Thermal Paper Slitting Machines for Precision Roll Converting
Featured Thermal PaperSlitter Rewinder Machines
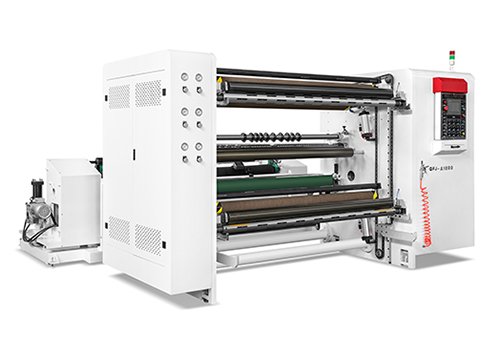
QFJ-A400 Horizontal High Speed Slitting Machine
- Key Specifications:
- Max Speed: 400m/min
- Min. Slitting Width: 30mm
- Unwinding Diameter 1200mm(Customizable)
- Rewinding Diameter 1000mm(Customizable)
- Key Specifications:
- Automatic unloading by chain
- Independent shaft free feeding
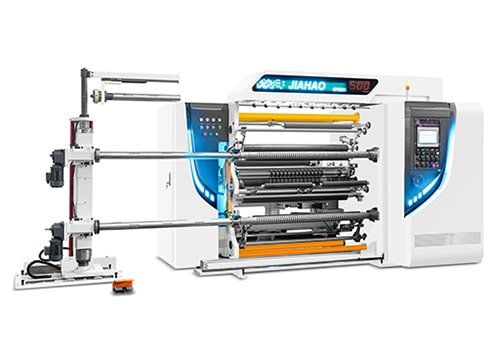
QFJ-A500 Horizontal High Speed Slitting Machine
- Key Specifications:
- Max Speed: 500m/min
- Min. Slitting Width: 20mm
- Unwinding Diameter 800mm(Customizable)
- Rewinding Diameter 600mm(Customizable)
- Key Specifications:
- Small Footprint of connected structures
- 4 Sets Servo Motor Controll
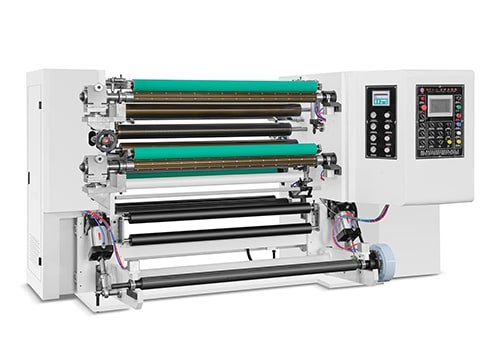
QFJ-B200 Vertical Slitting Machine
- Key Specifications:
- Max Speed: 200m/min
- Min. Slitting Width: 20mm
- Unwinding Diameter 700mm(Customizable)
- Rewinding Diameter 400mm(Customizable)
- Key Specifications:
- Small Footprint of connected structures
- 4 Sets Servo Motor Controll
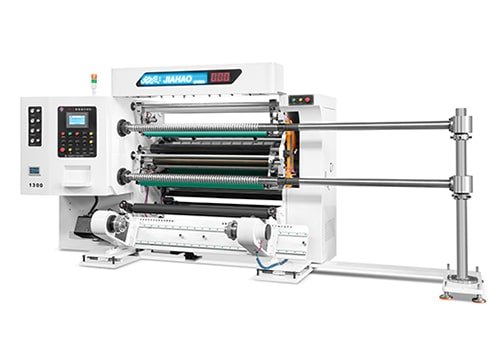
QFJ-B500 Vertical High Speed Slitting Machine
- Key Specifications:
- Max Speed: 500m/min
- Min. Slitting Width: 30mm
- Unwinding Diameter 750mm(Customizable)
- Rewinding Diameter 450mm(Customizable)
- Key Specifications:
- Automatic unloading by chain
- Independent shaft free feeding
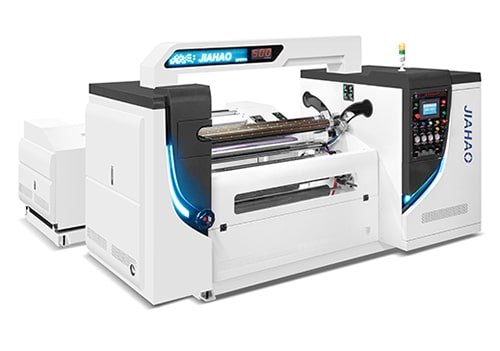
QFJ-C500 Surface Winding High Speed Slitting Machine
- Key Specifications:
- Max Speed: 500m/min
- Min. Slitting Width: 20mm
- Unwinding Diameter 1000mm(Customizable)
- Rewinding Diameter 600mm(Customizable)
