Precision Stainless Steel Wire Guide Rollers for Fine Wire and Narrow Web Handling
Featured Stainless Steel Wire Guide Rollers
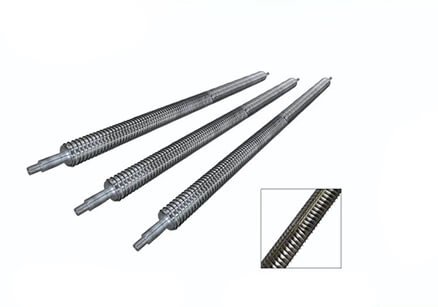
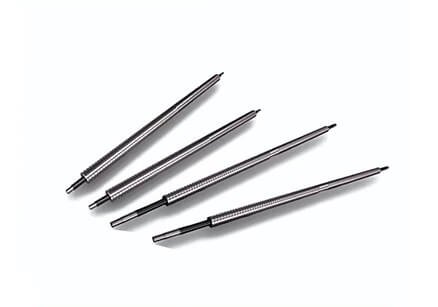
Product Specifications – Stainless Steel Wire Guide Rollers | |
---|---|
Materials | 304 stainless steel wire combined with stainless steel composite tube; optional shaft heads in 304 stainless steel or 45# steel |
Roller Diameter | Non-standard sizes available such as Ø60, Ø90, Ø100, Ø125, Ø150, Ø180, Ø200 mm; custom sizes available upon request |
Wire Types | Round wire, flat wire, trapezoidal wire |
Key Features | Suitable for high-speed machines; resistant to moisture, acids, alkalis, solvents, abrasion, and high temperatures |
Typical Applications | Web spreading and flattening for fabric, nonwoven materials, leather, film, and other substrates |
Precision Stainless Steel Wire Guide Rollers for Industrial Excellence
Corrosion-Resistant Performance in Harsh Environments
Built for operations exposed to chemicals, moisture, or high humidity, our Stainless Steel Wire Guide Rollers feature a rust-proof surface that ensures long-term reliability. Key Benefit: Perfect for chemical processing, wet conditions, and sanitation-focused industries.
Durability for Abrasive and High-Friction Tasks
Engineered to handle abrasive materials like specialty papers, coated substrates, and foils, these rollers maintain their shape and surface quality, resisting wear in demanding production lines. Key Benefit: Low maintenance and consistent performance for high-friction applications.
Hygienic Design for Food and Pharmaceutical Use
With a smooth, non-porous finish, our Stainless Steel Wire Guide Rollers meet strict hygiene standards, reducing contamination risks in food, pharma, and cleanroom environments. Key Benefit: Supports sterile conditions and complies with sanitary regulations.
Thermal Efficiency for Temperature-Sensitive Processes
Featuring stainless steel cladding on heated or cooled cores, these rollers offer excellent thermal conductivity and corrosion resistance for precise temperature control. Key Benefit: Ensures surface integrity and efficiency in critical manufacturing tasks.
Precision Engineered: Stainless Steel Wire Guide Roller Technology
1. Precision Core Manufacturing
2. Advanced Stainless Steel Cladding
3. Ultra-Precision Surface Finishing
4. Optimized Material Engineering
5. Wire Processing Excellence
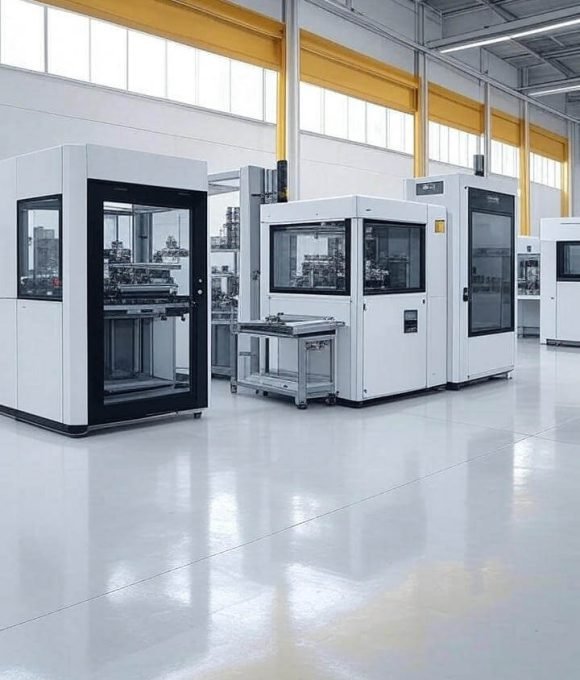
Get Our Free Wire Guide Roller Samples
What Are Stainless Steel Wire Guide Rollers?
