Premium Non-Stick PTFE Coated Rollers
DJH Machinery delivers expertly engineered non-stick rollers with advanced PTFE coating technology, providing exceptional release properties for demanding industrial applications. These specialized components offer ideal solutions for processes involving adhesives, sticky materials, hot plastics, and substances prone to surface adhesion. Our coated systems also provide excellent chemical resistance and temperature stability, ensuring versatile performance across diverse manufacturing environments.
Featured Teflon (PTFE) Coated Roller Product
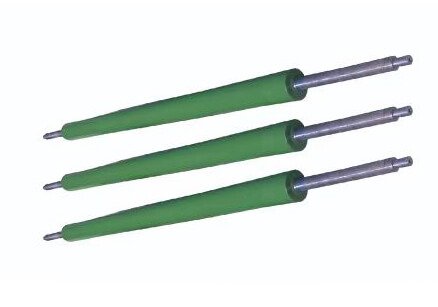
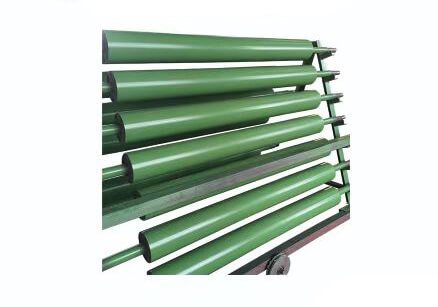
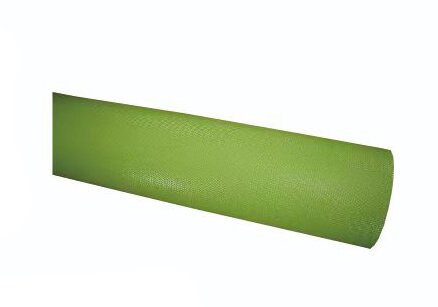
Product Specifications – PTFE Coated Rollers | |
---|---|
Materials | Aluminum Alloy, 45# Steel, 20# Steel, 40Cr Steel, 304 Stainless Steel |
Spray Coating Diameter | From Ø10mm to Ø1200mm |
Roller Length | Up to 8 meters |
Surface Finishing Options | Polishing, Sandblasting, Spray Coating, Oven Curing |
Optional Coating Colors | Green or Black PTFE (Teflon) Coating |
Key Features | Non-stick surface, Easy to clean |
Typical Applications | Tape, Fabric, Leather, Nonwoven Materials, Anti-adhesive Processing |
Key Applications for PTFE Coated Systems
Adhesive Coating & Laminating Operations
Precision release systems designed for tape manufacturing and coating processes, featuring anti-adhesive surfaces that eliminate build-up, prevent web contamination, and ensure continuous operation without wrap-around issues.
Hot Melt & Extrusion Manufacturing
High-performance non-stick systems built for molten plastics and tacky extruded materials, delivering smooth material transport without adhesion or deformation during critical processing stages.
Food Processing & Packaging
Food-grade non-stick systems designed for dough, confectionery, and sticky food products, ensuring hygienic operation standards while preventing product loss and maintaining processing efficiency.
Printing & Converting Applications
Advanced ink-repellent components engineered for fountain systems and idler positions, providing simplified cleanup operations and preventing unwanted ink transfer with minimal maintenance requirements.