- Key Specifications:
- Small Footprint of connected structures
- 4 Sets Servo Motor Controll
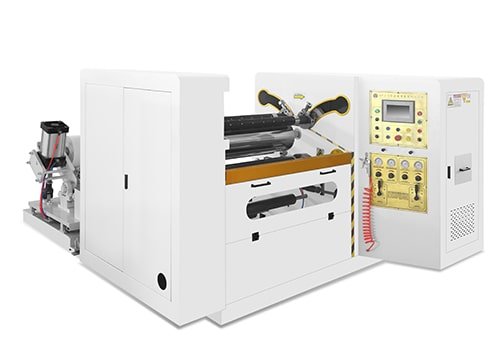
QFJ-C200 Series Surface Winding Slitting Machine
- Key Specifications:
- Max Speed: 200m/min
- Min. Slitting Width: 10mm
- Unwinding Diameter 1000mm(Customizable)
- Rewinding Diameter 600mm(Customizable)
- Key Specifications:
- Small Footprint of connected structures
- 4 Sets Servo Motor Controll
Specialized Thermal Paper Slitting Applications
POS & Cash Register Rolls
Efficient slitting for retail receipt rolls and credit card terminal paper, ensuring tight winding, accurate lengths, and consistent width. Ideal for fast-paced retail environments requiring reliable roll performance.
ATM & Kiosk Receipts
High-accuracy machines for ATM and self-service terminal rolls, delivering clean edges and precise dimensions to prevent jamming. Designed for smooth operation in automated dispensing systems.
Medical Chart & ECG Paper
Gentle web handling and exact slitting for ECG, ultrasound, and medical chart paper used in diagnostic and patient monitoring equipment. Protects sensitive coatings and preserves print clarity for healthcare use.
Lottery & Ticketing Paper
Slitting solutions for thermal lottery rolls, ticket stock, and travel vouchers with exact dimensions and tamper-resistant features. Supports secure, high-speed issuance of tickets and transactional documents.
Fax Paper & Thermal Transfer Media
Versatile equipment for direct thermal paper, fax rolls, and thermal transfer ribbons, with adjustable blade setups and material control. Enables multi-format production across legacy and modern printing systems.
