High-Precision Slitting for Aluminium & Copper Foils
Featured Metal Foil Slitter Rewinder Machines
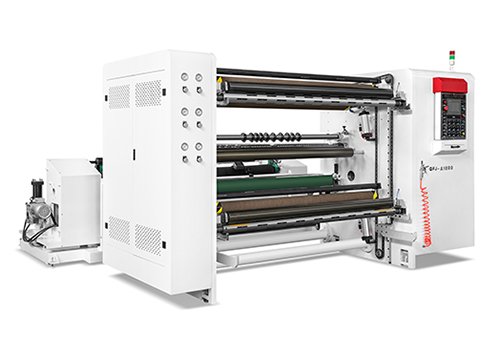
QFJ-A400 Horizontal High Speed Slitting Machine
- Key Specifications:
- Max Speed: 400m/min
- Min. Slitting Width: 30mm
- Unwinding Diameter 1200mm(Customizable)
- Rewinding Diameter 1000mm(Customizable)
- Key Specifications:
- Automatic unloading by chain
- Independent shaft free feeding
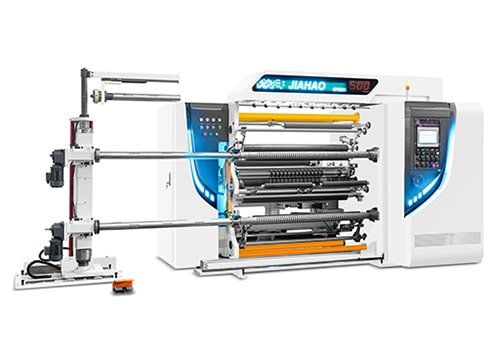
QFJ-A500 Horizontal High Speed Slitting Machine
- Key Specifications:
- Max Speed: 500m/min
- Min. Slitting Width: 20mm
- Unwinding Diameter 800mm(Customizable)
- Rewinding Diameter 600mm(Customizable)
- Key Specifications:
- Small Footprint of connected structures
- 4 Sets Servo Motor Controll
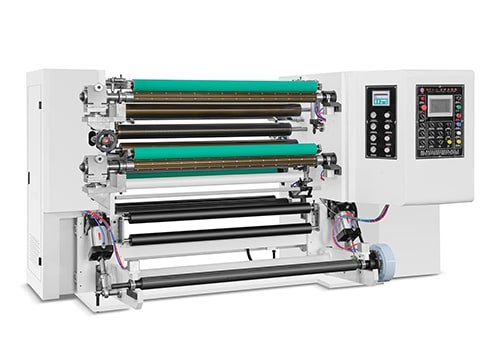
QFJ-B200 Vertical Slitting Machine
- Key Specifications:
- Max Speed: 200m/min
- Min. Slitting Width: 20mm
- Unwinding Diameter 700mm(Customizable)
- Rewinding Diameter 400mm(Customizable)
- Key Specifications:
- Small Footprint of connected structures
- 4 Sets Servo Motor Controll
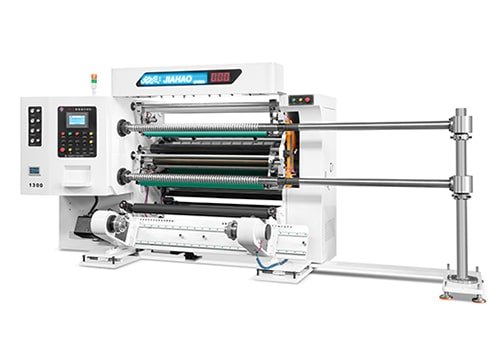
QFJ-B500 Vertical High Speed Slitting Machine
- Key Specifications:
- Max Speed: 500m/min
- Min. Slitting Width: 30mm
- Unwinding Diameter 750mm(Customizable)
- Rewinding Diameter 450mm(Customizable)
- Key Specifications:
- Automatic unloading by chain
- Independent shaft free feeding
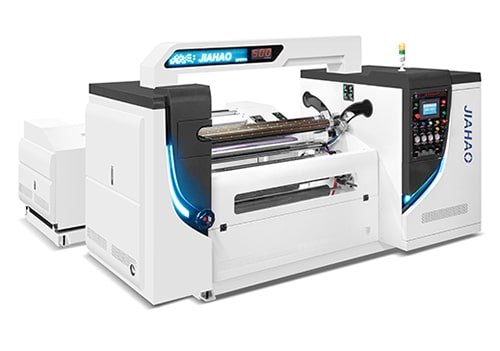
QFJ-C500 Surface Winding High Speed Slitting Machine
- Key Specifications:
- Max Speed: 500m/min
- Min. Slitting Width: 20mm
- Unwinding Diameter 1000mm(Customizable)
- Rewinding Diameter 600mm(Customizable)
- Key Specifications:
- Small Footprint of connected structures
- 4 Sets Servo Motor Controll
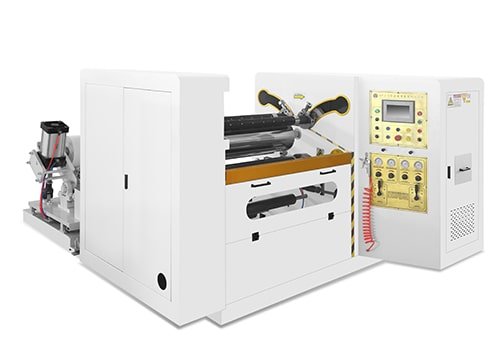
QFJ-C200 Series Surface Winding Slitting Machine
