Advanced Water-Cooled Rollers for Precision Temperature Management
Featured Water-Cooled Rollers
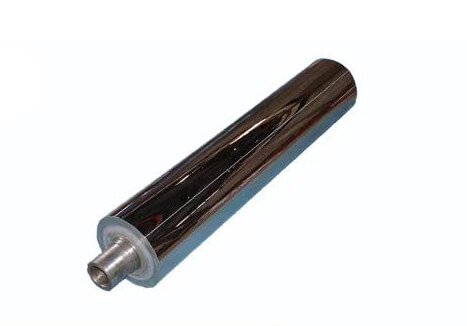
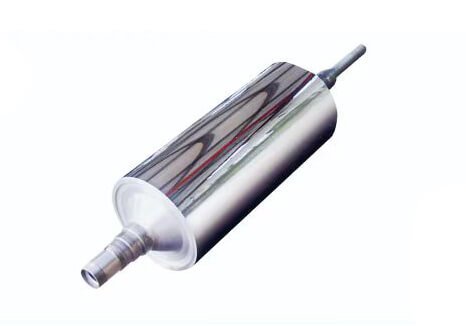
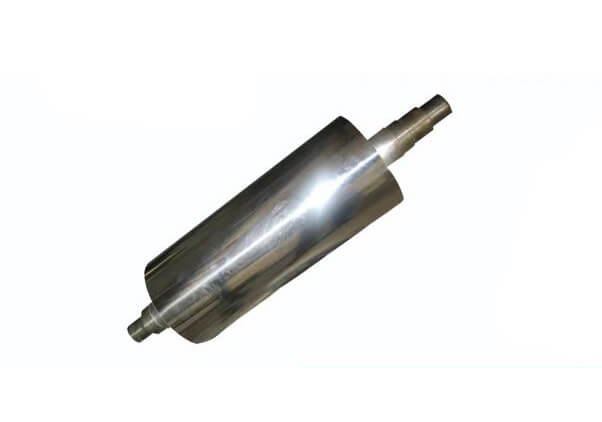
Product Specifications – Water-Cooled Rollers | |
---|---|
Materials | Aluminum Alloy, 45# Steel, 20# Steel, 40Cr Steel, 304 Stainless Steel |
Cooling Method | Water cooling with single or dual-end inlet/outlet design; optional internal spiral tubing; available in single or double-layer structures |
Key Features | Water-cooled rollers are used to cool materials before winding to reduce deformation caused by shrinkage during cooling, especially in calendered film or adhesive tape coating processes |
Surface Finishing Options | Hard Chrome Plating, Teflon Coating, Ceramic Coating |
Water-Cooled Rollers for Precision Cooling
Plastic Film Extrusion & Casting
Used as chill rollers in film extrusion and casting lines to rapidly cool and solidify newly extruded films, ensuring accurate thickness, optical clarity, and flatness. Key Benefit: Enhances dimensional stability and increases production speed.
Coating & Drying Lines
Placed after high-temperature ovens to cool substrates before rewinding, preventing sticking, blocking, or coating displacement. Key Benefit: Maintains coating quality and avoids downstream defects.
Laminating Applications
Used during or after lamination—especially with hot melt adhesives or heat-sensitive layers—to manage web temperature and minimize warping. Key Benefit: Supports uniform bonding and protects delicate laminates.
Printing & Embossing
Ideal for UV curing, flexographic and gravure printing, as well as embossing or calendering lines. Maintains substrate shape and ensures precision pattern retention. Key Benefit: Improves registration accuracy and ensures clean, consistent finishes.