Advanced Slitting Technology
Precision Slitting Process for Thermal Paper
1. Controlled Unwinding System
2. Accurate Web Alignment
3. High-Precision Slitting Module
4. Integrated Dust Extraction
5. Curl-Control Technology
6. Optimized Rewinding System
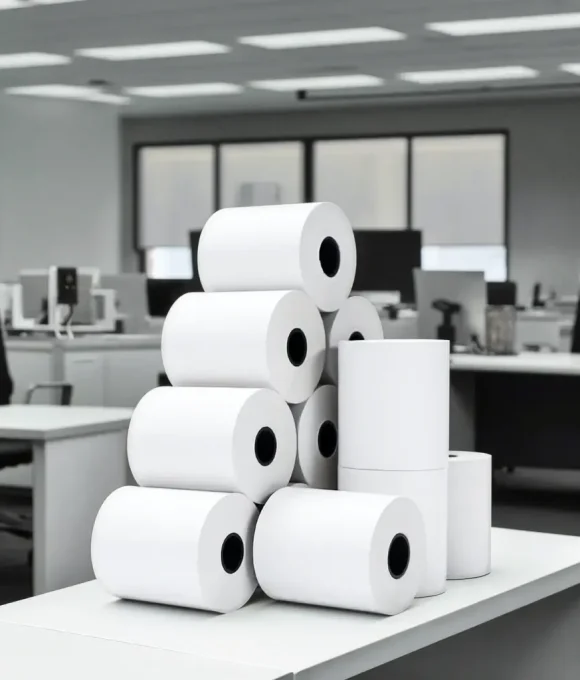
Turning Your Thermal Paper Slitting Challenges into Smart Engineering
Ensure Clean, Dust-Free Operation for Thermal Paper
Enclosed cutting zones, optimized blade angles, and high-efficiency vacuum extraction work together to minimize paper dust—keeping your rolls clean and protecting downstream equipment from contamination.
Reduce Maintenance with Clean, Accessible Machine Design
Modular structures, quick-blade access, and intelligent diagnostics simplify service and reduce unplanned downtime—ensuring smooth operation and long-term reliability.
Guarantee Consistent Roll Dimensions for POS
Servo-driven control systems and precise diameter monitoring ensure every roll meets your exact specifications—minimizing printer jams and maximizing efficiency in high-volume .
Protect Sensitive Thermal Coatings During Slitting
Low-tension unwind units and friction-optimized web paths reduce mechanical stress and heat generation, preserving coating integrity for long-lasting, high-contrast printing results.
Streamline Roll Handling for High-Speed Production Lines
Fully automated slitter rewinders with turret systems, recipe memory, and user-friendly HMIs reduce changeover time and operator error—supporting continuous, large-scale production.
Customized Thermal Paper Slitting Solutions
Every thermal paper converting line faces unique demands — that’s why we deliver fully customizable slitting systems engineered for your exact coating sensitivity, tension control, and high-speed production requirements.
Whether you’re slitting wide POS rolls, narrow medical-grade labels, or ultrathin ticket stock, our engineers design solutions for scratch-free surfaces, static elimination, and pristine edge quality.
What We Customize:
Machine Configuration
Robust frames, precision unwind/rewind stations, and optimized web paths for low-tension handling of heat-sensitive paper – tailored to your facility layout.
Slitting System
High-precision razor or rotary shear knives selected for coating integrity, minimal dust generation, and burr-free edges (even at 800+ FPM speeds).
Rewinding Technology
Gentle surface/center-wind systems, servo-tension controls, and coreless solutions to prevent coating transfer, edge damage, or roll telescoping.
Web Width & Roll Size
Solutions for thermal paper widths from 50mm to 1200mm, handling jumbo rolls up to 1200mm OD with precision core chucks.