Advanced Coating Technology & Performance
1. PTFE Roller Manufacturing Process
2. Ultra-Low Friction Coefficient Benefits
3. Superior Material Handling Performance
4. Enhanced Durability and Chemical Resistance
5. Anti-Static Solutions for Specialized Applications
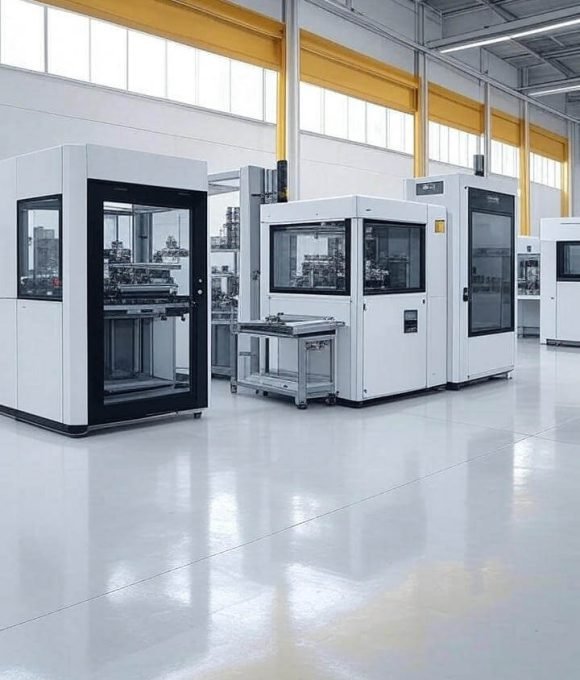
Get Our Free Samples
What Are PTFE Coated Rollers?
PTFE (Polytetrafluoroethylene) coated rollers are cylindrical components where a base material, typically steel or aluminum, is coated with a layer of PTFE material. PTFE, commonly known by the brand name Teflon, is a synthetic fluoropolymer that exhibits exceptional non-stick properties, chemical resistance, and thermal stability.
The fundamental principle behind PTFE coated rollers lies in combining the structural strength of traditional roller materials with the unique surface properties of PTFE. This combination creates a roller that can handle demanding applications while providing consistent performance over extended periods.
PTFE coated rollers work by utilizing the low coefficient of friction inherent in PTFE materials. When materials pass over or come into contact with these rollers, the PTFE coating reduces friction, prevents sticking, and ensures smooth material handling. This is particularly beneficial in applications involving adhesives, hot materials, or substances that tend to build up on conventional roller surfaces.
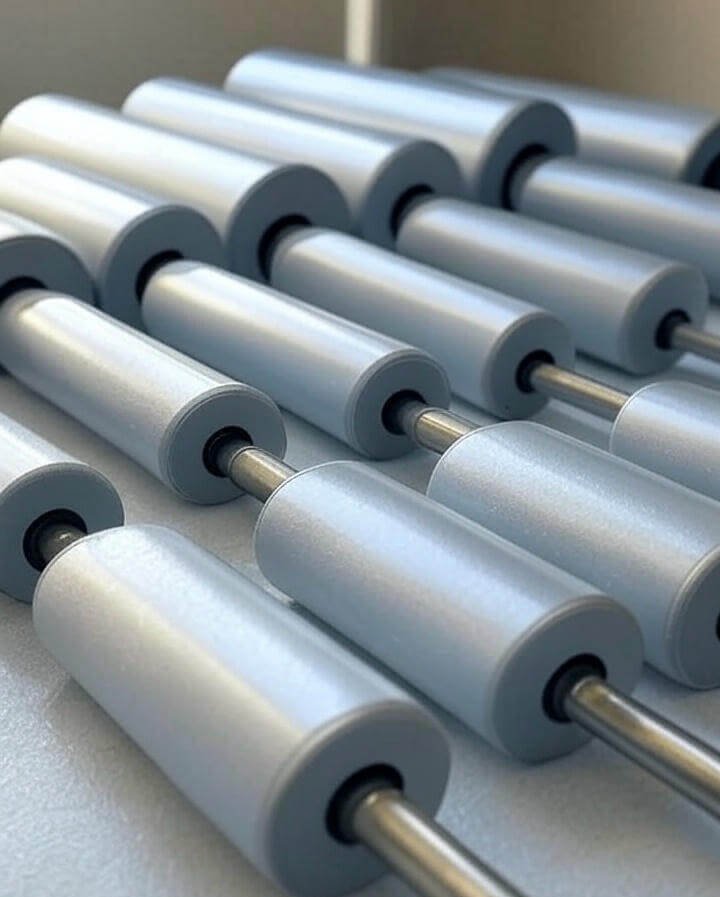
Different Types and Specifications of PTFE Coated Rollers
Standard PTFE Coated Rollers
Represent the most common type, featuring a uniform PTFE coating applied to a metal core. These rollers typically have coating thickness ranging from 0.1mm to 1.0mm, depending on the application requirements. The base materials commonly used include steel, stainless steel, and aluminum, each offering different strength and weight characteristics.