Engineered Performance: Inside Water-Cooled Roller Technology
1. Precision Core Fabrication
2. High-Integrity Cladding Process
3. Advanced Surface Finishing
4. Performance-Driven Material Pairing
5. Built for Industrial Versatility
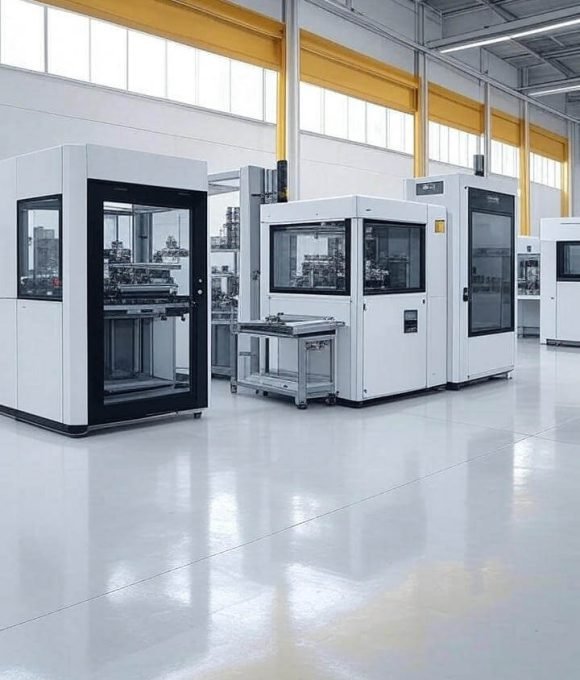
Get Our Free Samples
What Are Water-Cooled Rollers?
Water-cooled rollers are cylindrical mechanical components that incorporate internal cooling systems to maintain controlled surface temperatures during operation. Unlike conventional rollers that rely on ambient air cooling, these systems actively circulate coolant—typically water or specialized cooling fluids—through internal channels to achieve precise temperature regulation.
The fundamental characteristics of water-cooled rollers include superior heat dissipation capabilities, consistent surface temperatures, reduced thermal expansion, and enhanced dimensional stability. These rollers feature robust construction with internal coolant passages, precision-machined surfaces, and specialized sealing systems to prevent coolant leakage while maintaining optimal performance.
The cooling mechanism operates on the principle of forced convection, where coolant flows through strategically designed internal channels, absorbing heat from the roller surface and transferring it away from the processing zone. This continuous heat removal enables sustained operation at high processing speeds while maintaining material quality and preventing thermal-related defects.
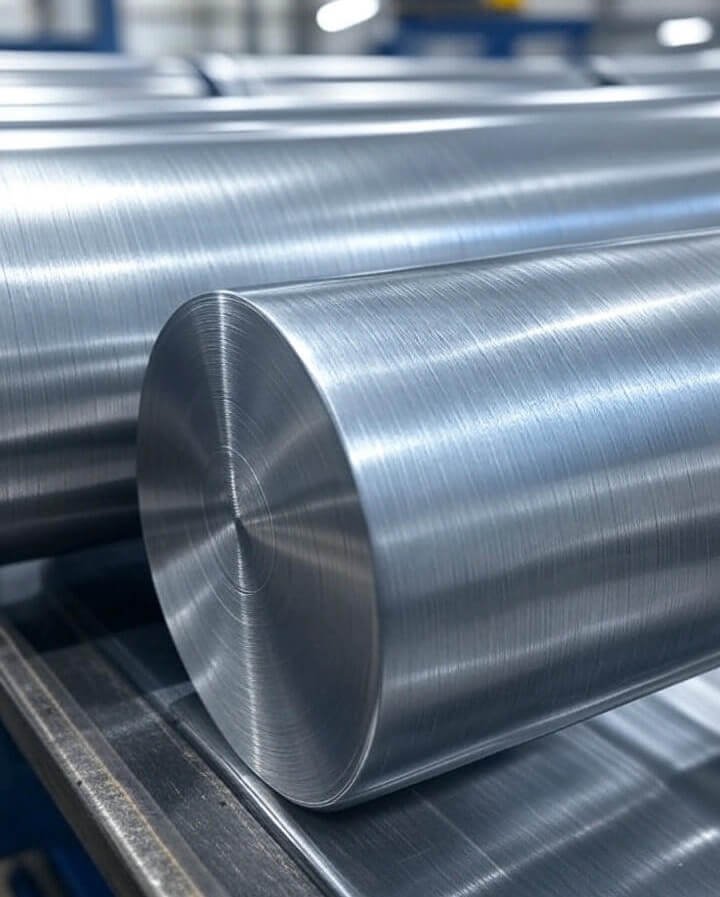
Different Types and Specifications of Water-Cooled Rollers
Types of Water-Cooled Rollers | |||
---|---|---|---|
Type | Description | Applications | Key Specifications |
Standard Water-Cooled Rollers | Basic design with internal fluid channels for moderate cooling or heating. | General material handling, low-intensity tasks | Stainless steel or carbon steel, 1.5–6mm cladding, standard surface finish (32–125 Ra). |
Double Shell Spiral Baffle Rollers (DSSB) | Feature an inner shell with spiral baffles for enhanced heat transfer efficiency. | Film extrusion, paper drying, high-performance tasks | Stainless steel (304/316L), 3–10mm cladding, precision finish (4–32 Ra). |
Heated Rollers | Use hot oil or steam for high-temperature applications. | Adhesive activation, textile finishing | Heat-resistant stainless steel, internal heating elements, customized surface finishes. |
Chill Rollers | Designed for rapid cooling using chilled water or glycol. | Film casting, metal quenching | High thermal conductivity materials, mirror polish (4–8 Ra). |
Customized Rollers | Tailored designs for unique applications, including special materials or coatings. | Specialized processes, extreme environments | Advanced alloys (e.g., 2205, 904L), custom configurations. |
Specifications
- Diameter and Length: Vary based on material width and process requirements, typically ranging from 100mm to over 4,000mm in length.