Tension & Control Accessories
- Anti-static ionizing bars - Non-marring silicone rollers - Dust-free trim suction systems - Low-friction guide plates - Tension-controlled layon rollers
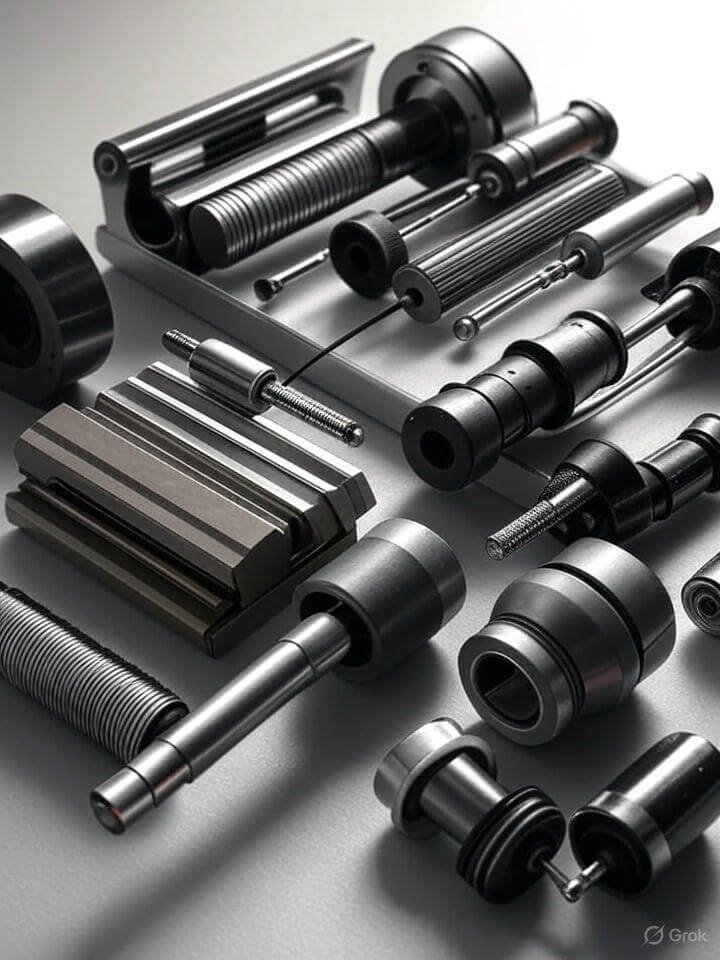
Our Manufacturing Prowess & R&D Capabilities
Production Scale & Qualifications
- Factory Area: Over 10,000 square meters dedicated to manufacturing high-precision slitters.
- Annual Capacity: 200+ high-quality slitting machines for various materials.
- Certifications: ISO 9001, CE, Multiple Patents for advanced slitting technology.
R&D and Innovation
- Dedicated R&D Team: 12+ experienced engineers focused on slitter machine innovation.
- Technical Collaborations: Partnering with leading universities and research institutes for cutting-edge slitting solutions.
- Innovation Focus: Continuous development of intelligent and automated slitting and rewinding machines for paper, film, and foil.
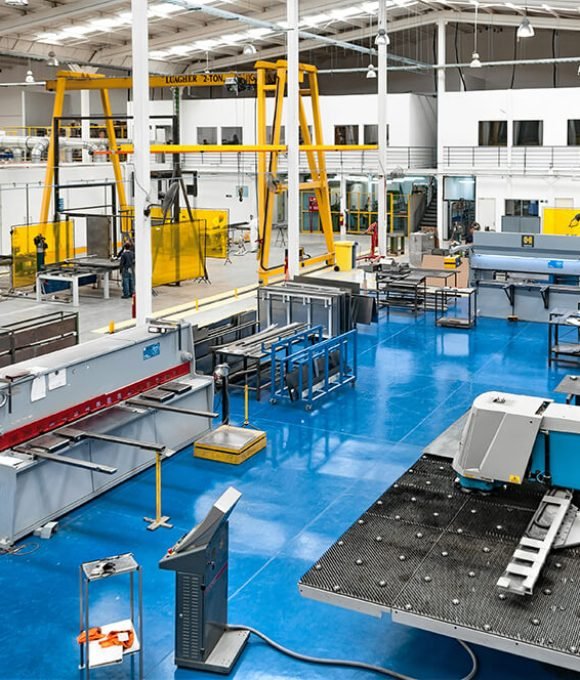
Quality Certifications
- ISO 9001:2015 Quality Management System
- CE Certification for European Market Compliance
- SGS Audited Supplier Status for all our slitting and rewinding machines.