Stainless steel wire guide rollers are precision-engineered components designed to direct and control wire movement in industrial applications. These specialized rollers provide smooth material guidance while minimizing friction and preventing wire damage during processing operations. Built from premium-grade stainless steel, they deliver outstanding durability and corrosion resistance, making them essential for wire drawing, cable manufacturing, and material handling systems where reliability is paramount.
The fundamental design principle of wire guide rollers centers on providing consistent contact points that maintain wire trajectory without causing surface damage or dimensional changes. Unlike standard conveyor rollers, wire guide rollers feature precisely machined surfaces with specific groove patterns or smooth cylindrical profiles that accommodate various wire diameters and materials. The stainless steel construction offers superior hardness characteristics, typically ranging from 316L for standard applications to 440C for high-wear environments.
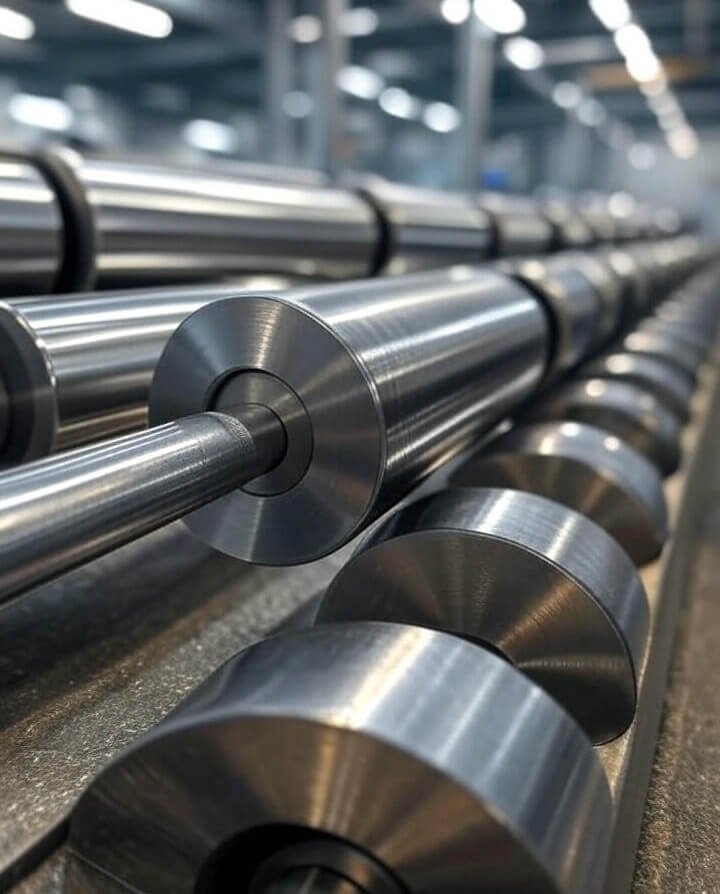
Types and Configurations of Wire Guide Rollers
Adjustable Guide Rollers
These versatile systems feature variable positioning mechanisms that accommodate multiple wire sizes and diameters, providing operational flexibility for diverse production runs and material changes. Adjustable rollers typically incorporate precision threaded adjustments or cam-operated mechanisms that allow operators to quickly modify roller spacing for different wire gauges. The adjustment range commonly spans from 0.5mm to 50mm wire diameters, with positioning accuracy maintained within ±0.02mm. These rollers often include locking mechanisms to prevent inadvertent adjustment during operation and graduated scales for precise positioning. Advanced adjustable systems may incorporate pneumatic or servo-controlled positioning for automated changeovers, reducing setup time and improving consistency. Some designs feature quick-release mechanisms that allow rapid roller replacement without tools, essential for high-volume production environments with frequent product changes.