- Key Specifications:
- Max Speed: 200m/min
- Min. Slitting Width: 10mm
- Unwinding Diameter 1000mm(Customizable)
- Rewinding Diameter 600mm(Customizable)
- Key Specifications:
- Small Footprint of connected structures
- 4 Sets Servo Motor Controll
Specialized Foil Slitting Applications
Aluminium Foil for Packaging & Household Use
High-precision slitting of aluminium foil rolls for food packaging, household wraps, and industrial liners. Ensures clean edges, tight winding, and minimal surface contamination.
Copper Foil for Electronics & PCB
Slitting systems tailored for copper foils used in circuit boards and flexible electronics. Provides burr-free edges and tight width tolerance to support stable conductivity.
Battery Electrode Foils (Anode & Cathode)
Clean, burr-free slitting for copper and aluminium battery foils. Ensures edge stability for safe, high-performance lithium-ion cells.
Capacitor & Transformer Foils
Reliable slitting for silver, aluminium, and copper foils used in capacitors and transformers. Gentle handling prevents material deformation and edge damage.
Specialty & Ultra-Thin Metal Foils
Supports gold, nickel, and laminated foils. Custom machines available for exotic applications, including refurbished aluminium foil rewinders on request.
Precision Slitting for Thin & Delicate Foils
From Roll to Finish: Inside the Film Slitting Workflow
1. Robust Shaftless Unwinding
2. Sensitive Tension Management
3. Precision Shear Slitting
4. Safe Trim Removal
5. Scratch-Free Rewinding
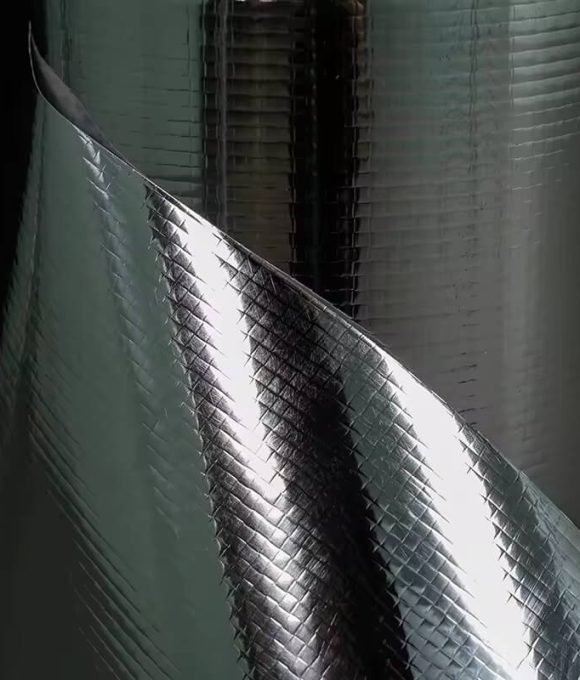
Turning Your Metal Foil Slitting Challenges into Smart Solutions
Prevent Aluminium Foil Breakage and Surface Damage
Dual-taper cone coreless clamping, electro-hydraulic guiding, and non-marking rollers ensure smooth feeding, stable tension, and reduced risk of foil breakage, deformation, or scratches.