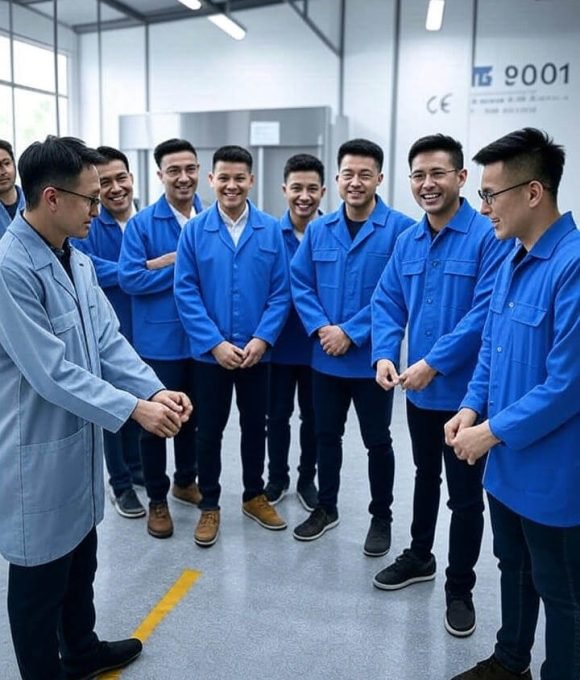
Unmatched After-Sales Service & Support
We have a growing network of overseas service points and authorized agents in Southeast Asia, Europe, and the Americas to ensure prompt local support for your slitting and rewinding machine.
Our Service Commitments
- 24/7 remote technical support and troubleshooting for your slitter.
- Scheduled preventive maintenance programs and on-site servicing for all slitting machines.
- Comprehensive operator training and detailed maintenance guides (e.g., slitter slider lubrication, film slitter knife care).
12+
Years of Experience
500+
Customer Cases
20+
Patented Technologies
98%
Customer Satisfaction
A Real-World Success Story:Sarah's Experience with Advanced Thermal Paper Slitting Technology
To showcase the remarkable potential of precision thermal paper slitting equipment, we present the inspiring journey of Ms. Sarah Thompson, a distinguished client from the United Kingdom, whose thermal paper distribution business achieved unprecedented growth after incorporating our state-of-the-art TSM-2800 Thermal Paper Slitting Machine into her operations.
Establishing the Foundation
Our professional relationship with Ms. Sarah began in early 2018 when she initially contacted our company regarding high-precision thermal paper converting solutions for her expanding receipt paper distribution enterprise. During this period, we were consolidating our manufacturing excellence in Wenzhou, Zhejiang Province, focusing specifically on advanced thermal paper processing machinery designed for commercial and industrial applications. Although preliminary discussions demonstrated significant potential, fluctuating market dynamics resulted in a temporary suspension of active negotiations. Nevertheless, in late 2019, Ms. Sarah reconnected with renewed interest as the digital payment revolution was accelerating demand for high-quality thermal receipt papers across retail sectors. Upon learning of her scheduled business trip to China for the International Paper Technology Exhibition, we extended an invitation to visit our comprehensive Wenzhou manufacturing complex—a strategic decision that ultimately established the foundation for an exceptionally successful long-term partnership.
Professional Reception and Comprehensive Facility Assessment
Ms. Sarah and her technical consultant received a professional welcome from our engineering director and international sales division upon their arrival at our advanced Wenzhou production facility. The detailed assessment included an exhaustive examination of our cutting-edge manufacturing operations, with specialized focus on thermal paper slitting and converting processes. This comprehensive evaluation encompassed our flagship TSM-2800 thermal paper slitting machine, alongside our integrated quality assurance systems and precision measuring equipment—machinery fundamental to Ms. Sarah’s objective of delivering premium thermal receipt papers for point-of-sale applications. The facility tour provided direct exposure to our technological capabilities and unwavering commitment to delivering superior thermal paper processing solutions.
Technical Excellence in Action: During the visit, Ms. Sarah witnessed the TSM-2800’s precision blade system operating at full capacity, achieving consistent tolerances of ±0.1mm across thermal paper widths ranging from 57mm to 80mm—exactly the specifications required for modern POS systems.