Fixed Configuration Rollers
Engineered for specific wire dimensions, these units offer consistent performance with minimal setup requirements, ideal for high-volume single-wire operations. Fixed rollers are manufactured with precise groove dimensions matched to specific wire diameters, ensuring optimal contact and guidance. The groove geometry is typically designed with radii 10-15% larger than the wire diameter to prevent binding while maintaining positive guidance. These rollers excel in applications requiring maximum throughput and minimal maintenance intervention. The fixed design eliminates adjustment mechanisms, reducing potential failure points and maintenance requirements. Materials used in fixed roller construction often include premium stainless steel alloys with specialized heat treatments that achieve hardness levels exceeding Rockwell C 60.
Heavy-Duty Industrial Rollers
Constructed to withstand high loads and continuous operation, perfect for demanding manufacturing environments and large-diameter wire processing. These robust units feature reinforced construction with larger bearing systems, increased wall thickness, and enhanced mounting hardware. Load capacities typically range from 500N to 5000N, with some specialized units handling even higher loads. Heavy-duty rollers often incorporate sealed bearing systems with extended lubrication intervals, reducing maintenance frequency in continuous operation environments. The roller surfaces may feature specialized treatments such as chromium plating or ceramic coatings to enhance wear resistance and extend service life. Mounting systems for heavy-duty applications typically include precision-machined brackets with multiple adjustment points for optimal alignment.
Industrial Applications Across Various Sectors
Stainless steel clad rollers serve critical roles across numerous industries, each leveraging the unique combination of strength, corrosion resistance, and hygiene properties for specific operational advantages.
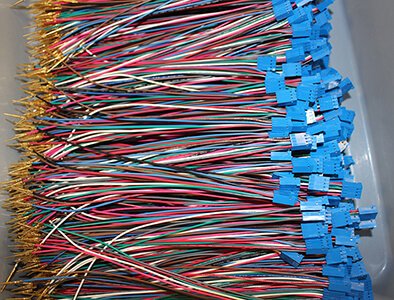
Wire Processing
Guide rollers are essential in wire drawing, forming, and inspection. They ensure accurate wire alignment during multi-pass drawing, handle high tensions (100–1000N), and prevent marking or distortion. In wire forming, rollers maintain bend consistency and accommodate various wire profiles, including flat and trapezoidal wires. For quality control, rollers stabilize wire position for diameter checks and defect detection without vibration.
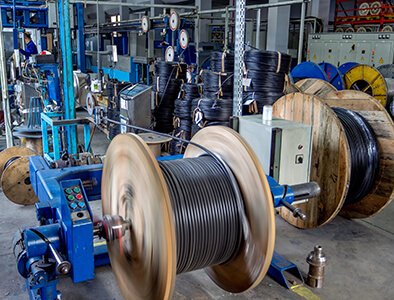
Cable Manufacturing
In cable production, guide rollers support conductor alignment during stranding, extrusion, and insulation. They maintain tension balance, operate under high temperatures, and ensure centered cable positioning for consistent wall thickness. In assembly, they aid automated connector installation by keeping cables stable and undamaged.
