buffing for ultra‑smooth release surfaces; laser or knurled texturing for controlled traction. – Visual Inspection: Specify acceptable appearance criteria, including absence of pits, inclusions, or coating voids.
Performance Requirements
– Operating Temperatures: Detail continuous and peak temperatures (e.g., –60 °C to +200 °C), including any thermal cycling profiles. – Line Speed & Tension: State maximum web speeds and nip pressures to ensure coating integrity under dynamic loads. – Chemical Exposure: List process fluids, solvents, and cleaning agents to confirm compound compatibility. – Service Life Expectations: Provide target runtime or coating wear limits (e.g., 10,000 m of web throughput).
Quality and Testing
– Dimensional Verification: Dimensional report with certified measurements for diameter, length, and concentricity. – Hardness Testing: Shore A durometer readings at multiple locations. – Bond/Adhesion Testing: Peel or shear tests to verify silicone-to-core adhesion strength. – Surface Roughness Measurement: Profilometer data confirming specified Ra. – Material Certifications: Mill or batch certificates for core alloy and silicone compound traceability.
Special Features & Add‑Ons
– Internal Cooling or Heating Channels: For precise temperature control in thermal‑sensitive coatings. – Integrated Instrumentation: Embedded thermocouples, pressure sensors, or RFID tags for real‑time monitoring. – Custom Mounting Hardware: Flanges, bearings, or quick‑change end caps tailored to your equipment. – Multi‑Layer or Duplex Coatings: Dual‑durometer or gradient coatings for combined grip and release properties.
Our Manufacturing Prowess & R&D Capabilities
Production Scale & Qualifications
- Factory Area: Over 10,000 square meters dedicated to manufacturing high-precision slitters and Accessories
- Annual Capacity: 200+ high-quality slitting machines for various materials.
- Certifications: ISO 9001, CE, Multiple Patents for advanced slitting technology.
R&D and Innovation
- Dedicated R&D Team: 12+ experienced engineers focused on slitter machine innovation.
- Technical Collaborations: Partnering with leading universities and research institutes for cutting-edge slitting solutions.
- Innovation Focus: Continuous development of intelligent and automated slitting and rewinding machines for paper, film, and foil.
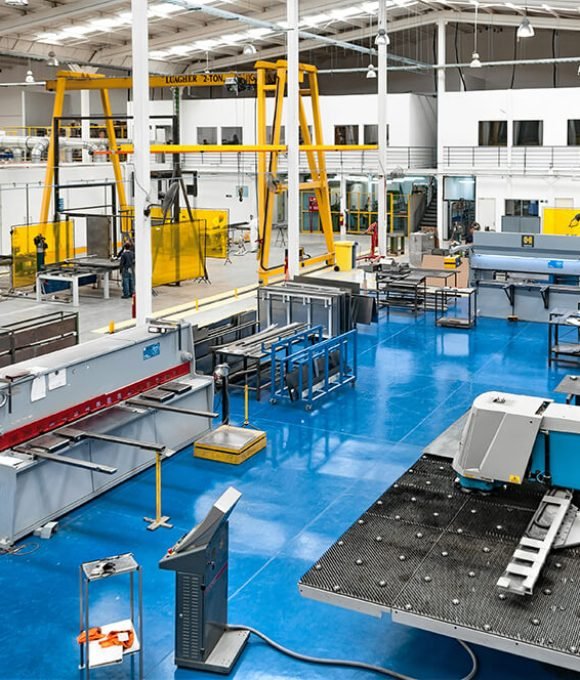
Quality Certifications
- ISO 9001:2015 Quality Management System
- CE Certification for European Market Compliance
- SGS Audited Supplier Status for all our slitting and rewinding machines.
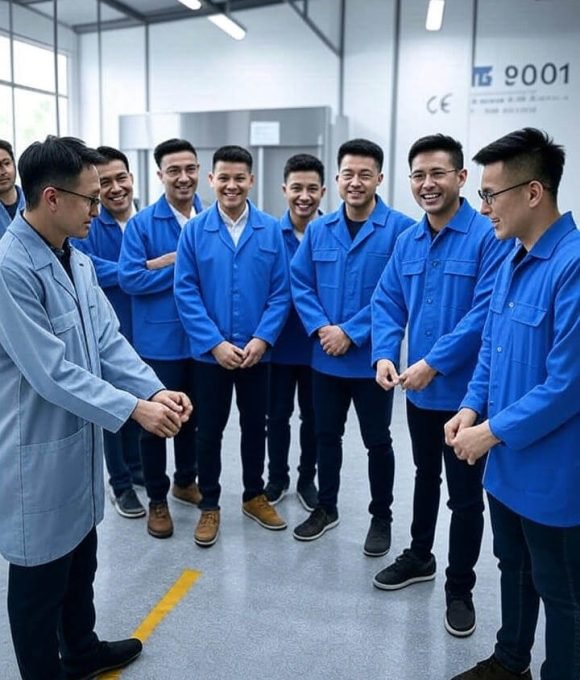
Unmatched After-Sales Service & Support
We have a growing network of overseas service points and authorized agents in Southeast Asia, Europe, and the Americas to ensure prompt local support for your slitting and rewinding machine.
Our Service Commitments
- 24/7 remote technical support and troubleshooting for your slitter.
- Scheduled preventive maintenance programs and on-site servicing for all slitting machines.
- Comprehensive operator training and detailed maintenance guides (e.g., slitter slider lubrication, film slitter knife care).