Confidence Through Technical Demonstration
Observing the TSM-2800 in continuous operation proved instrumental for Ms. Sarah’s decision-making process. She examined our precision engineering workshop and monitored the machine’s sophisticated thermal paper handling mechanisms, confirming that our organization represented a committed manufacturer capable of providing innovative, dependable equipment for the rapidly expanding thermal paper market. This technical transparency and demonstrated engineering expertise solidified her trust in our brand and comprehensive solutions portfolio.
Strategic Investment Decision
Thoroughly impressed by the TSM-2800’s advanced capabilities—specifically its automatic tension control system, razor-sharp slitting blades, and integrated edge trim removal features—Ms. Sarah made the strategic decision to acquire the machine. These sophisticated technologies perfectly aligned with her operational requirements for producing consistently precise thermal paper rolls that could satisfy demanding retail applications while maintaining optimal print quality and operational reliability standards.
Key Performance Indicators: The TSM-2800 demonstrated slitting speeds up to 300 meters per minute with zero defect rates during the demonstration, processing thermal paper grades from 48gsm to 65gsm without quality degradation.
Exceptional Business Transformation
Following the successful integration of the TSM-2800, Ms. Sarah’s thermal paper distribution operations have achieved remarkable expansion and market recognition. The machine has established itself as the cornerstone of her production infrastructure, consistently delivering premium thermal receipt papers for restaurants, retail chains, banking institutions, and hospitality venues throughout the United Kingdom. Her thermal papers are now utilized across diverse applications ranging from grocery store receipts and restaurant orders to banking transaction records and parking tickets. Combined with our comprehensive technical support services, the TSM-2800 has enabled Ms. Sarah to quadruple her production output while achieving unprecedented quality consistency, resulting in her company “PrecisionThermal UK Limited” receiving the prestigious “British Retail Technology Excellence Award” for outstanding supplier performance. Her extraordinary achievements exemplify the machine’s transformative impact within the thermal paper processing industry and demonstrate the tangible benefits of investing in advanced slitting technology.
Market Impact: Within 18 months of installation, Ms. Sarah’s company secured contracts with three major UK retail chains, processing over 2.5 million meters of thermal paper monthly and establishing herself as a leading supplier in the competitive thermal receipt paper market.
What is a thermal paper slitting machine?
What types of thermal paper can it handle?
What roll sizes can be slit and rewound?
What is the typical speed of a thermal paper slitter?
How is curling of the paper prevented during slitting?
Does the machine generate a lot of dust?
Can the machine be adjusted for different paper widths?
Complete Guide to Choosing a Thermal Paper Slitting Machine
Thermal paper slitting machines are essential for converting large parent rolls of thermal paper into precise, finished sizes for POS systems, receipt printers, and various thermal printing applications. Whether you’re producing standard receipt rolls, cash register paper, or specialized thermal labels, choosing the right slitting machine ensures optimal production efficiency, cutting accuracy, and roll quality. This comprehensive guide covers the critical factors to consider when purchasing a thermal paper slitting machine.
- 1. Understanding Your Thermal Paper Production Requirements
- 2. Key Machine Features to Evaluate
- 3. Selecting the Right Machine Manufacturer
- 4. Cost Considerations and ROI
- 5. Other Important Factors
- 6. Market Trends and Future Opportunities-trends">6. Market Trends and Future Opportunities
- Thermal Paper Slitter Machine Comparison Table
1. Understanding Your Thermal Paper Production Requirements
Start with a thorough assessment of your thermal paper production workflow:
- Paper Grade: Standard thermal paper, premium thermal paper, or top-coated thermal paper—each requires specific blade settings and handling parameters.
- Parent Roll Specifications: Typical thermal paper slitters handle web widths up to 1650 mm and roll diameters of 1000–1500 mm.