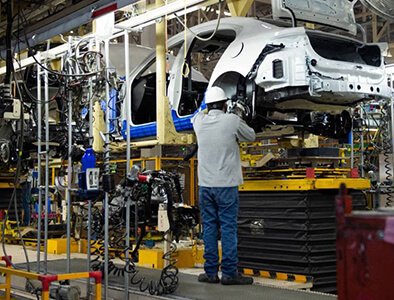
Automotive & Aerospace
In wire harness assembly and testing, precision rollers ensure exact wire positioning for routing and inspection. They support multiple wire types and enable consistent performance in automated production systems.
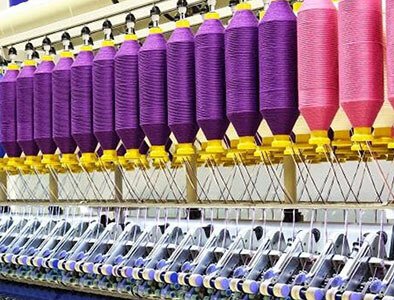
Textile Industry
Used in synthetic fiber and weaving processes, guide rollers manage high-speed filaments and yarns while resisting wear and chemicals. Their smooth, static-resistant surfaces prevent fiber damage. During dyeing and finishing, rollers provide precise fabric control in wet, corrosive environments.
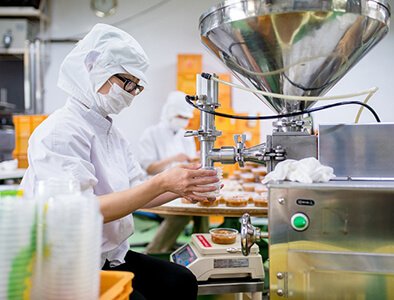
Packaging Systems
High-speed packaging lines rely on guide rollers for accurate wire and cable positioning during cutting, stripping, and coil winding. They maintain stability at speeds over 10 m/s and adapt to various wire sizes in automated processes.
Supplier Selection and Investment Considerations
Supplier Evaluation Criteria
Manufacturing capabilities assessment should include equipment sophistication, quality control systems, and production capacity. Suppliers with advanced CNC machining capabilities and comprehensive testing facilities typically produce higher-quality products with better consistency. Technical expertise evaluation should consider engineering support capabilities, application experience, and problem-solving track record. Suppliers with strong technical teams can provide valuable assistance in product selection, installation, and troubleshooting. Quality certifications such as ISO 9001, AS9100, or industry-specific standards indicate established quality management systems. Specific certifications may be required for food-grade, aerospace, or other specialized applications.
Customization Capabilities
Many applications require customized roller designs to meet specific requirements. Supplier capabilities in custom engineering, prototyping, and small-batch production are important considerations for specialized applications. Design modification capabilities allow suppliers to adapt standard products for specific requirements, potentially reducing costs and delivery times compared to fully custom solutions. CAD modeling and simulation capabilities help optimize designs before manufacturing.
Cost Analysis and Value Proposition
Initial cost considerations include unit price, tooling costs for custom products, and minimum order quantities. However, total cost of ownership analysis should consider service life, maintenance requirements, and performance benefits. Quality-related costs include the impact of product failures, maintenance requirements, and performance limitations. Higher-quality rollers may justify premium pricing through improved reliability and performance.
Supply Chain Considerations
Delivery reliability is crucial for production planning and inventory management. Suppliers with strong supply chain management and flexible manufacturing capabilities can better respond to changing requirements. Technical support availability, including application engineering, installation assistance, and troubleshooting support, adds significant value to the supplier relationship. Local support capabilities may be important for time-sensitive applications.
Long-term Partnership Value
Suppliers who invest in ongoing product development and technology advancement provide long-term value through improved products and capabilities. Innovation in materials, manufacturing processes, and design approaches can provide competitive advantages. Supplier financial stability and business continuity planning ensure reliable supply over the product lifecycle. Backup supply arrangements may be necessary for critical applications.
