Premium Stainless Steel Clad Rollers for Industrial Applications
Featured Stainless Steel Clad Rollers Product
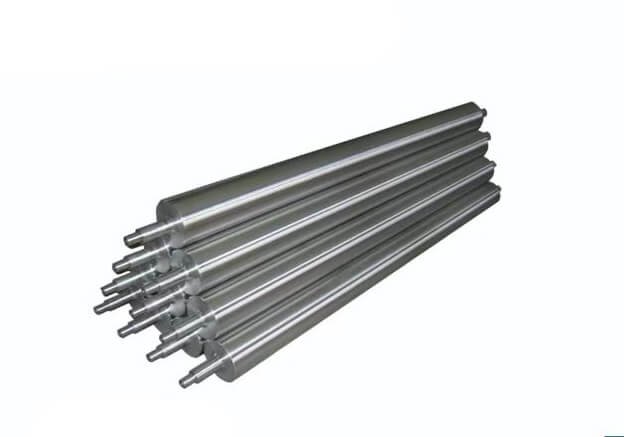
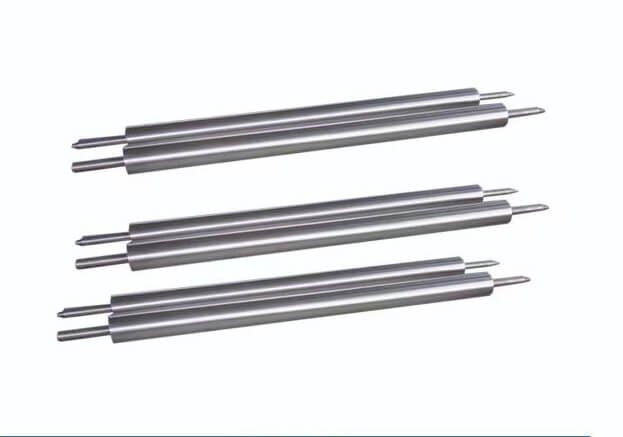
Product Specifications – Stainless Steel Clad Rollers | |
---|---|
Materials | 201 Stainless Steel + A3 Steel Composite, 304 Stainless Steel + A3 Steel Composite; Shaft Ends: Optional 304 Stainless Steel or 45# Steel |
Roller Diameter | Ø50, Ø60, Ø75, Ø90, Ø100, Ø125, Ø150, Ø180, Ø200 |
Manufacturing Process | Stainless steel plate is laminated with A3 steel, formed into a cylindrical tube through die pressing, then machined into guide rollers |
Key Features | Cost-effective, excellent concentricity, solvent-resistant, high-temperature resistant, wear-resistant |
Typical Applications | Textile dyeing, leather processing, nonwoven fabric, film handling, conveyor guide rollers |
High-Performance Rollers for Industrial Precision and Hygiene
Corrosive & Wet Environments
Designed for operations frequently exposed to chemicals, cleaning agents, steam, or high humidity. The corrosion-resistant surface ensures long-term performance without rust or degradation. Key Benefit: Ideal for chemical processing, sanitation-heavy environments, and moisture-prone areas.
Heavy-Duty & Abrasive Applications
Built for handling abrasive substrates such as specialty papers, coated materials, and foils. The hardened stainless steel surface resists wear and maintains dimensional stability. Key Benefit: Low maintenance and reliable performance in high-friction production lines.
Food-Grade & Pharmaceutical Use
Engineered with a non-porous, easy-to-sanitize finish, these rollers meet hygiene standards for food, pharma, and cleanroom manufacturing, minimizing contamination risk. Key Benefit: Meets sanitary regulations and supports sterile production conditions.
Temperature-Controlled Processes
Stainless steel cladding applied to heated or cooled cores provides strong thermal conductivity with corrosion resistance—ideal for precision temperature control. Key Benefit: Maintains surface integrity and thermal efficiency for critical processing tasks.