- Finished Roll Dimensions: Define target widths (from 38mm for receipt rolls to 216mm for wide-format applications) and core sizes (12mm to 76mm).
- Production Speed: Operating speeds of 200–500 m/min are common, depending on paper grade, width, and quality requirements.
2. Key Machine Features to Evaluate
The machine’s technical capabilities directly impact your production efficiency and thermal paper quality. Essential features include:
- Slitting Technology: Razor slitting for clean edges on thermal coatings, with pneumatic or servo-controlled blade positioning.
- Rewinding Systems: Surface rewinding or center rewinding options, with precise tension control to prevent coating damage.
- Tension Management: Multi-zone tension control with load cells ensures consistent roll density without compromising thermal coating integrity.
- Edge Trimming: Automatic waste matrix stripping and disposal systems for efficient operation.
- Quality Control: Web inspection systems for detecting coating defects, holes, or contamination in thermal paper.
3. Selecting the Right Machine Manufacturer
Partner with a supplier who specializes in thermal paper converting and provides comprehensive support:
- Thermal Paper Expertise: Look for manufacturers with proven experience in thermal paper handling and coating protection.
- Machine Customization: Ensure the supplier can configure unwind systems, rewinding methods, and quality control features for your specific thermal paper grades.
- Global Service Network: Verify availability of technical support, spare parts, and maintenance services in your operating region.
- Training and Commissioning: Comprehensive operator training and machine commissioning should be included in the purchase package.
4. Cost Considerations and ROI
A quality thermal paper slitting machine delivers long-term value through improved efficiency and reduced waste. Consider:
- Initial Investment: Entry-level machines for basic thermal paper, while high-speed automated systems offer better returns for large-volume operations.
- Operational Expenses: Factor in blade replacement costs, maintenance intervals, and energy consumption.
- Waste Reduction: Precision slitting and quality control systems minimize material waste and rework costs.
- Labor Optimization: Automated features reduce operator requirements and training time while improving consistency.
5. Other Important Factors
- Coating Protection: Anti-static systems and controlled environment features protect thermal coatings during processing.
- Roll Handling: Automatic core loading and finished roll removal systems improve productivity and reduce manual handling.
- Dust Management: Effective dust extraction systems prevent contamination of thermal coatings and maintain machine performance.
- Safety Features: Proper guarding, emergency stops, and operator safety systems are essential for thermal paper processing environments.
6. Market Trends and Future Opportunities
- Digital Receipts: While digital alternatives grow, thermal paper remains essential for retail, hospitality, and logistics applications.
- Eco-Friendly Thermal Paper: BPA-free and recyclable thermal papers require updated slitting technologies and handling procedures.
- Specialty Applications: Medical thermal paper, shipping labels, and industrial tags demand higher precision and quality control.
- Emerging Markets: Growing retail sectors in Asia, Africa, and Latin America drive demand for thermal paper converting capacity.
Thermal Paper Slitter Machine Comparison Table
Evaluation Factor | Details | Why It Matters |
---|---|---|
Thermal Coating Protection | Anti-static systems, controlled tension, clean environment | Prevents coating damage and maintains print quality |
Slitting Precision | Razor slitting with servo positioning | Ensures clean edges and consistent roll widths |
Rewinding Control | Multi-zone tension, surface or center winding | Maintains roll quality without coating damage |
Quality Inspection | Web inspection, defect detection, coating monitoring | Ensures thermal paper meets print performance standards |
Production Flexibility | Quick job changeover, multiple core sizes, variable widths | Adapts to diverse thermal paper product requirements |
Selecting the optimal thermal paper slitting machine requires careful evaluation of your production requirements, technical specifications, and long-term business objectives. From protecting thermal coatings during processing to achieving precise slitting accuracy and maintaining consistent quality, every aspect affects your operational success. As global demand for thermal paper continues across retail, logistics, and specialty applications, investing in a reliable and well-supported slitting machine is crucial for maintaining competitiveness in this evolving market.