Eliminate Burrs and Maintain Edge Quality on Copper Foil
Ultra-precision shear blades and a rigid frame deliver burr-free slitting with edge deviations under 5µm—ideal for downstream processes like PCB etching and lamination.
Maintain Winding Stability for Ultra-Thin Foils
Closed-loop tension control with contact or differential rewinding ensures consistent roll density, accurate edge alignment, and no telescoping—even on fragile or ultra-thin foils.
Reduce Trim Waste and Improve Operator Safety
Integrated trim suction systems efficiently remove sharp metal edges and foil scraps during slitting—keeping the work area clean and reducing the risk of operator injury or product contamination.
Adapt Easily to Different Foil Widths and Core Sizes
Modular machine design with adjustable slit positioning, interchangeable shafts, and automated tension presets allows fast setup for various roll widths, foil types, and core dimensions.
Customized Foil Slitting Solutions
Every foil processing line has its own challenges — that’s why we offer fully customizable slitting systems engineered to match your specific material, tension, and production needs.
Whether you’re slitting wide rolls of aluminium foil, narrow copper strips for electronics, or delicate battery-grade materials, our engineers will build a tailored solution for consistent performance and high edge quality.
What We Customize:
Machine Configuration
Custom-built frame structures, unwind/rewind setups, and web paths optimized for thin foil handling and factory layout.
Slitting System
Precision shear or rotary knife assemblies selected based on foil thickness, material hardness, and edge quality standards.
Rewinding Options
Options include contact rewind, differential shaft systems, and coreless rewinding—designed to protect delicate foil surfaces and maintain roll consistency.
Web Width & Roll Diameter
Equipment available for foil widths from 600 mm to 2500 mm and jumbo rolls up to 1500 mm OD.
Accessories & Spare Parts
Foil-grade blades, dust-free trim suction systems, anti-scratch rollers, tension load cells, and more for safe and reliable operation.
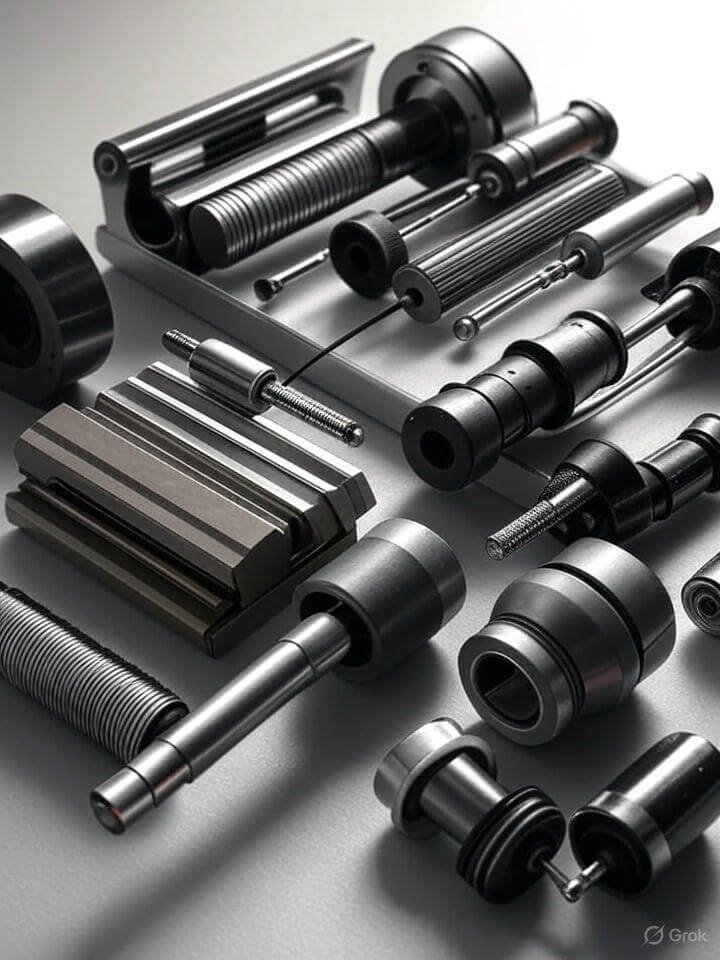
Our Manufacturing Prowess & R&D Capabilities
Production Scale & Qualifications
- Factory Area: Over 10,000 square meters dedicated to manufacturing high-precision slitters.