Engineered for Performance: Inside Clad Roller Technology
1. Precision Core Fabrication
2. High-Integrity Cladding Process
3. Advanced Surface Finishing
4. Performance-Driven Material Pairing
5. Built for Industrial Versatility
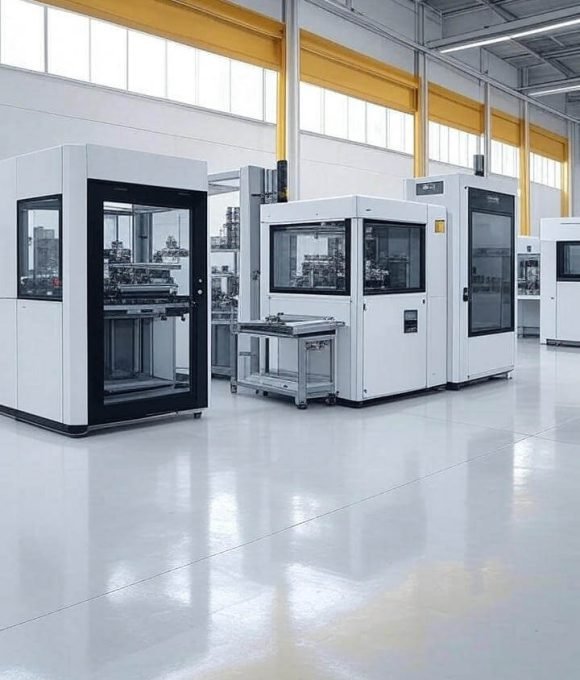
Get Our Free Samples
What Are Stainless Steel Clad Rollers?
Stainless steel clad rollers are precision-engineered cylindrical components featuring a core material (typically carbon steel or aluminum) that is completely encased or “clad” with a layer of stainless steel. This cladding process creates a roller that combines the structural strength and cost-effectiveness of the core material with the superior corrosion resistance, hygiene properties, and aesthetic appeal of stainless steel.
The fundamental principle behind stainless steel clad rollers lies in the metallurgical bonding process that permanently joins the stainless steel cladding to the base material. This bonding can be achieved through various methods including explosive welding, roll bonding, or diffusion bonding, each creating a strong, durable interface that performs as a single, unified component.
Stainless steel clad rollers function by providing a corrosion-resistant surface that maintains its properties even under demanding operating conditions. The stainless steel cladding protects the core material from environmental factors while providing a smooth, hygienic surface suitable for applications requiring cleanliness, chemical resistance, or aesthetic appeal. This design approach allows manufacturers to achieve the performance benefits of solid stainless steel construction while maintaining cost-effectiveness through the use of less expensive core materials.
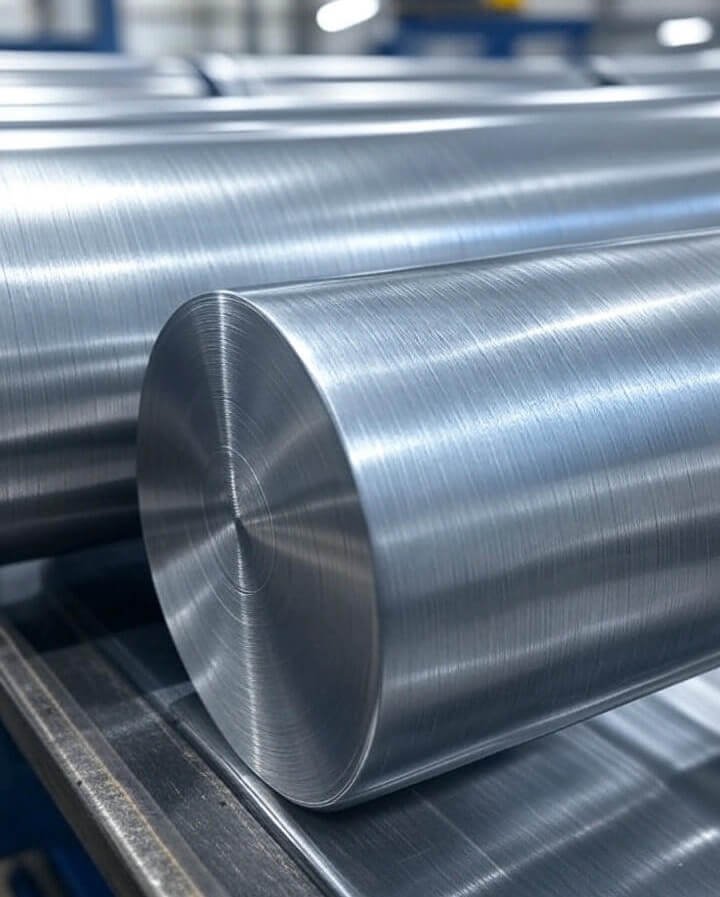
Industrial Applications Across Various Sectors
Stainless steel clad rollers serve critical roles across numerous industries, each leveraging the unique combination of strength, corrosion resistance, and hygiene properties for specific operational advantages.