High-Temperature PTFE Coated Rollers
High-Temperature PTFE Coated Rollers are specifically designed for applications involving elevated temperatures. These rollers can operate continuously at temperatures up to 260°C (500°F) and intermittently at even higher temperatures. The PTFE formulation for these rollers often includes additives that enhance thermal stability and reduce thermal expansion.
Food-Grade PTFE Coated Rollers
Food-Grade PTFE Coated Rollers meet strict FDA regulations for food contact applications. These rollers use virgin PTFE materials and undergo special manufacturing processes to ensure they meet food safety standards. They are commonly used in food processing, packaging, and pharmaceutical applications.
Anti-Static PTFE Coated Rollers
Anti-Static PTFE Coated Rollers incorporate conductive additives into the PTFE coating to prevent static electricity buildup. These are essential in applications involving plastic films, textiles, or other materials prone to static charging.
Precision PTFE Coated Rollers
Precision PTFE Coated Rollers are manufactured to extremely tight tolerances, with surface finish requirements measured in microinches. These rollers are used in applications requiring precise material handling, such as printing, laminating, and coating processes.
PTFE Coating Materials and Performance Grades
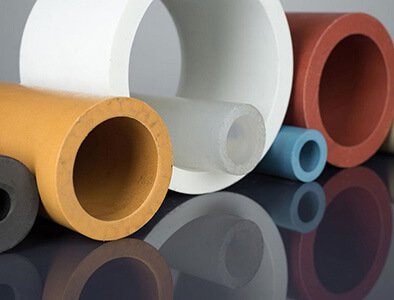
Virgin PTFE Coatings
Virgin PTFE Coatings offer the purest form of PTFE with maximum chemical resistance and lowest coefficient of friction. These coatings are ideal for applications requiring the highest level of non-stick performance and chemical inertness. Virgin PTFE coatings typically exhibit coefficients of friction as low as 0.05 to 0.1.
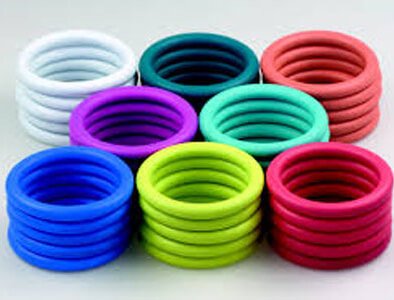
Filled PTFE Coatings
Filled PTFE Coatings incorporate various fillers to enhance specific properties. Glass-filled PTFE provides improved wear resistance and dimensional stability. Carbon-filled PTFE offers enhanced thermal conductivity and wear resistance. Bronze-filled PTFE provides superior load-bearing capabilities and wear resistance under high-pressure applications.
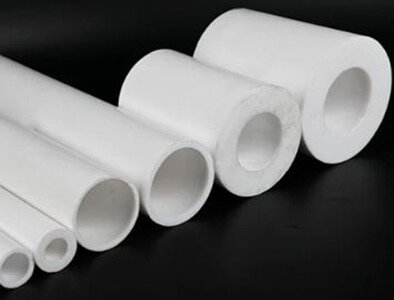
Modified PTFE Coatings
Modified PTFE Coatings use chemical modifications to improve adhesion, flexibility, or other specific properties. These modifications can include the addition of perfluoroalkoxy (PFA) or fluorinated ethylene propylene (FEP) to enhance certain characteristics while maintaining the core benefits of PTFE.