- Annual Capacity: 200+ high-quality slitting machines for various materials.
- Certifications: ISO 9001, CE, Multiple Patents for advanced slitting technology.
R&D and Innovation
- Dedicated R&D Team: 12+ experienced engineers focused on slitter machine innovation.
- Technical Collaborations: Partnering with leading universities and research institutes for cutting-edge slitting solutions.
- Innovation Focus: Continuous development of intelligent and automated slitting and rewinding machines for paper, film, and foil.
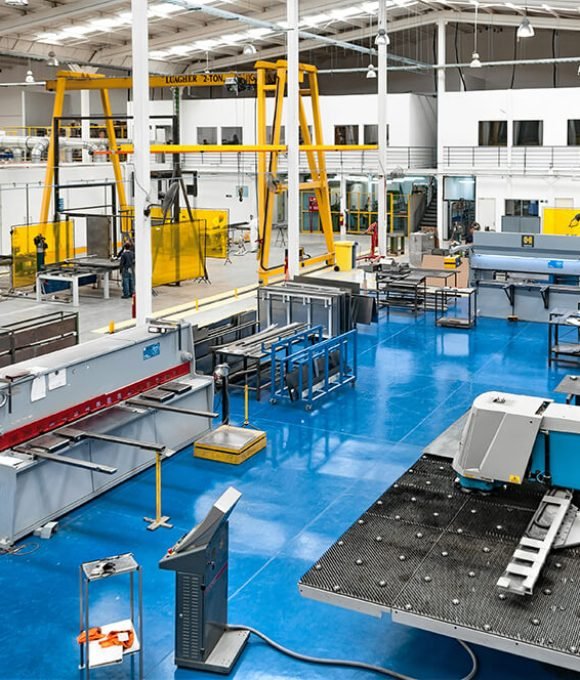
Quality Certifications
- ISO 9001:2015 Quality Management System
- CE Certification for European Market Compliance
- SGS Audited Supplier Status for all our slitting and rewinding machines.
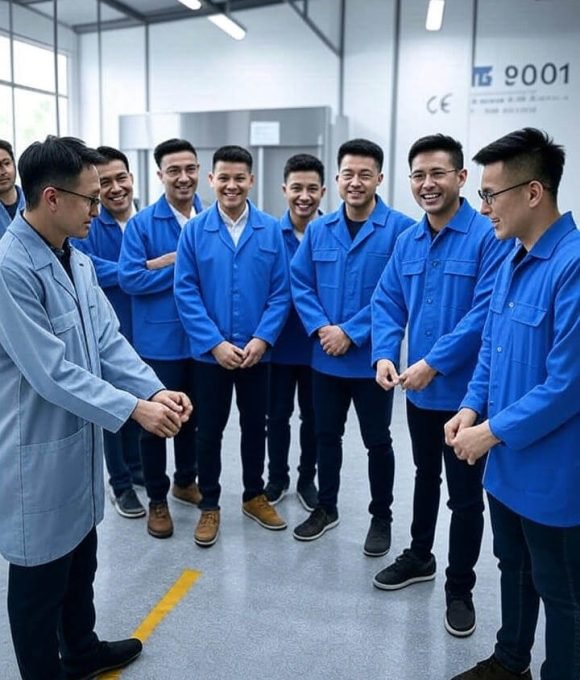
Unmatched After-Sales Service & Support
We have a growing network of overseas service points and authorized agents in Southeast Asia, Europe, and the Americas to ensure prompt local support for your slitting and rewinding machine.