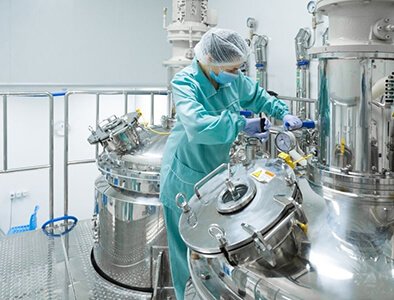
Food Processing Industry
extensively utilizes stainless steel clad rollers in applications requiring strict hygiene standards and frequent cleaning. These rollers are essential in meat processing, dairy operations, bakery equipment, and beverage production lines. The smooth, non-porous surface prevents bacterial growth and allows for effective sanitization using standard cleaning protocols. FDA-approved stainless steel grades ensure compliance with food safety regulations.
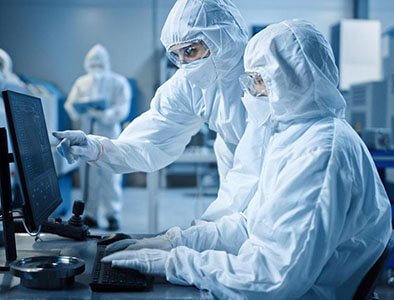
Pharmaceutical and Biotechnology Industries
Pharmaceutical and Biotechnology Industries rely on stainless steel clad rollers for manufacturing processes requiring contamination-free environments. These rollers meet stringent validation requirements and can withstand aggressive cleaning and sterilization procedures including steam sterilization, chemical sanitization, and clean-in-place (CIP) systems.
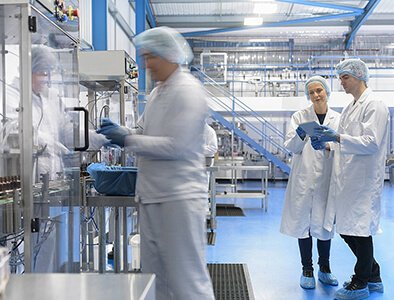
Chemical Processing Industry
Chemical Processing Industry employs stainless steel clad rollers in applications involving corrosive chemicals, acids, and bases. The chemical resistance of stainless steel cladding protects against attack from process chemicals while maintaining structural integrity. Specialized alloy cladding can handle even more aggressive chemical environments.
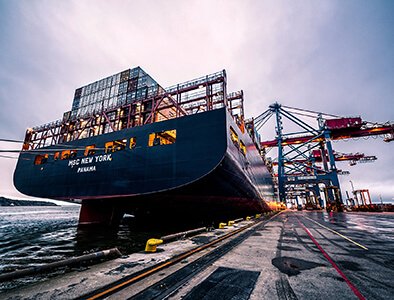
Marine and Offshore Industries
Marine and Offshore Industries utilize stainless steel clad rollers in applications exposed to saltwater and marine atmospheres. The chloride resistance of marine-grade stainless steels prevents pitting and crevice corrosion that would quickly destroy carbon steel components.