- Material: Stainless steel (e.g., 304, 316L) for corrosion resistance; carbon steel or aluminum for cost-effective cores.
- Surface Finish: Ranges from standard (125–250 Ra) to mirror polish (4–8 Ra) for hygiene-critical applications.
- Cooling Capacity: Determined by fluid type, flow rate, and roller design (e.g., mono-flow or dual-flow systems).
- Temperature Range: Up to 800°C for heated rollers; chilled rollers can maintain sub-zero temperatures with glycol.
Technical Parameters and Their Significance
Technical Parameters and Their Significance | ||
---|---|---|
Parameter | Significance | Typical Values |
Cooling Fluid | Determines heat transfer efficiency; must be compatible with process and materials. | Water, glycol, oil; 5–80°C for cooling fluids. |
Roller Material | Affects thermal conductivity, corrosion resistance, and durability. | Stainless steel (304, 316L), carbon steel. |
Surface Finish | Impacts heat transfer, cleanability, and material contact. | 4–250 Ra, depending on application. |
Dimensional Accuracy | Ensures precise material handling and process consistency. | ±0.1mm (standard), ±0.025mm (precision). |
Temperature Uniformity | Critical for consistent processing across material width. | ±1°F across roll face in advanced designs. |
Bond Strength (if clad) | Ensures cladding integrity under thermal and mechanical stress. | 140–280 MPa, verified by destructive testing. |
Operational Temperature | Defines limits for continuous and intermittent use. | Up to 800°C for heated rollers. |
These parameters guide the selection process, ensuring rollers perform reliably under specific conditions.
Industrial Applications Across Various Sectors
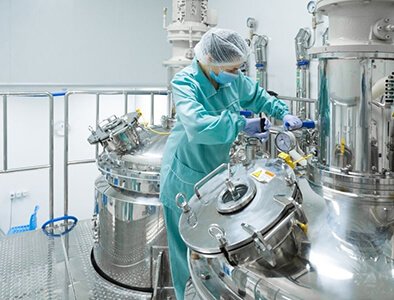
Food Processing Industry
Used in cooling and shaping products like pasta, candies, and baked goods. The smooth, stainless steel surfaces meet FDA hygiene standards, preventing bacterial growth and facilitating cleaning (Roll Technology).
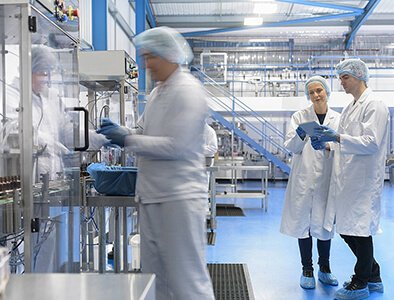
Chemical Processing Industry
Control reactions and curing for adhesives, sealants, and paints, ensuring consistent quality and preventing unwanted reactions (R2R Engineering).