Our Service Commitments
- 24/7 remote technical support and troubleshooting for your slitter.
- Scheduled preventive maintenance programs and on-site servicing for all slitting machines.
- Comprehensive operator training and detailed maintenance guides (e.g., slitter slider lubrication, film slitter knife care).
12+
Years of Experience
500+
Customer Cases
20+
Patented Technologies
98%
Customer Satisfaction
Industries That Rely on Foil Slitting Machines
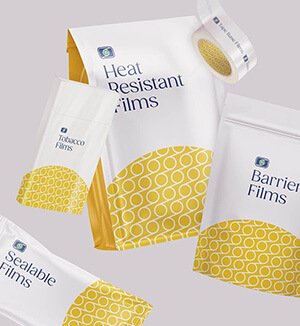
Flexible Packaging & Household Foil
Slitting systems engineered for aluminium foils used in food wrapping, blister packs, and household rolls. Ensure clean cuts and uniform rewinds to maintain sealing performance and aesthetic appearance.
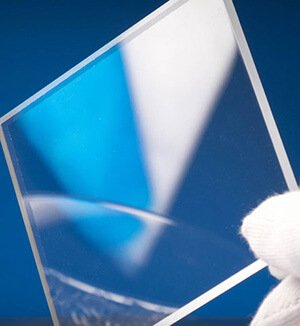
Electronics & PCB Manufacturing
Precision copper foil slitters for printed circuit boards, flexible circuits, and electromagnetic shielding. Deliver burr-free edges and tight width control essential for signal integrity and downstream processing.
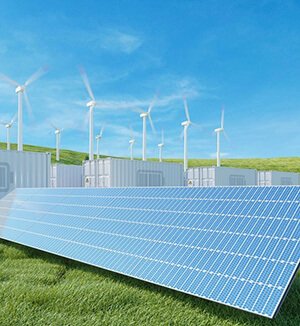
Battery & Energy Storage
High-accuracy slitting of anode and cathode foils in lithium-ion batteries. Support clean edge formation and layer uniformity to enhance battery performance, safety, and cycle life.
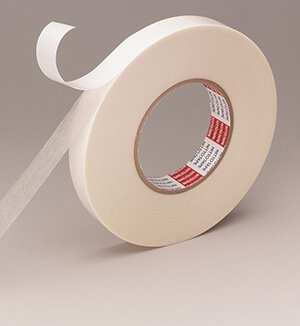
Capacitor & Transformer Foil Production
Customized slitting machines for aluminium, zinc, and silver foils used in capacitors and transformer windings. Maintain flat edges and tight tolerances for consistent electrical performance.
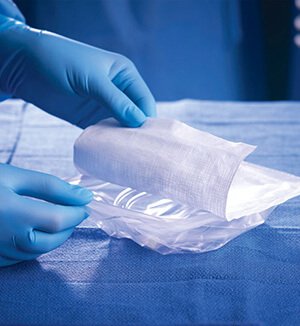
Label Foil & Decorative Laminate Converting
Slitting solutions for metallized foils used in pressure-sensitive labels, holographic films, and decorative laminates. Prevent surface scratches and support narrow-width converting with precision edge control.
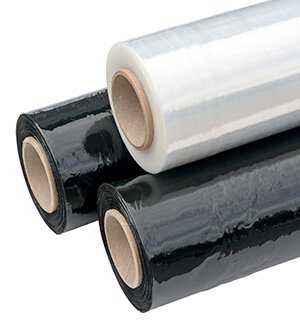
Medical & Pharmaceutical Foil Applications
Slitting systems designed for cleanroom-ready aluminium foils used in blister packs, sterile barriers, and diagnostic packaging. Minimize contamination while preserving foil integrity.