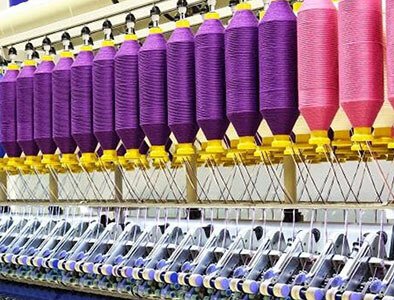
Textile Industry
Textile Industry uses stainless steel clad rollers in dyeing, finishing, and coating processes where chemical resistance and smooth surface finish are essential. These rollers withstand exposure to dyes, bleaches, and other textile chemicals while maintaining dimensional stability.
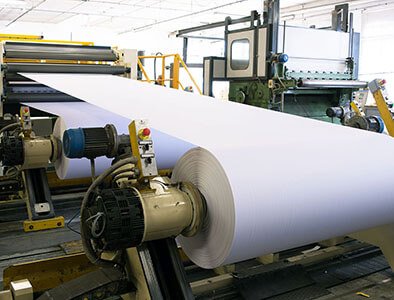
Paper and Pulp Industry
Paper and Pulp Industry employs stainless steel clad rollers in coating, calendering, and converting processes. The corrosion resistance is particularly valuable in applications involving paper chemicals, while the smooth surface finish ensures consistent paper quality.
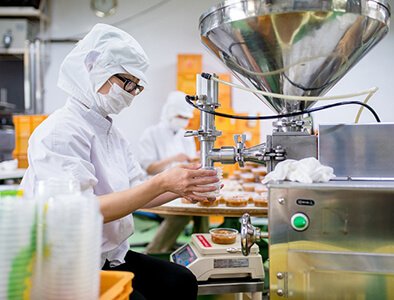
Medical Device Manufacturing
Medical Device Manufacturing requires stainless steel clad rollers for processing biocompatible materials and maintaining clean room standards. The rollers must meet strict cleanliness requirements and often require validation for medical device applications.
Selection Criteria for Stainless Steel Clad Rollers
Custom Stainless Steel Clad Roller Specifications
Dimensional Specifications
Dimensional Specifications must include all critical dimensions including diameter, length, shaft configurations, keyways, and any special geometric features. These specifications must account for manufacturing tolerances and operational clearances required for proper installation and operation.
Core Material Selection
Core Material Selection depends on mechanical requirements, cost considerations, and compatibility with the cladding process. Carbon steel cores provide cost-effective strength for most applications. Alloy steel cores offer enhanced strength for high-load applications. Aluminum cores provide lighter weight and may be preferred for applications requiring reduced inertia.
Cladding Material Specification
Cladding Material Specification must identify the specific stainless steel grade, thickness requirements, and any special properties needed. This specification should reference relevant standards such as ASTM or AISI designations and include requirements for chemical composition, mechanical properties, and corrosion resistance.
Surface Finish Requirements
Surface Finish Requirements should specify the desired surface roughness, measurement methods, and any special surface treatments. This may include electropolishing for enhanced corrosion resistance, passivation for improved cleanliness, or special texturing for functional requirements.
Performance Requirements
Performance Requirements must clearly define operational parameters including temperature ranges, chemical exposure conditions, mechanical loads, speed limitations, and expected service life. These specifications help manufacturers select appropriate materials and processes.
Quality and Testing
Quality and Testing Requirements may include specific inspections, tests, or certifications required for the application. This could include dimensional verification, bond strength testing, corrosion resistance testing, or material certification requirements.
Special Features
Special Features might include internal cooling passages, special mounting configurations, integral instrumentation, or other unique design elements required for the specific application.