Technical Parameters and Their Meanings
Selection Criteria for PTFE Coated Rollers
Application Requirements Analysis
Application Requirements Analysis forms the foundation of roller selection. This includes understanding the materials being processed, operating temperatures, chemical exposure, load requirements, and precision needs. The operating environment, including ambient conditions and potential contaminants, must also be considered.
Material Compatibility
Material Compatibility assessment ensures that the PTFE coating formulation is suitable for the specific materials and chemicals encountered in the application. While PTFE offers broad chemical compatibility, certain aggressive chemicals or unique combinations may require specialized formulations.
Temperature Considerations
Temperature Considerations are critical in roller selection. The continuous operating temperature, peak temperatures, and thermal cycling patterns all influence coating selection and expected service life. Applications with rapid temperature changes may require special consideration for thermal expansion and contraction.
Load and Pressure Requirements
Load and Pressure Requirements determine the necessary coating thickness and base material specifications. High-pressure applications may require thicker coatings or specialized filling materials to prevent coating deformation or damage.
Surface Finish Requirements
Surface Finish Requirements depend on the specific application needs. Some applications require mirror-smooth surfaces for optimal release properties, while others may benefit from slightly textured surfaces for improved material handling.
Dimensional Tolerances
Dimensional Tolerances are particularly important in precision applications. The coating process can affect dimensional accuracy, so tolerances must be specified considering both the base roller and final coated dimensions.
Custom PTFE Roller Parameters and Specifications
Dimensional Specifications
Dimensional Specifications include roller diameter, length, shaft size, and any special geometric features. These dimensions must account for the coating thickness to ensure proper fit and function in the intended application.
Base Material Selection
Base Material Selection depends on application requirements including strength, weight, thermal conductivity, and cost considerations. Steel provides maximum strength and durability, aluminum offers lighter weight and better thermal conductivity, while stainless steel provides enhanced corrosion resistance.
Coating Specifications
Coating Specifications must detail the PTFE formulation, thickness requirements, surface finish, and any special properties needed. This includes specifying whether virgin PTFE, filled PTFE, or modified PTFE formulations are required.
Performance Requirements
Performance Requirements should clearly define operating temperature ranges, chemical exposure conditions, load requirements, and expected service life. These specifications help manufacturers select appropriate materials and processes.
Quality Standards
Quality Standards may include specific certifications such as FDA compliance for food applications, ISO standards for quality management, or industry-specific standards for specialized applications.
Testing Requirements
Testing Requirements might include specific tests for coating adhesion, chemical resistance, temperature performance, or other critical characteristics depending on the application.
Supplier Selection and Quality Considerations
Manufacturing Capabilities
Manufacturing Capabilities assessment should include coating equipment, quality control systems, testing capabilities, and production capacity. Suppliers with advanced coating equipment and comprehensive testing facilities typically produce higher-quality products.
Quality Certifications
Quality Certifications such as ISO 9001, AS9100, or industry-specific certifications indicate established quality management systems. FDA registration may be required for food-grade applications.
Technical Expertise
Technical Expertise evaluation should consider the supplier's understanding of PTFE technology, application engineering support, and problem-solving capabilities. Suppliers with strong technical teams can provide valuable application support and troubleshooting assistance.
Customization Capabilities
Customization Capabilities are important for applications requiring specialized rollers. This includes design engineering capabilities, prototype development, and flexible manufacturing processes.
Testing and Validation Services
Testing and Validation Services may include coating thickness measurement, adhesion testing, chemical resistance testing, and performance validation. Comprehensive testing capabilities ensure product quality and performance.
Supply Chain Reliability
Supply Chain Reliability considerations include supplier financial stability, backup manufacturing capabilities, and inventory management systems. Reliable suppliers help ensure consistent product availability and delivery performance.