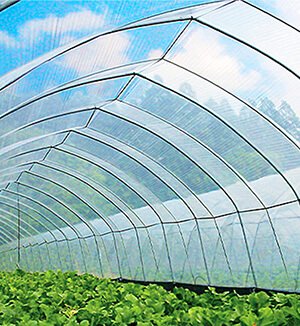
Industrial & Insulation Foils
Heavy-duty foil slitters for HVAC insulation foil, radiant barriers, and laminated vapor barriers. Ensure robust tension control and clean edge quality for large-format, multi-layer foils.
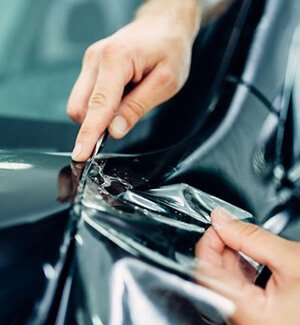
Automotive & Aerospace Foils
Advanced slitting solutions for aluminium and copper foils used in EV components, EMI shielding, and lightweight structural materials. Support high-precision processing for critical performance requirements.
A Real-World Success Story: Marco's Transformation with DJH Machinery
To demonstrate the practical impact of our Metal Foil Slitting Machine (Model MFS-1600), we present the inspiring journey of Mr. Marco Rosetti, a second-generation business owner from Italy who modernized his family’s aluminum foil processing operation through strategic investment in precision slitting technology.
From Traditional Methods to Modern Excellence
Our partnership with Marco began in 2019, when he inherited his father’s aluminum foil converting business in Milan. Rosetti Foil Industries had been serving the Italian food packaging market for over 30 years, but Marco faced mounting challenges with their aging slitting equipment—uneven cuts, frequent maintenance issues, and limited capacity were preventing the company from meeting growing demand from artisanal food producers and high-end restaurants.
Marco realized that to honor his father’s legacy while securing the company’s future, he needed to embrace modern technology. What he sought wasn’t merely equipment replacement—it was a comprehensive upgrade to achieve superior cutting precision, increased throughput, and expanded material handling capabilities.
The Pivotal Factory Visit: Seeing Innovation Firsthand
In early 2020, just before the global pandemic, Marco made a crucial decision to visit our manufacturing facility in Wenzhou, China. Despite initial travel concerns, he was determined to evaluate our technology personally. Our engineering team provided an extensive demonstration of the MFS-1600 Metal Foil Slitting Machine, highlighting its advanced features:
- Pneumatic knife positioning with 0.1mm accuracy
- Advanced anti-static system for thin foil handling
- Multi-zone tension control across the web width
- Servo-driven rewinding with constant surface speed
- Integrated dust collection system
Marco was particularly fascinated by the machine’s ability to process ultra-thin 6-micron aluminum foil at speeds up to 400m/min without tearing or wrinkling—a capability his existing equipment couldn’t match.
Technical Excellence Meets Practical Needs
What sealed Marco’s confidence was witnessing the machine handle various foil grades, from standard household aluminum to specialized barrier films with multiple layers. Our technical team also demonstrated the automatic core loading system and web inspection technology that could detect and mark defects in real-time.
Understanding the unique requirements of the Italian market, we customized the machine with European CE certification, Italian-language HMI interface, and special tension control algorithms optimized for the delicate foils used in traditional Italian food packaging.
Three months after his visit, Marco committed to the investment, making Rosetti Foil Industries our flagship client in Southern Europe.
Remarkable Results and Market Expansion
Since installing the MFS-1600 in late 2020, Rosetti Foil Industries has achieved extraordinary growth. Production capacity increased by 140%, while material waste dropped by 22%. The enhanced cutting quality enabled Marco to enter new market segments, including:
- Luxury chocolate packaging for premium Italian confectioners
- Pharmaceutical blister packaging for local drug manufacturers
- Industrial laminating foils for automotive applications
In 2023, the company was selected as the “Supplier of the Year” by the Italian Packaging Manufacturers Association, recognizing their commitment to quality improvement and technological advancement.
Building a Strategic Alliance
Marco’s success story continues to evolve. In 2024, he expanded his relationship with DJH Machinery by adding automated core cutting equipment and a foil embossing unit to create value-added products. What began as a machine purchase has developed into a strategic alliance built on mutual trust—precision engineering, continuous innovation, and sustainable growth.