Our Manufacturing Prowess & R&D Capabilities
Production Scale & Qualifications
- Factory Area: Over 10,000 square meters dedicated to manufacturing high-precision slitters and Accessories
- Annual Capacity: 200+ high-quality slitting machines for various materials.
- Certifications: ISO 9001, CE, Multiple Patents for advanced slitting technology.
R&D and Innovation
- Dedicated R&D Team: 12+ experienced engineers focused on slitter machine innovation.
- Technical Collaborations: Partnering with leading universities and research institutes for cutting-edge slitting solutions.
- Innovation Focus: Continuous development of intelligent and automated slitting and rewinding machines for paper, film, and foil.
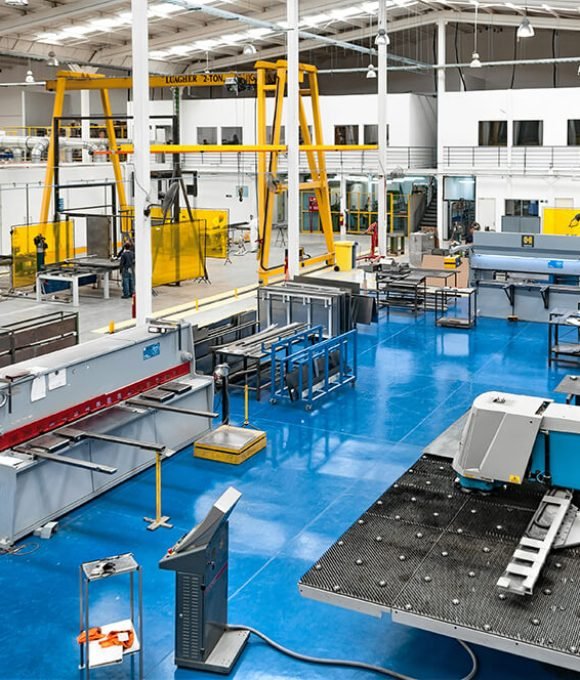
Quality Certifications
- ISO 9001:2015 Quality Management System
- CE Certification for European Market Compliance
- SGS Audited Supplier Status for all our slitting and rewinding machines.
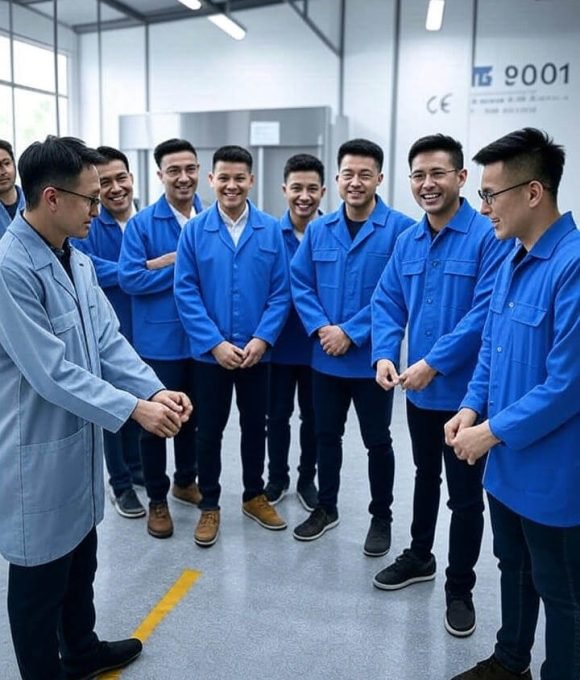
Unmatched After-Sales Service & Support
We have a growing network of overseas service points and authorized agents in Southeast Asia, Europe, and the Americas to ensure prompt local support for your slitting and rewinding machine.
Our Service Commitments
- 24/7 remote technical support and troubleshooting for your slitter.
- Scheduled preventive maintenance programs and on-site servicing for all slitting machines.
- Comprehensive operator training and detailed maintenance guides (e.g., slitter slider lubrication, film slitter knife care).