Our Manufacturing Prowess & R&D Capabilities
Production Scale & Qualifications
- Factory Area: Over 10,000 square meters dedicated to manufacturing high-precision slitters and Accessories
- Annual Capacity: 200+ high-quality slitting machines for various materials.
- Certifications: ISO 9001, CE, Multiple Patents for advanced slitting technology.
R&D and Innovation
- Dedicated R&D Team: 12+ experienced engineers focused on slitter machine innovation.
- Technical Collaborations: Partnering with leading universities and research institutes for cutting-edge slitting solutions.
- Innovation Focus: Continuous development of intelligent and automated slitting and rewinding machines for paper, film, and foil.
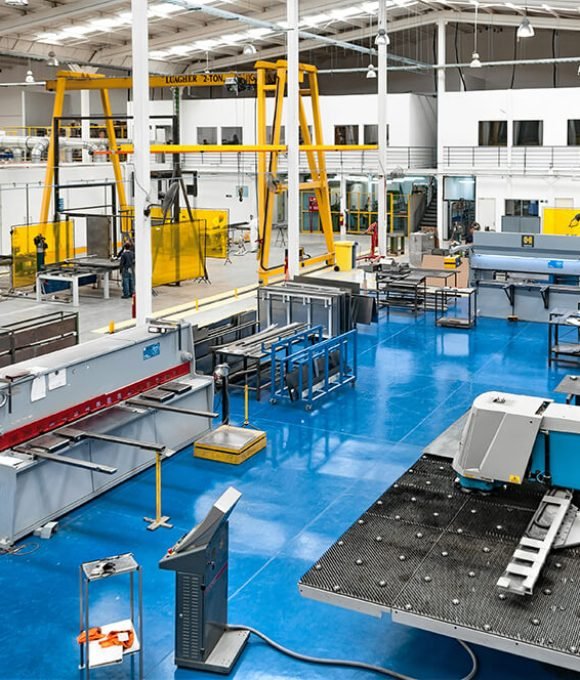
Quality Certifications
- ISO 9001:2015 Quality Management System
- CE Certification for European Market Compliance
- SGS Audited Supplier Status for all our slitting and rewinding machines.
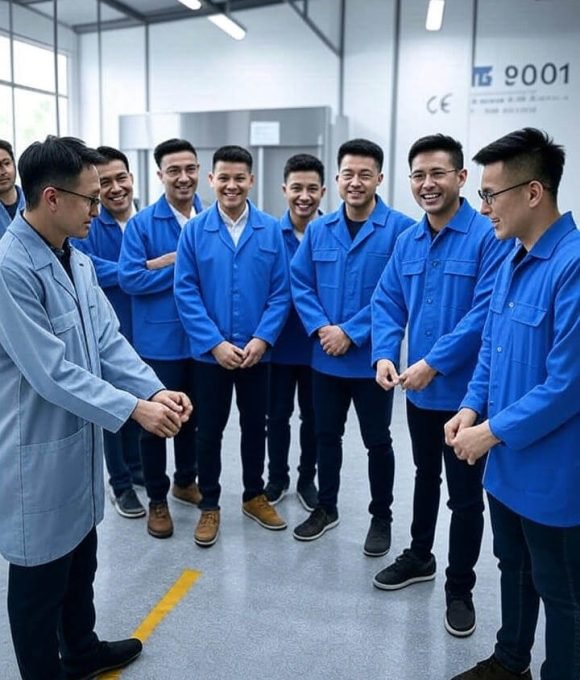
Unmatched After-Sales Service & Support
We have a growing network of overseas service points and authorized agents in Southeast Asia, Europe, and the Americas to ensure prompt local support for your slitting and rewinding machine.
Our Service Commitments
- 24/7 remote technical support and troubleshooting for your slitter.
- Scheduled preventive maintenance programs and on-site servicing for all slitting machines.
- Comprehensive operator training and detailed maintenance guides (e.g., slitter slider lubrication, film slitter knife care).