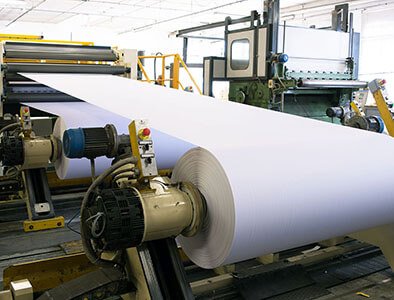
Paper and Pulp
Facilitate drying and calendering, preventing wrinkling and ensuring uniform paper quality (Saueressig Group).
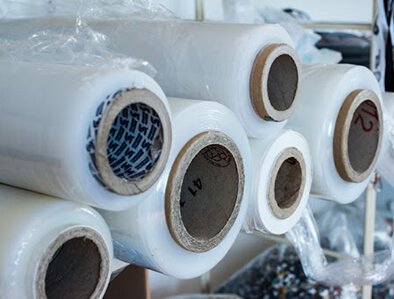
Plastics and Films
Cool extruded films and sheets, setting properties like strength and clarity (Empire Rollers).
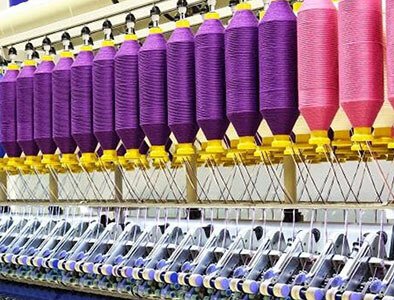
Textile Industry
Support dyeing and finishing, ensuring even dye absorption and fabric quality (Mebatex).
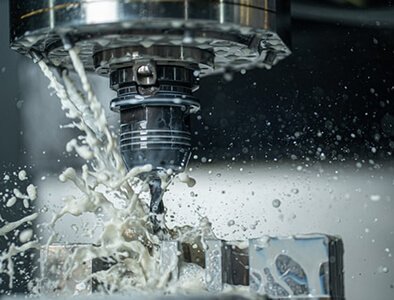
Metalworking
Used in quenching to enhance metal hardness and durability, critical for steel industry applications (Fai Ftc).
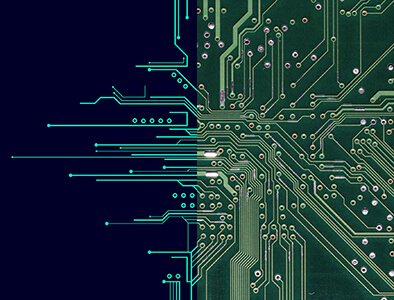
Electronics
Maintain precise temperatures for manufacturing lithium-ion battery films, ensuring material integrity (Delta T Systems).
Supplier Selection and Quality Assurance for Water-Cooled Rollers
Selecting Quality Water-Cooled Roller Manufacturers
Technical Capability Assessment
Technical capability assessment includes manufacturing equipment, engineering expertise, and quality control systems. Manufacturers should demonstrate capability to meet specification requirements and provide technical support throughout the product lifecycle.
Quality System Evaluation
Quality system evaluation should verify ISO certification, quality control procedures, and testing capabilities. Documented quality systems ensure consistent product quality and provide confidence in supplier capabilities.
Service Support Capabilities
Service support capabilities include technical assistance, spare parts availability, and repair services. Long-term support requirements may exceed initial product costs, making service capability a critical selection factor.
Financial Stability and Business Continuity
Financial stability and business continuity considerations ensure the supplier can provide ongoing support throughout the product lifecycle. Supplier financial health impacts availability of warranty support and long-term service capability.
Key Factors in Supplier Evaluation
Technical Expertise
Technical expertise encompasses engineering capability, application knowledge, and problem-solving ability.
Manufacturing Capability
Manufacturing capability includes equipment sophistication, capacity, and quality control systems. Advanced manufacturing capabilities often correlate with superior product quality and shorter delivery times.
Customer Service
Customer service and support capabilities significantly impact user satisfaction and long-term costs. Responsive technical support, readily available spare parts, and comprehensive documentation improve operational efficiency.
Cost Competitiveness
Cost competitiveness must be evaluated in the context of total lifecycle costs, including initial purchase price, installation costs, operating costs, and maintenance requirements. Lowest initial cost may not represent best value when total costs are considered.