Today, Rosetti Foil Industries stands as a testament to how the right technology partnership can transform a traditional family business into a modern industry leader.
What is metal foil slitting and how does it work?
Metal foil slitting is a converting process that cuts wide rolls of metal foil—such as aluminum, copper, or nickel—into narrower strips using rotary blades or razors. The process typically involves unwinding, tension control, precision slitting, and rewinding.
What types of metal foils can be slit with your machines?
What is the minimum and maximum thickness your machines can handle?
How do you prevent burrs and edge defects during slitting?
What is the typical slitting accuracy for width control?
Can your foil slitting machines handle coated or laminated foils?
Do you offer machines for lithium battery electrode foil slitting?
What tension control systems are used in your machines?
Comprehensive Guide to Choosing the Right Aluminum Foil Slitting Machine
Selecting the ideal aluminum foil slitting machine is a pivotal decision for businesses involved in foil production, impacting efficiency, product quality, and profitability. With the global market for these machines projected to grow from approximately $1.5 billion in 2025 to $2.5 billion by 2033, driven by rising demand in food packaging, pharmaceuticals, and industrial sectors, a thorough evaluation is essential. This guide provides an in-depth look at key considerations, enriched with technical details, market insights, and practical advice to ensure you choose a machine that meets both current and future needs.
1. Production Demand
Understanding your production requirements is the foundation of selecting the right machine. Aluminum foil varies significantly in thickness, width, and hardness, and its intended application dictates the machine’s specifications.
- Material Type and Application: Aluminum foil is used across diverse industries, each with unique requirements:
- Food Packaging: Requires thin, flexible foils with high-speed slitting and minimal defects to ensure cost-effective production.
- Pharmaceuticals: Demands high precision and cleanliness to meet regulatory standards for packaging medications.
- Electronics and Lithium-ion Batteries: Needs ultra-precise, burr-free cuts to ensure performance and safety in applications like printed circuit boards and battery foils.
Ensure the machine can handle your specific foil type, whether hard-rolled or soft-annealed, and meets the precision demands of your industry.
- Slitting Specifications: Define the required slitting width, length, and accuracy based on your production needs. For high-speed production, particularly in battery manufacturing, the machine must maintain precision without damaging the foil. Consider the maximum roll diameter and width to align with storage and handling capabilities.
2. Machine Performance
The performance of an aluminum foil slitting machine directly affects production efficiency and product quality. Key performance factors include:
- Tension Control: Precise tension control is critical, especially at high speeds, to prevent stretching or tearing of the foil. Advanced systems, often incorporating self-adhesive rubber cork tapes, ensure consistent tension across varying speeds, including acceleration and deceleration.
- Slitting Methods: Different cutting methods offer distinct advantages:
- Gang Cutting: Ideal for burr-free, high-quality slitting, particularly for metal foils used in battery applications.
- Rotary Cutting: Suitable for high-speed production with certain materials, offering flexibility in width adjustments.
- Automation Level: Modern machines feature programmable logic controllers (PLCs), touch screen interfaces, and advanced automation capabilities like automatic splicing, waste rewinding, and defect detection. These features reduce labor costs, minimize errors, and enhance productivity.
- Precision and Stability: For applications in electronics or batteries, the machine must deliver consistent width accuracy and burr-free cuts. High-precision machines are essential to meet stringent quality standards, minimizing roughness and improving performance in downstream processes.
3. After-sales Service
Reliable after-sales support ensures the machine operates efficiently throughout its lifespan.
- Supplier Reputation: Choose a supplier with a proven track record in the industry. Companies like KETE and DJH Machinery are recognized for their quality and reliability.
- Technical Support: Comprehensive support, including installation, operator training, and maintenance, is vital. Suppliers should offer prompt assistance to minimize downtime.
- Warranty and Service Contracts: Understand the warranty period and what it covers. Service contracts for regular maintenance can extend the machine’s lifespan and maintain performance.
- Local Support: For international suppliers, verify the availability of local technical support or the supplier’s ability to provide timely assistance, especially for urgent repairs.