Our Manufacturing Prowess & R&D Capabilities
Production Scale & Qualifications
- Factory Area: Over 10,000 square meters dedicated to manufacturing high-precision slitters and Accessories
- Annual Capacity: 200+ high-quality slitting machines for various materials.
- Certifications: ISO 9001, CE, Multiple Patents for advanced slitting technology.
R&D and Innovation
- Dedicated R&D Team: 12+ experienced engineers focused on slitter machine innovation.
- Technical Collaborations: Partnering with leading universities and research institutes for cutting-edge slitting solutions.
- Innovation Focus: Continuous development of intelligent and automated slitting and rewinding machines for paper, film, and foil.
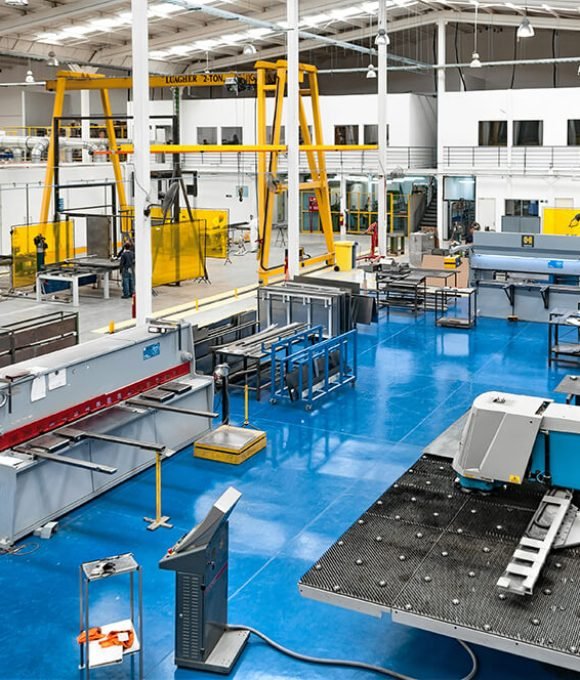
Quality Certifications
- ISO 9001:2015 Quality Management System
- CE Certification for European Market Compliance
- SGS Audited Supplier Status for all our slitting and rewinding machines.
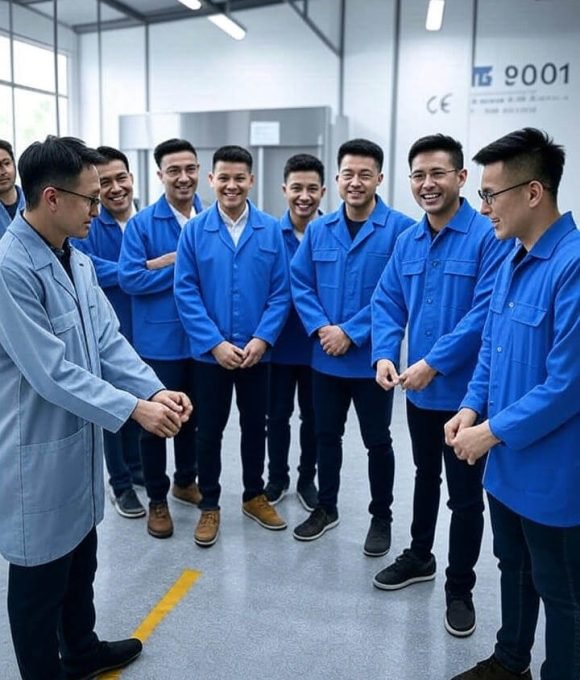
Unmatched After-Sales Service & Support
We have a growing network of overseas service points and authorized agents in Southeast Asia, Europe, and the Americas to ensure prompt local support for your slitting and rewinding machine.
Our Service Commitments
- 24/7 remote technical support and troubleshooting for your slitter.
- Scheduled preventive maintenance programs and on-site servicing for all slitting machines.
- Comprehensive operator training and detailed maintenance guides (e.g., slitter slider lubrication, film slitter knife care).