Delivery Performance and Reliability
Delivery performance and reliability impact production scheduling and inventory requirements. Reliable suppliers with consistent delivery performance reduce operational complexity and improve planning effectiveness.
Our Manufacturing Prowess & R&D Capabilities
Production Scale & Qualifications
- Factory Area: Over 10,000 square meters dedicated to manufacturing high-precision slitters and Accessories
- Annual Capacity: 200+ high-quality slitting machines for various materials.
- Certifications: ISO 9001, CE, Multiple Patents for advanced slitting technology.
R&D and Innovation
- Dedicated R&D Team: 12+ experienced engineers focused on slitter machine innovation.
- Technical Collaborations: Partnering with leading universities and research institutes for cutting-edge slitting solutions.
- Innovation Focus: Continuous development of intelligent and automated slitting and rewinding machines for paper, film, and foil.
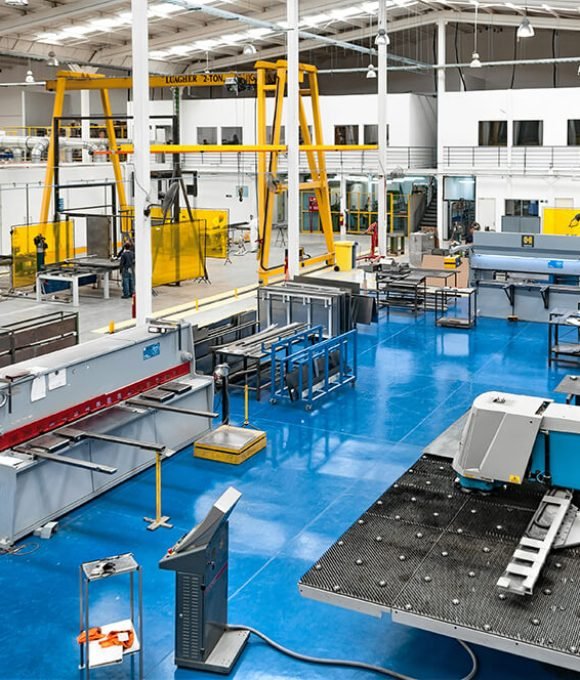
Quality Certifications
- ISO 9001:2015 Quality Management System
- CE Certification for European Market Compliance
- SGS Audited Supplier Status for all our slitting and rewinding machines.
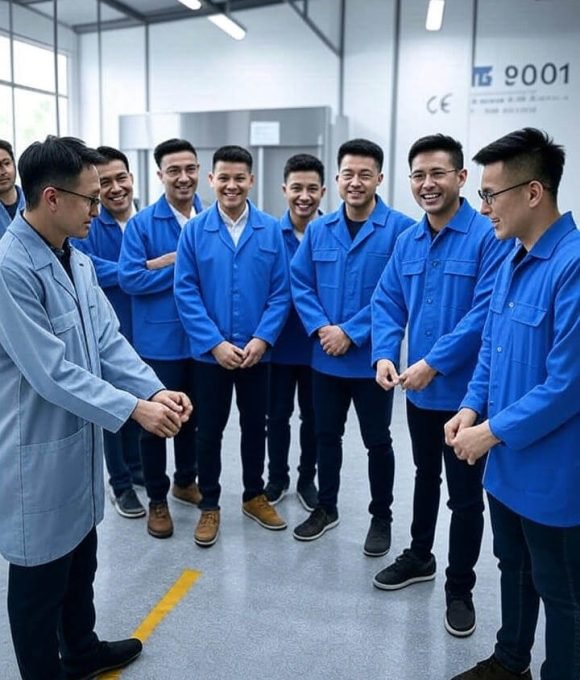
Unmatched After-Sales Service & Support
We have a growing network of overseas service points and authorized agents in Southeast Asia, Europe, and the Americas to ensure prompt local support for your slitting and rewinding machine.
Our Service Commitments
- 24/7 remote technical support and troubleshooting for your slitter.
- Scheduled preventive maintenance programs and on-site servicing for all slitting machines.
- Comprehensive operator training and detailed maintenance guides (e.g., slitter slider lubrication, film slitter knife care).