4. Cost Considerations
Cost is a critical factor, but it’s important to look beyond the initial purchase price.
- Total Cost of Ownership (TCO): Consider all costs, including:
- Initial Purchase: Compare prices across brands, balancing cost with performance and features.
- Installation and Training: Factor in setup and operator training expenses.
- Operating Costs: Evaluate energy consumption, maintenance, and spare parts costs.
- Downtime Costs: Machines with high reliability reduce losses from unexpected breakdowns.
- Scalability: Choose a machine that can handle current production volumes and accommodate future growth. Machines with adjustable settings or upgrade options offer flexibility.
5. Site Inspection and Testing
Before finalizing your purchase, conduct thorough evaluations to ensure the machine meets your expectations.
- Machine Demonstration: Request a demonstration at the supplier’s facility to observe the machine’s performance, noise levels, and ease of operation.
- Trial Run: If possible, test the machine with your specific material to verify compatibility and performance.
- Safety and Ergonomics: Assess safety features, such as emergency stops and guards, and ensure the machine is ergonomically designed for operators.
6. Environmental Impact
Sustainability is increasingly important in manufacturing.
- Energy Efficiency: Opt for machines with energy-saving features to reduce operational costs and environmental impact.
- Waste Management: Evaluate how the machine handles scrap foil and whether it supports recycling processes.
- Regulatory Compliance: Ensure the machine complies with local and international environmental standards, aligning with consumer demand for sustainable practices.
7. Integration and Compatibility
The machine should integrate seamlessly with your existing operations.
- Compatibility with Production Lines: Verify that the machine can be integrated with your current equipment to avoid workflow disruptions.
- Data Integration: Advanced machines offer data logging and integration with enterprise resource planning (ERP) systems, enabling better production tracking and optimization.
8. Brand Reputation and References
A supplier’s reputation and real-world performance are critical indicators of reliability.
- Case Studies: Review case studies or visit reference sites to see how the machine performs in scenarios similar to yours.
- Industry Feedback: Seek reviews or feedback from other users in your industry to gauge the machine’s reliability and supplier support.
9. Market Trends and Future Outlook
The aluminum foil slitting machine market is experiencing robust growth, driven by several factors:
- Technological Advancements: Improvements in slitting technology, such as enhanced precision and automation, are increasing adoption rates.
- Growing Demand: The rise in e-commerce and consumer preference for convenient, safe packaging are boosting demand for aluminum foil, particularly in food and pharmaceutical sectors.
- Sustainability: Increasing focus on eco-friendly packaging is driving interest in machines that support sustainable practices.
- High-tech Applications: The growth of lithium-ion battery production and electronics manufacturing is creating demand for high-precision slitting machines.
Investing in a machine that aligns with these trends ensures long-term relevance.
Comparison Table of Key Considerations
Factor | Key Considerations | Why It Matters |
---|---|---|
Production Demand | Material type, application (e.g., food, pharma, electronics), slitting specifications | Ensures the machine meets specific industry and output requirements |
Machine Performance | Tension control, slitting methods, automation, precision | Impacts efficiency, product quality, and operational costs |
After-sales Service | Supplier reputation, technical support, warranty, local support | Reduces downtime and ensures long-term reliability |
Cost Considerations | Total cost of ownership, scalability | Balances initial investment with long-term profitability |
Environmental Impact | Energy efficiency, waste management, regulatory compliance | Aligns with sustainability goals and reduces operational costs |
Integration | Compatibility with existing systems, data integration | Enhances workflow efficiency and production tracking |
Testing and Inspection | Demonstrations, trial runs, safety features | Confirms performance and ensures operator safety |
Choosing the right aluminum foil slitting machine requires a comprehensive evaluation of production needs, machine performance, after-sales support, costs, and environmental considerations. By incorporating market trends, such as the growing demand for sustainable packaging and high-precision applications, you can select a machine that not only meets your immediate requirements but also supports long-term growth and competitiveness. Thorough research, supplier evaluations, and hands-on testing will ensure you invest in a machine that enhances efficiency, quality, and profitability.